Advanced materials and automated maintenance are both being put into play

Aquafeeds are typically cited as the biggest operating expense in aquaculture. So the netting to keep fish in and predators and pests out may end up being overlooked.
The industry is now paying more attention to net technology, said Vayu Garware, chairman and managing director of Garware Technical Fibres Ltd. (GTFL) of Pune, Maharashtra, India.
“Nets are a small part of the overall cost but can significantly impact the bottom line,” he told The Advocate.
What’s more, innovations in net materials and technologies promise even bigger boost to the bottom line. Examples come from GTFL itself, which has become one of the leading suppliers of netting materials to the Norwegian farmed salmon sector.
The company gets a substantial portion of its revenues from aquaculture, with its products found all over the world. According to Garware, GTFL’s latest nets are made of high-density polyethylene (HDPE), instead of the more traditional nylon.
While acknowledging nylon is the stronger of the two materials in dry-state tests, “It’s not only about strength. It’s about the actual application in wet conditions,” Garware pointed out.
Nylon is hydrophilic, or water loving. So, when immersed, nylon readily absorbs water and undergoes accelerated breakdown. Thus, nylon gets weaker in water over time and nets made of it generally last only five years, Garware said.
HDPE, in contrast, is hydrophobic, or water averse. Therefore, it doesn’t break down in water and suffers a minimal loss of strength over a similar time frame.
The result of using the new hydrophobic material is nets last longer. Garware noted that when cleaned in place there may be a doubling or more in net lifetime. HDPE also has better abrasion resistance of the two materials, an important advantage for fencing intended to keep predators out.
There are some drawbacks to HDPE. For instance, some formulations result in material that is less dense than water, which means it floats. GTFL builds its nets on a marine steel core and adds a pattern of lead weights, which together overcome floatation issues and add strength.

The company’s latest innovation incorporates tiny metallic copper particles within the net material. The process took four years to develop, according to Garware. Adding copper further increases the material density and brings another benefit: less biofouling. The metallic particles lead to a continuous release of a small amount of copper ions into the water.
“This delays fouling growth and therefore also delays any requirement to clean. We are able to see at least a 50 percent reduction in cleaning cycles,” Garware said.
Traditionally, biofouling has been reduced through the application of copper oxide paints. Such paints, though, tend to flake off and end up on as sediment on the seafloor, becoming an environmental hazard. The copper ions released by GTFL’s new products do not produce such a sediment, and the small amount of copper released suppresses biofouling without harming the environment, according to Garware.
Another netting-related innovation also addresses the biofouling problem, with Aqua Robotics of Harstad, Norway, automating the application of elbow grease. The company’s robot sits above the water and travels around the cage structure, moving a submerged brushing system that scrubs the net inside and out from top to bottom.

The automated system does not work on nets that are already encrusted with marine life, said CEO Knut Molaug. “We start with a clean net and we prevent it from the biofouling. So, we maintain it clean.”
Besides copper oxide paint, today biofouling mitigation can involve cleaning a net with a high-pressure spray, which is labor-intensive, expensive and stresses the fish inside. A high-pressure wash also interrupts fish feeding, another drawback.
Aqua Robotics’ robot avoids such problems. The parts of the net near the surface, which see greater biofouling due to the presence of more oxygen and light, are cleaned more often.
Molaug said that one surprising finding was how often cleaning needed to be done. The company’s latest robots, which are in the field in eight locations, clean continuously.
Aqua Robotics owns the systems and delivers a cleaning service, with customers paying a fee. Discussing plans, Molaug said the company is ready to scale up operations.
In speaking of the future, GTFL’s Garware noted that the company has extensive ongoing research and development programs. Work is underway on improved sea lice barriers, algal bloom shields and other material innovations.
For instance, GTFL is working on ropes for moorings that hold netting in place. Results over a year and a half of testing indicate that material improvements can significantly reduce the number of times that restraining ropes must undergo retensioning. The benefit in terms of cost savings depends on the location of the cage structure, but the company believes the savings can be more than seven-fold what would be spent on a new rope.
Such a return shows that an investment in netting, related gear and net technology can pay off. This also is indicative of what GTFL strives for, Garware said. “If we can give payback to customers in months, then we are doing something the right way.”
Follow the Advocate on Twitter @GAA_Advocate
Now that you've reached the end of the article ...
… please consider supporting GSA’s mission to advance responsible seafood practices through education, advocacy and third-party assurances. The Advocate aims to document the evolution of responsible seafood practices and share the expansive knowledge of our vast network of contributors.
By becoming a Global Seafood Alliance member, you’re ensuring that all of the pre-competitive work we do through member benefits, resources and events can continue. Individual membership costs just $50 a year.
Not a GSA member? Join us.
Author
-
Hank Hogan
Hank Hogan is a freelance writer based in Reno, Nevada, who covers science and technology. His work has appeared in publications ranging from Boy’s Life to New Scientist.
Tagged With
Related Posts
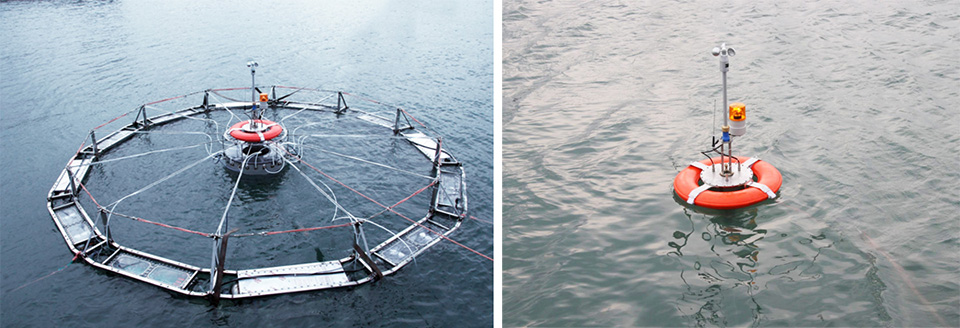
Innovation & Investment
Automatic submersible fish cage systems counter weather, surface problems
The development of submersible fish cage technologies may be necessary to avoid the operational challenges of surface-based aquaculture, which can include extreme temperature and weather conditions, jellyfish infestation, oil spills and many types of biofouling.
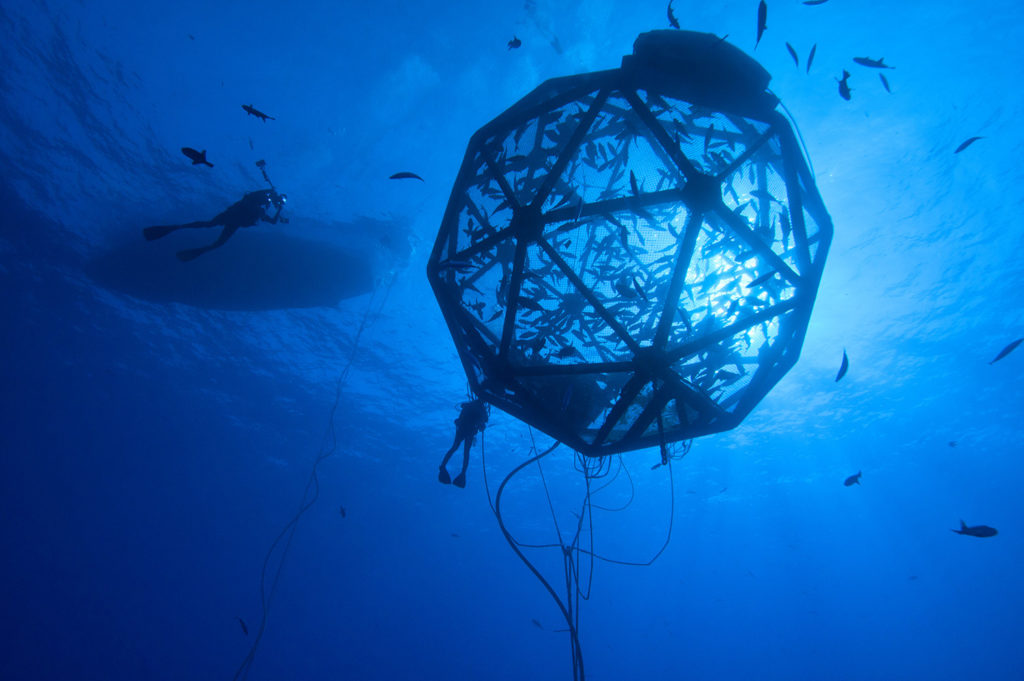
Innovation & Investment
Opinion: Stop offshoring offshore aquaculture
Something must change if the U.S. government hopes to encourage rather than discourage aquaculture, particularly in federal “offshore” waters. Neil Sims says it’s time to stop exporting knowledge, innovation and investment.
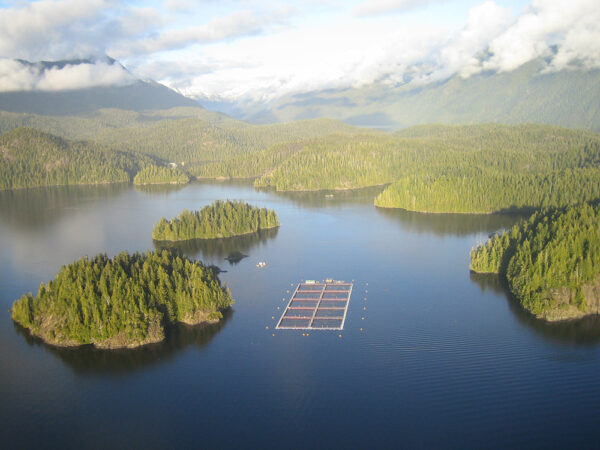
Intelligence
Canadian salmon farmers: ‘Leave us out of your shutdown’
The potential of a salmon-farming ban in Washington state is being monitored closely next door, in British Columbia, where many more salmon farms operate. But they’re not worried about a spillover effect.
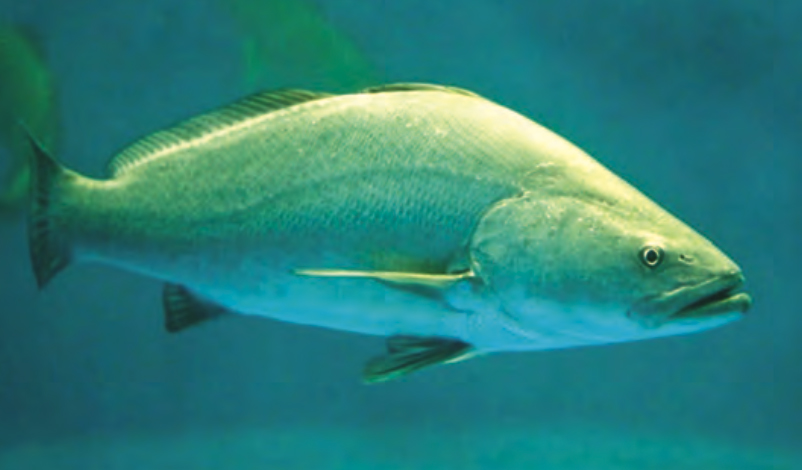
Responsibility
Aquaculture gives endangered totoaba a fighting chance
The tenuous fate of a pint-sized porpoise, the critically endangered vaquita, is linked to a fish targeted by poachers fueling China’s appetite for maws. The vaquita remains in peril, but aquaculture presents some hope for the totoaba.