Prototype system proved to be biosecure against WSSV

The Nicaragua Small Shrimp Producer Assistance Program was designed to help the country’s shrimp farmers improve their production technologies and management strategies, and promote the sustainable redevelopment of the industry after the introduction of viral diseases and devastation caused by Hurricane Mitch.
In 2001, its main projects included building a closed, zero water-exchange shrimp production system to demonstrate the concepts and practices of the new technology. It also included the promotion of the economic viability of the system by introducing the results of the demonstration project to commercial financial institutions and local development agencies.
The United States Agency for International Development, and National Oceanic and Atmospheric Administration enlisted Michigan Sea Grant to manage the project. Subcontractors included the Florida Sea Grant College in Florida, USA. Camanica, a local shrimp-farming and processing company, managed the day-to-day operations of the prototype farm.
Prototype farm
The demonstration farm was built during the first half of 2001 by Aquatic Designs, Inc. of Michigan, USA near Estero Real in west-central Nicaragua at the existing University of Central America shrimp farm in Puerto Morazán. The project included four 0.5-ha production ponds, two 1-ha settling ponds, a pump station, generator shed, feed storage, laboratory, and office.
The ponds were built with a center drain for harvesting and removal of solids during the production cycle. The dikes had a crown width of 5 meters, with an interior slope of 1:1 and exterior slope of 2.5:1. Settling ponds had two drains: one to release water to the estuary once sediments were removed and another to refill the ponds. Each pond was lined with high-density polyethylene (HDPE) and had 10 2-hp paddlewheel aerators.
Biosecurity measures
Biosecurity measures used included water filtration, pond preparation, the use of resistant or pathogen-free postlarvae (PL), farm quarantine, disinfection of hands and feet upon entrance, and reduction of birds in the pond area.
Water filtration

Water introduced into the system flowed through a series of filters to eliminate hosts that could harbor shrimp viruses. Water from the Estero Real was passed through a 500-μ filter into the receiving and distribution canal and settling ponds. From the settling ponds, water was filtered at 300 μ into a secondary reservoir and then at 200 μ into a tertiary reservoir. Finally, water entered the grow-out ponds through a 100-μ filter.
Pond preparation
Water was kept for a two-week “resting” period in the settling ponds, where plankton samples were collected and tested for White Spot Shrimp Virus (WSSV). Initially there were positive results for WSSV, but during the second week, all samples tested negative. The settling ponds were not sterilized to test the effectiveness of the water filtration/resting treatment in preventing WSSV, or fertilized to desired levels due to time constraints. Ponds were stocked with PL almost immediately after filling.
Pathogen-free postlarvae
Seedstock resistant to Taura Syndrome Virus (TSV) was procured from laboratories in Panama. Specific pathogen-free PL from the United States were not used due to their historically low survivals in regions where TSV is present. Ponds were stocked at high rates (109-130 PL per square meter) to compensate for TSV-induced mortality.
Disinfection

To reduce the risk of contamination from nearby farms and ponds, gates were set up at the entrance to the project with an iodine bath. All entrants to the farm were to wash their hands and shoes at the gate.
Bird predation
The 1:1 interior pond slopes and slippery HDPE liners prevented predation by birds along the shoreline. With small ponds and the constant presence of aerators and workers, major predators such as cormorants and herons were controlled. However, small gulls and terns remained a problem.
Water management
Water was fertilized with a balanced nitrogen/phosphate fertilizer and molasses. The mechanical aerators circulated the water to provide oxygenation. They maintained dissolved oxygen at or above 4.0 milligram per liter, with 8 horsepower per pond during the day and 20 horsepower per pond during the night.
Pond water dissolved oxygen, salinity, pH, and temperature were recorded twice daily. Salinity ranged from 16 ppt at stocking to 25 ppt by harvest time, and pH fluctuated between 7.2 and 8.6. Morning temperatures ranged from 29.9 degrees-C in August to 25.9 degrees-C in December, whereas afternoon temperatures were 33.5 to 28.5 degrees-C.
Chemical parameters were measured at least once a week. Alkalinity was increased by adding agricultural lime to ponds. Ammonia-nitrogen levels ranged from below 0.01 milligram per liter to 3.5 milligram per liter (typically around 0.5-milligram per liter). Nitrite and nitrate were normally below 0.2 milligram per liter.
Reduction of effluents
Sediments from the production ponds were removed by opening the center drain into the sediment ponds during the trial cycle and also at harvest. The center drain was opened while the aerators were in operation. Sediments were allowed to settle in drainage canals so the water could be returned to the production ponds.
Feed management
The three feeds for PL acclimation and three feeds for grow-out included a carbon feed supplement during the entire cycle. A 31 percent-protein feed was used during the first half of the cycle, with a 25 percent-protein feed used during the second. Feeds were manually applied evenly around the pond perimeters five times per day. Food conversions were 2.5 to 3.0:1 due to unexpected mortalities.
Diseases
Mortality resulted from TSV infection, vibriosis, and finally Necrotizing Hepatopancreatitis (NHP). Vibriosis could be prevented with a different pond preparation and fertilization regime before stocking. NHP is treatable with oxytetracycline-medicated feed if detected early and treated immediately, but this is not approved by the U.S. Food and Drug Administration.
Initial investment
Total construction cost for the project was U.S. $254,543. Of the total, U.S. $4,100 was for feeding equipment, $65,416 for permanent equipment, and $185,027 for earthwork, ponds, liners, electrical work, water control structures, and miscellaneous equipment.
Production results
The first grow-out cycle lasted 115 days and averaged over 4.5 metric tons (MT) per hectare, with 30 percent survival and a growth rate of 0.89 grams per week. Harvest size was 13.29 grams (heads-on) on average, and FCR was 2.44. The yield was unprecedented in Nicaragua, and higher yields are possible, based on the experience gained during this first cycle and year-round production.
Economic results
Projecting results from the one cycle and project price received in December 2001 to annual production with two cycles, the demonstration resulted in per-hectare net revenue of U.S. $20,508 and costs of $30,157, or a loss of $9,639 (Table 1). However, it is important to note the December 2001 market prices for shrimp were at the lowest level in several years. A break-even situation would have resulted at a price level of U.S. $3.00 per pound.
Lopez, Costs and returns for the zero-exchange demonstration, Table 1
Actual Total (1 Cycle) | Projected Total (2 Cycles) | Annual Harvested (2 Cycles) | Annual Seeded (per hectare) |
---|
Actual Total (1 Cycle) | Projected Total (2 Cycles) | Annual Harvested (2 Cycles) | Annual Seeded (per hectare) | |
---|---|---|---|---|
Pounds harvested | 20,008 | 40,016 | ||
Price (U.S. $/lb) | 2.05 | 2.05 | ||
Total revenue (U.S. $) | 41,016 | 82,033 | 2.05 | 20,508 |
Operating expenses | ||||
Postlarvae (U.S. $) | 11,995 | 23,991 | 0.60 | 5,998 |
Feed (U.S. $, includes shipping) | 17,176 | 30,952 | 0.77 | 7,738 |
Chemicals/fertilizers (U.S. $) | 1,251 | 2,503 | 0.06 | 626 |
Fuel (U.S. $) | 6,866 | 13,733 | 0.34 | 3,433 |
Direct labor (U.S. $) | 5,600 | 11,200 | 0.28 | 2,800 |
Indirect costs (U.S. $) | 37,801 | 38,211 | 0.95 | 9,553 |
Conclusion
Although relatively expensive to set up, the Nicaragua Small Shrimp Producer Assistance Program prototype system proved to be biosecure against WSSV and offered the potential for low-cost shrimp production. Despite unexpected mortalities caused by TSV, vibriosis and NHP, shrimp growth was better than expected. The system could produce high yields in areas where shrimp diseases are endemic.
Another advantage is the need for a smaller land area to produce at the same levels of traditional semi-intensive farms. By recycling water in lined ponds, restocking can take place as soon as five days after a pond is harvested. Effluents are also reduced.
(Editor’s Note: This article was originally published in the October 2002 print edition of the Global Aquaculture Advocate.)
Now that you've reached the end of the article ...
… please consider supporting GSA’s mission to advance responsible seafood practices through education, advocacy and third-party assurances. The Advocate aims to document the evolution of responsible seafood practices and share the expansive knowledge of our vast network of contributors.
By becoming a Global Seafood Alliance member, you’re ensuring that all of the pre-competitive work we do through member benefits, resources and events can continue. Individual membership costs just $50 a year.
Not a GSA member? Join us.
Authors
-
Mayra López
Graduate Student
Food and Resource Economics Department
IFAS – University of Florida, Florida, USA -
Russ Allen
President
Aquatic Designs, Inc.
Okemos, Michigan, USA -
Charles Adams, Ph.D.
Professor
Food and Resource Economics Department
IFAS – University of Florida, Florida, USA -
Jim C. Cato, Ph.D.
Director
Florida Sea Grant College Program
University of Florida
Florida, USA
Related Posts
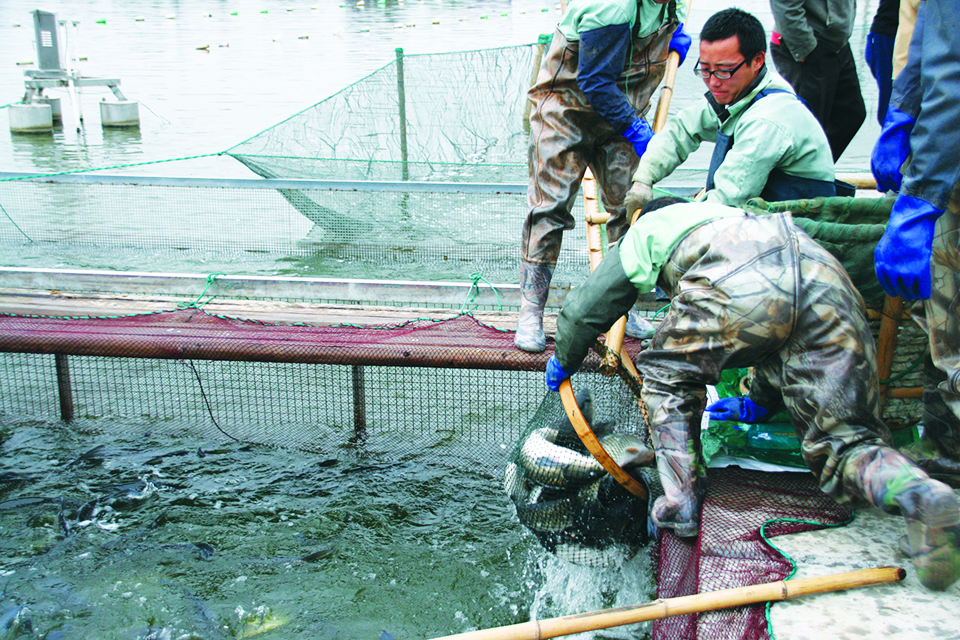
Responsibility
New intensive pond aquaculture technology demonstrated in China
An in-pond raceway system for intensive pond aquaculture was successfully demonstrated in China by the international marketing program of the U.S. Soybean Export Council.
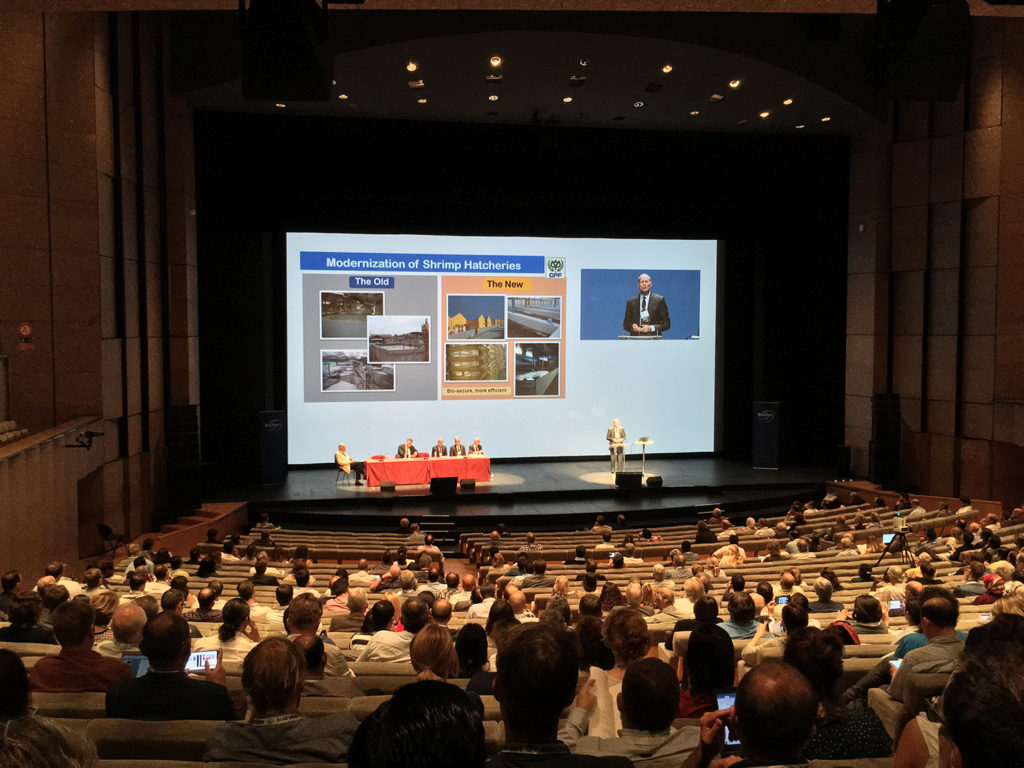
Intelligence
The message from Montpellier: Get innovative, efficient
AQUA 2018 brought together more than 3,000 aquaculture stakeholders from around the world, including keynote speakers Árni M. Mathiesen, Robins McIntosh and Øyvind Oaland.
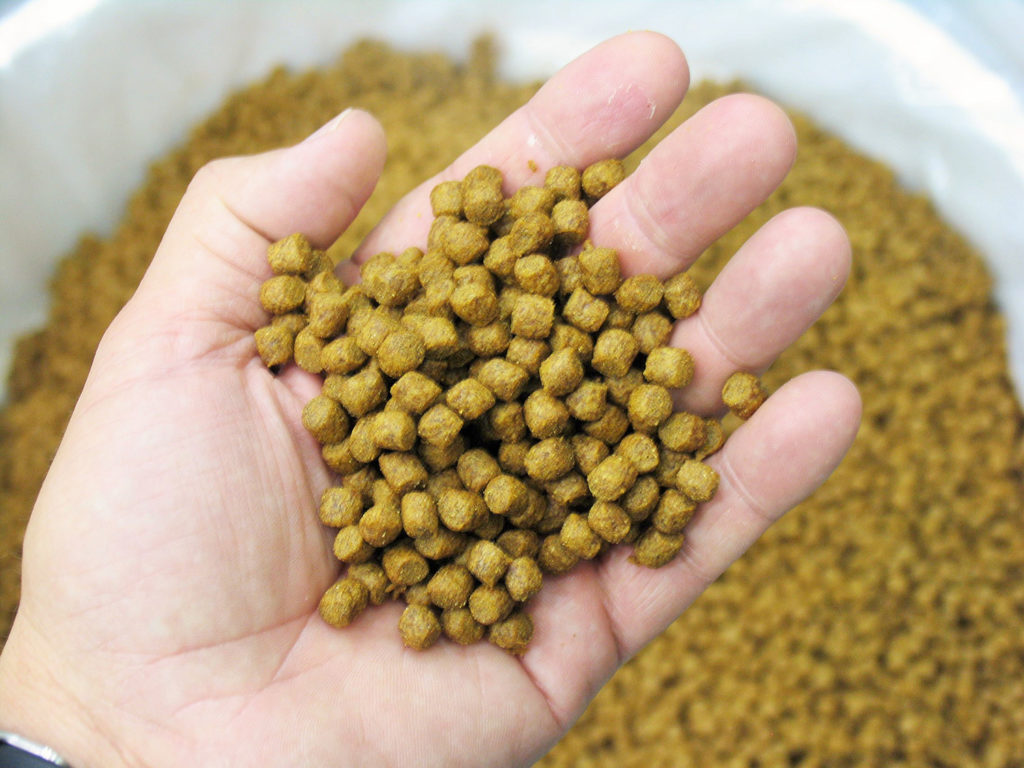
Aquafeeds
Analyzing aquaculture through Alltech’s Global Feed Survey
Alltech’s eighth annual Global Feed Survey, a compilation of estimated feed production data, reported that aquafeeds grew globally by 4 percent.
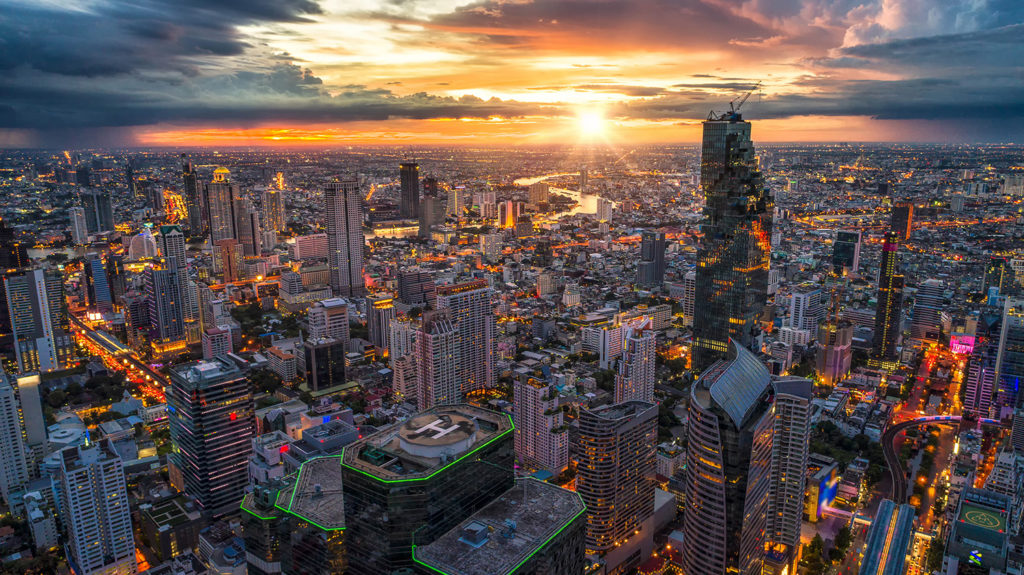
Responsibility
SeaWeb Seafood Summit in Thailand highlights rise of worker voice
Patima Tungpuchayakul, who rescued more than 5,000 Thai and migrant workers on fishing vessels, punctuates an emotional event kickoff.