Automated cleaning and solid netting materials are being put into play as maintenance costs rise
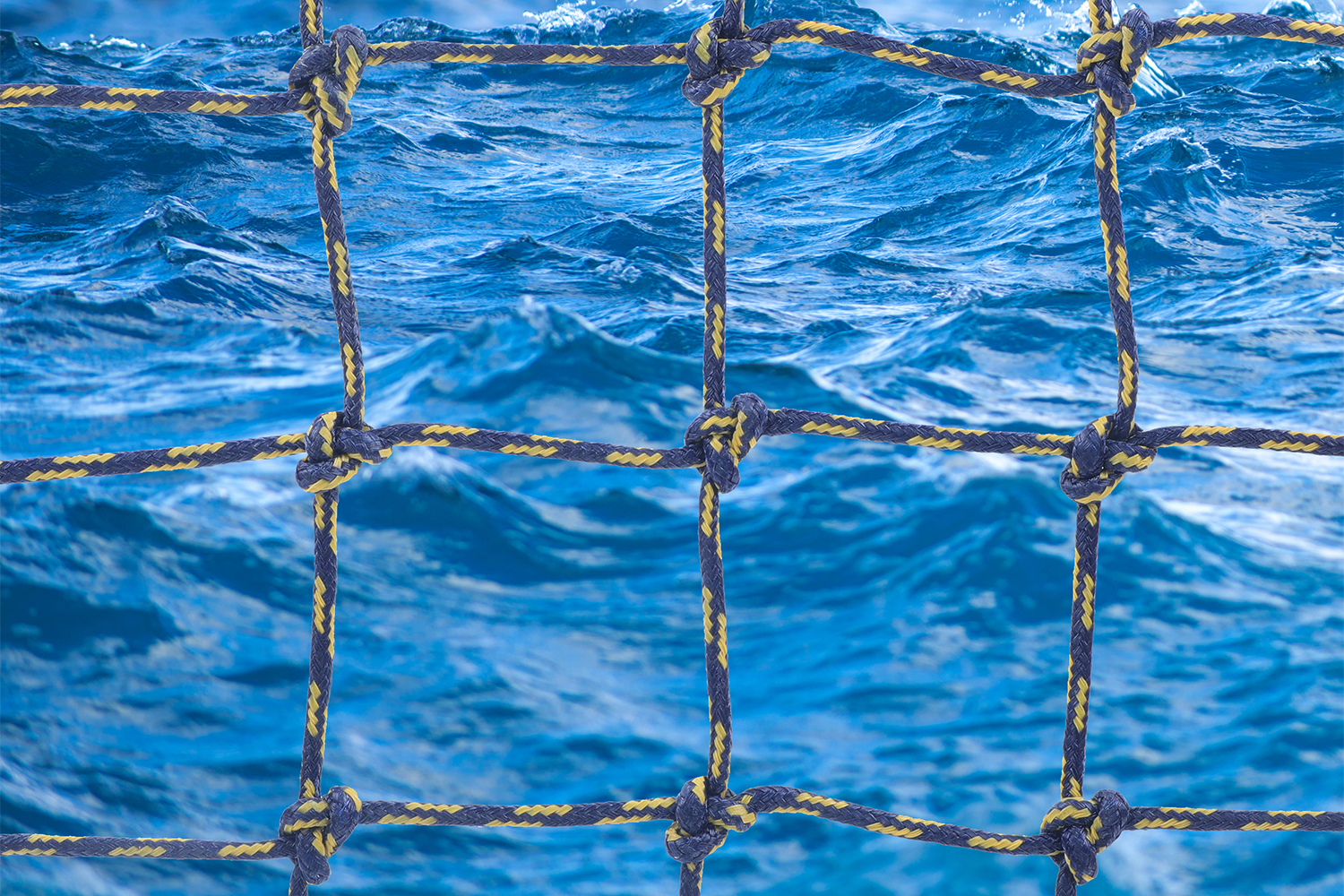
Feed and animal health are aquaculture’s top operating expenses but the sector is now paying more attention to net pen innovations for efficient farming, reduced carbon footprint and better fish welfare at sea.
Net pens must be kept clean to prevent the build-up of algae and other organic matter. Traditionally, this was done by lifting the pens out of the ocean and drying them in the wind or under the sun.
Today, net pens are mechanically cleaned with high-pressure equipment but this is labor-intensive and a stressor for fish. Aquaculture is witnessing a shift in cleaning operations, according to Mikkel Pedersen, CEO and founder of Norwegian aquatech firm Probotic, which has introduced a new, autonomous robot that cleans and inspects net pens.
Having identified the challenges of high-pressure cleaners, Pedersen’s solution was not just to clean, but to ensure that net pens would remain perpetually pristine.
“Biofouling, characterized by the accumulation of marine species that block a net, is a significant challenge in net pens,” Pedersen told the Advocate. “Traditional remote and manual cleaning systems are reactive, often addressing the issue when it’s too late. Our philosophy diverges from merely cleaning; we aim to maintain cleanliness. This proactive stance, powered by artificial intelligence (AI), autonomy and robotics, is a game-changer. I firmly believe that such proactive automation will define the future of most production processes. While our current model involves a human-operated ops-center overseeing the robots, we envision a future where the system is entirely plug-and-play, requiring minimal human intervention.”
The robot primarily focuses on the top 5 meters of a pen where biofouling is most aggressive due to the interplay of light and sea temperature. However, its robust design ensures that it also functions at depths surpassing 100 meters. An integrated remote station offers real-time visuals from the pens, which enables pre-emptive problem-solving capabilities and the ability to inspect the nets.
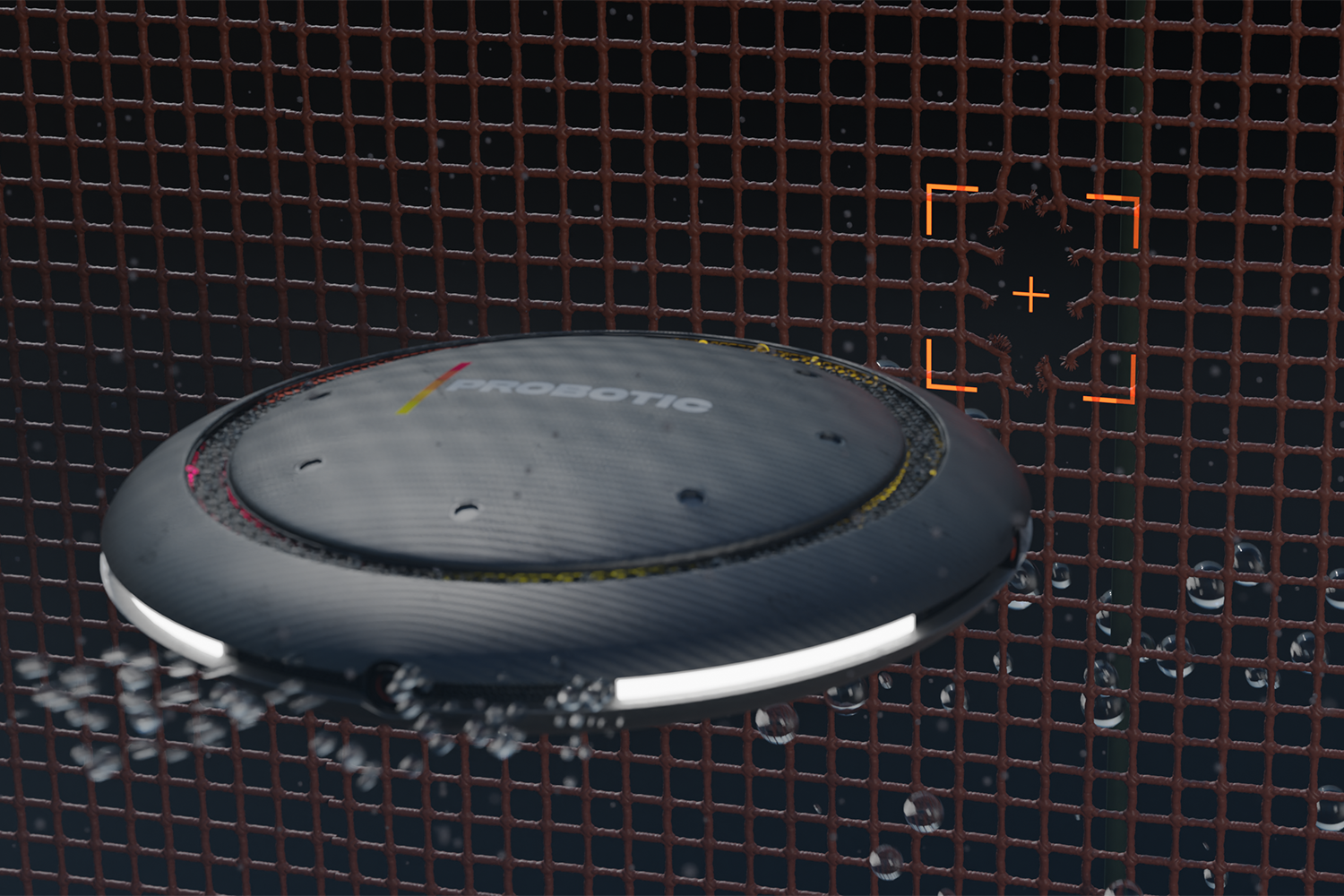
“Another distinguishing feature of the robot is its emergency shutdown capability, ensuring an immediate power cut-off when deemed necessary,” said Pedersen. “Its design, characterized by its rounded edges, is meticulously crafted to minimize potential harm to the nets. Our commitment has always been to conceive a design that’s both net- and fish-friendly.”
In a departure from traditional sales models, Probotic champions a rental approach. Fish farmers can avail themselves of a service called CLEAN & SAFE NETs, eliminating the need to purchase equipment. This model underscores Probotic’s responsibility to guarantee the robot’s seamless operation and drive continuous innovation.
“Our primary offering is a clean net,” said Pedersen. “The more refined and efficient our system evolves to be, the more lucrative our returns. It’s a symbiotic relationship, ensuring mutual benefits for both Probotic and our esteemed clients.”
Another cleaning innovation is also addressing the biofouling problem. Remora Robotics, a Norwegian technology firm in Stavanger, works with salmon and halibut farms. The company’s system is an autonomous robot with a thruster that enables it to travel around the pens. It also has a brushing mechanism that scrubs the nets inside and out from top to bottom. The robot can be operated during normal working hours, early in the morning or late at night.
In southern Norway, increased light during the summer results in higher sea temperatures and accelerates biofouling. Mitigation can involve cleaning with a high-pressure spray almost every week, but this stresses the fish and interrupts feeding, making them stop eating and slowing growth. The Remora Robotics system avoids such problems.
“Instead of removing biofouling each week, we prevent it from occurring in the first place,” said Svein Erik Gregersen, chief operating officer at Remora Robotics. “Farmers need a cleaning solution that doesn’t damage their pens and allows their fish to be healthy and free from stress.”
As well as preventing biofouling, the robot can collect data on the marine environment and detect and report holes through cameras and AI. Discussing future plans, Gregersen said that Remora Robotics is preparing to scale up its robot and looking at different improvements to increase its lifetime at sea. Several projects are also underway to maximize the effects of brushing and the impacts of brushing on water quality. Innovations such as these are likely to draw further attention, with biofouling remaining a serious issue.
“A fish farm only pressure cleans because previously there has been no other alternative,” said Gregersen. “When biofouling becomes severe, the oxygen levels in the pens would decrease, fish mortality would increase significantly, and the farmers would lose production. In some ways, biofouling is even worse than disease in that you could lose everything if your pens aren’t cleaned correctly.”
Pedersen agrees.
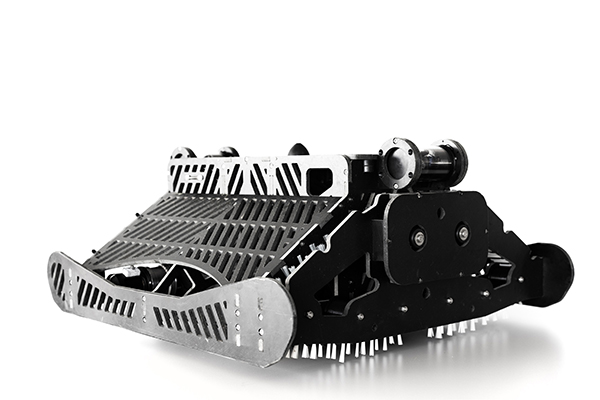
“Biofouling dynamics differ based on location,” he said. “It’s a multifaceted issue, making it challenging to pinpoint a singular cause and effect. For instance, if a pen houses weaker fish, cleaning operations might result in significant fatalities. However, robust and healthy fish might only experience a temporary reduction in feeding post-cleaning. Regardless of these nuances, there’s unanimous agreement among most aquaculturists about the severity of the biofouling challenge.”
Gopakumar Menon, associate vice president at Garware Technical Fibres Ltd (GTFL) in Vancouver, Canada, says that farmers and producers are increasingly keen to adapt to new solutions and work closely with manufacturers when it comes to nets, in order to resolve operational challenges, reduce cleaning and operations costs and increase profitability.
GTFL designs application-focused nets for commercial fishing and aquaculture to protect stock from predators, eliminate fish escapes, reduce biofouling and carbon footprint and enhance fish health. Among its innovations are nets made of high-density polyethylene (HDPE) in which metallic copper is built into the fibers to reduce biofouling. This prevents the copper from falling off and contaminating the surrounding environment, resulting in reduced growth on the nets and less need for washing. The result is better conditions for the fish with less disturbance from cleaning and reduced operational expenses in cleaning nets.
GTFL is also addressing another problem – predation on fish farms.
“This is more significant today compared to the last five to 10 years,” said Menon. “It can result in huge losses, in some cases around 5,000 fish per week. Traditionally, producers would increase twine thickness or mesh-breaking strength on the nets, but this doesn’t solve the problem. We work to understand predator behavior and design our nets based on the parameters required to prevent predator attacks.”
GTFL’s nets are made of nylon and HDPE. Although nylon is stronger and has been the traditional polymer, by nature it shrinks and its filaments are thin, making it increasingly likely to break. It also only lasts for around five years, has poor abrasion resistance in wet conditions and breaking strength is reduced by 10 percent when water is absorbed, making it unsuitable for protection against predators. HDPE, on the other hand, lasts longer with a lower carbon footprint than a kilogram of nylon, while repair and maintenance costs are reduced due to its high abrasion resistance and longer lifespan.
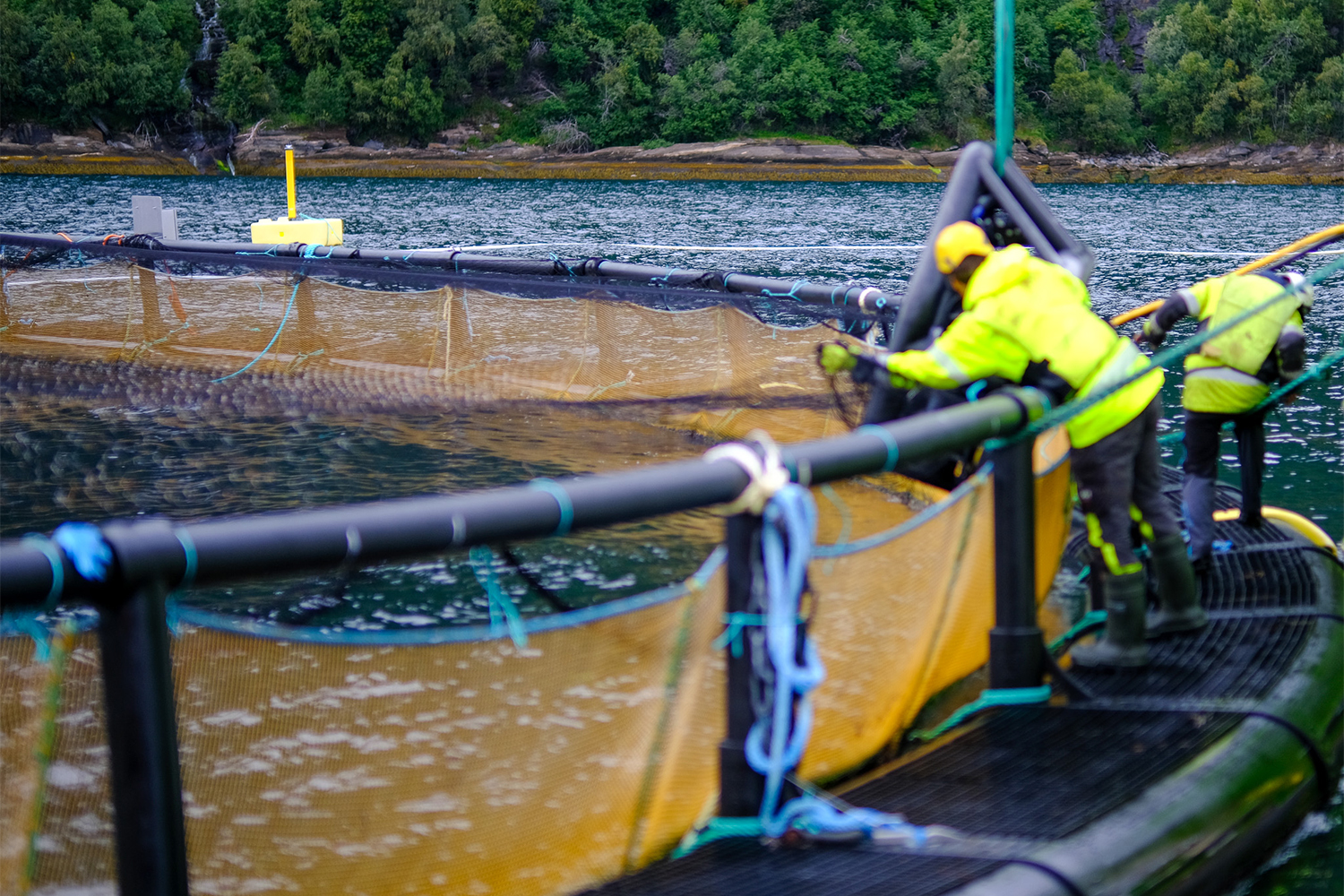
However, there is no standard material when it comes to nets, said Menon. The key is to work closely with customers to understand their needs and develop a customized product based on feedback.
“Our customers work in different environments with different infrastructure, operation strategies and challenges, so our nets must be developed in line with the behavior of a particular predator or biofouling issue,” he said. “Our products are highly customized and tailor-made for specific applications. What’s important is that we understand how our customers operate, the environment they operate in, and offer them a product that solves operational challenges, reduces cost and increases profitability.”
GTFL has extensive ongoing trials and research and development programs worldwide. Work is also underway on a new net that can inform customers in advance through SMS or email when the mesh breaks and the extent of any breakages. Trials in Norway and Scotland show that this type of net can prevent fish from escaping and enable a diver to fix an exact spot. This saves time and prevents the diver from having to continuously inspect the net and search for the breakage. GTFL is now looking to build a fully-fledged net in Chile.
Customers have experienced high return on investment, which is indicative of what GTFL strives for, said Menon: “It all starts with the voice of the customer. We are constantly redefining and fine-tuning our products to make them better. If we can understand our customers’ operations, site conditions, infrastructure and help address the challenges they face, we are doing something right.”
Now that you've reached the end of the article ...
… please consider supporting GSA’s mission to advance responsible seafood practices through education, advocacy and third-party assurances. The Advocate aims to document the evolution of responsible seafood practices and share the expansive knowledge of our vast network of contributors.
By becoming a Global Seafood Alliance member, you’re ensuring that all of the pre-competitive work we do through member benefits, resources and events can continue. Individual membership costs just $50 a year.
Not a GSA member? Join us.
Author
-
Bonnie Waycott
Correspondent Bonnie Waycott became interested in marine life after learning to snorkel on the Sea of Japan coast near her mother’s hometown. She specializes in aquaculture and fisheries with a particular focus on Japan, and has a keen interest in Tohoku’s aquaculture recovery following the 2011 Great East Japan Earthquake and Tsunami.
Tagged With
Related Posts
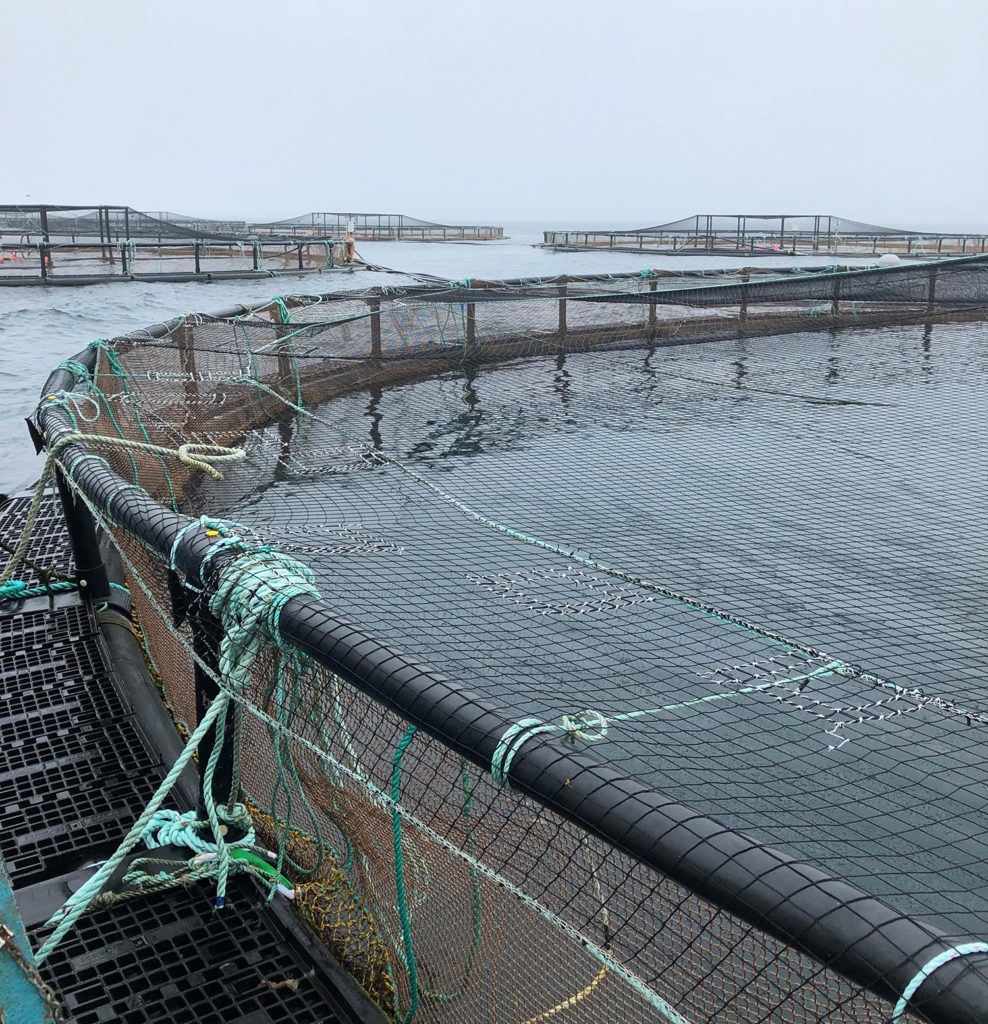
Innovation & Investment
Net gains in aquaculture net technology
The aquaculture industry is paying greater attention to net technology, in terms of materials and maintenance, because of its impact on the bottom line.
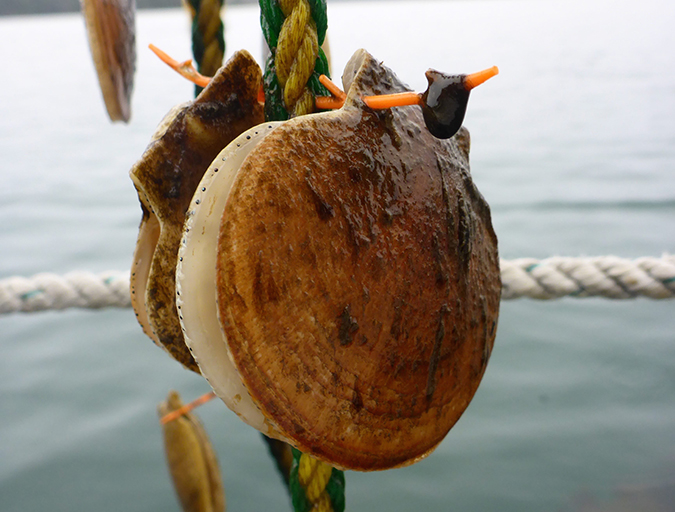
Innovation & Investment
Maine scallop farmers get the hang of Japanese technique
Thanks in part to a unique “sister state” relationship that Maine shares with Aomori Prefecture, a scallop farming technique and related equipment developed in Japan are headed to the United States. Using the equipment could save growers time and money and could signal the birth of a new industry.
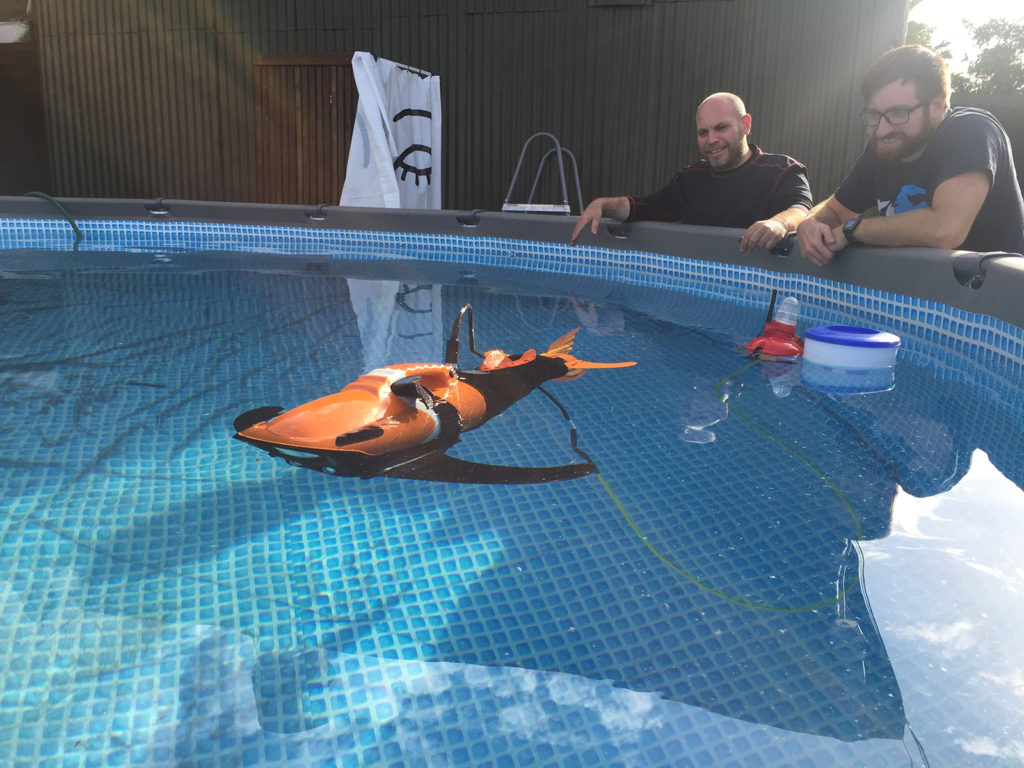
Innovation & Investment
Fish farmers turn to drones for health, feed monitoring
Two technology startups are offering unique fish-monitoring solutions for aquaculture producers. Using algorithms, drones and computer vision software, Aquaai and Aquabyte aim to take labor-intensive and error-prone tasks out of human hands.
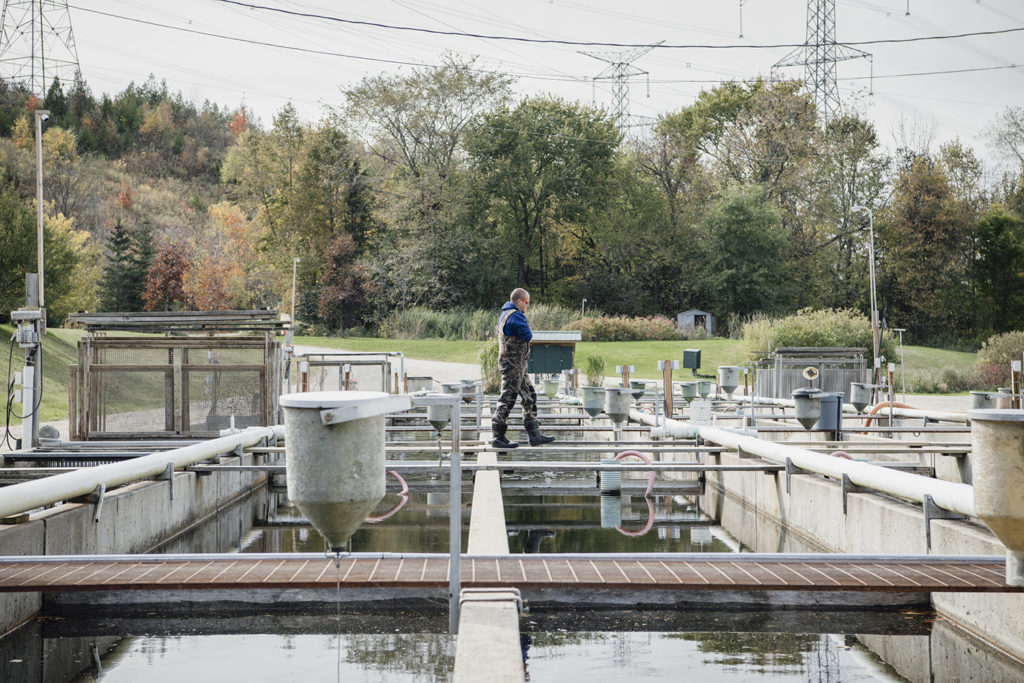
Innovation & Investment
Technology allowing aquaculture to do social distancing
Data tools and remotely operated feeding systems are just a couple ways aquaculture is accomplishing social distancing during the coronavirus pandemic.