Biological reactors remove nutrients and suspended solids

Fish farming can often generate pollutants that can be detrimental to animal health and the environment. Accordingly, researchers and farmers have developed and implemented numerous technologies and strategies to combat these issues, especially when considering recirculating aquaculture systems (RAS).
Technologies for cleaning culture water for reuse include biological processes, chemical processes and physical processes. Biological processes have traditionally focused on fixed-film processes, more commonly known as nitrification. Recently, suspended-growth biological processes are getting more attention in the RAS industry.
Suspended-growth bioreactors
In suspended-growth bioreactors, microorganisms are maintained in suspension by mixing the reactor using pneumatic aeration or mechanical agitation. Microorganisms in these bioreactors form floc particles between 50 and 200 µ in diameter that are conglomerates of microorganisms that are bridged together by polysaccharides and proteins.
Organic material and excess nutrients in the wastewater are removed as these flocs move through the water. The term floc is synonymous with bioflocs, microbial flocs and activated sludge.
Two major configurations of suspended-growth bioreactors are being considered by the aquaculture industry: sequencing batch reactors (SBRs) and membrane batch reactors (MBRs). Operation of SBRs consists of the following stages:
- Fill stage. “Dirty” wastewater is pumped or gravity fed into the SBR. Bioflocs are already in the bioreactor from the last batch cycle.
- Reaction stage. The “dirty” wastewater is mixed with bioflocs until treatment objectives such as greater than 90 percent reduction of nutrients are met.
- Settling stage. The mixing cycle is terminated, allowing bioflocs to settle out of the quiescent water column.
- Decantation stage. Treated “clean” wastewater is removed from the bioreactor while leaving the settled bioflocs behind.
The operation of a membrane batch reactor is similar, but instead of using settling and decantation stages, the well-mixed bioflocs and treated wastewater are separated from each other using a membrane or filter.
Every aquaculture facility has a limiting factor that requires wastewater to be discharged (Fig. 1). Typical limiting factors in RAS systems are either elevated suspended solids or accumulated nitrate levels. Biological reactors remove nutrients and suspended solids, thereby enhancing water reuse at RAS facilities.

Evaluation methods
To determine the feasibility of implementing suspended-growth biological reactors, researchers performed the following studies. Wastewater from an indoor recirculating aquaculture facility that cultures freshwater fish was diverted into bioreactors to determine removal rates of pollutants. Three 5-m3 pilot-scale SBRs and a single 42-m3 pilot-scale MBR were used in the evaluation process.
The sequencing batch reactors were operated in aerobic mode, and the MBR was run using both aerobic and anaerobic stages. Furthermore, carbon supplementation in the form of sucrose was used in the SBR experimental trials. No external carbon source was used for the MBR process.
All bioreactors were monitored for water quality. Treatment efficiencies were assessed by measuring water quality parameters before and after treatment.
Biofloc quantities can be estimated by measuring total suspended solids or, more appropriately, volatile suspended solids. Biofloc concentrations in the SBRs were operated to contain 1,000 to 3,000 mg/L. MBRs are typically operated at higher biofloc concentrations, often at levels that exceed 10,000 mg/L. Bioflocs from SBRs and the MBR were harvested, dried and analyzed for nutritional composition.
Results
Removal rates for important wastewater constituents are shown in Table 1. Both reactor types removed ammonia, nitrite and suspended solids with great efficacy. However, the MBR removed higher rates of nitrate compared to the SBR.
Kuhn, Typical removal rates of constituents, Table 1
Removal Rates Ammonia | Removal Rates Nitrite | Removal Rates Nitrate | Removal Rates Suspended Solids |
---|
Removal Rates Ammonia | Removal Rates Nitrite | Removal Rates Nitrate | Removal Rates Suspended Solids | |
---|---|---|---|---|
Sequencing batch reactor | > 90% | > 90% | 0-30% | > 95% |
Membrane batch reactor | > 90% | > 90% | > 90% | > 99% |
This was expected, because the MBR included an anaerobic stage, which is required for effective denitrification. If the SBRs included an anaerobic stage, denitrification could be feasible. Implementing anaerobic stages complicates the process, but should be considered if nitrate is the limiting factor at an aquaculture facility.
If bioreactors are properly operated and maintained, no offensive odor is produced. Bioflocs are typically removed from the bioreactor to control and stabilize the population of microorganisms. For example, removing 10 percent of the solids each day will maintain a biofloc that is, on average, 10 days old. The age of the bioflocs influences the types of organisms that form them.
Typically, “young” biofloc yields predominately heterotrophic organisms, while “old” biofloc could be dominated by fungi. Traditionally, removing bioflocs to control biofloc age is an issue for a bioreactor operator. However, if we could harvest bioflocs to be used as an alternative protein source, we could potentially reduce the amount of marine meal required in aquaculture diets.
Nutritional value
The nutritional compositions of SBR and MBR bioflocs are presented in Table 2. Even though SBR bioflocs had higher protein levels compared to MBR bioflocs, both bioflocs proved to be suitable and often superior ingredients when they replaced fishmeal and/or soy protein.
Kuhn, Typical dry-matter proximate composition, Table 2
Protein | Carbohydrates | Total Ash | Crude Fiber | Crude Fat |
---|
Protein | Carbohydrates | Total Ash | Crude Fiber | Crude Fat | |
---|---|---|---|---|---|
Sequencing batch reactor | 41-49% | 31-36% | 12-13% | 13-15% | 0-1% |
Membrane batch reactor | 35-43% | 22-28% | 22-28% | 14-18% | < 0.1% |
Lab-scale trials using various biofloc inclusion rates improved shrimp growth by an average of 4 to 67 percent over two independent six-week feeding trials. This not only provides an option for disposing of bioflocs as part of normal suspended-growth biological operations, but also provides a sustainable alternative to marine meals in shrimp diets.
Even though biofloc technology has great potential, small-scale studies should be conducted prior to implementing the technology in full-scale production. This is because each aquaculture facility has unique wastewater characteristics, including water quality and flow, that strongly influence bioreactor design, operations and management.
(Editor’s Note: This article was originally published in the January/February 2010 print edition of the Global Aquaculture Advocate.)
Authors
-
David D. Kuhn, Ph.D.
Department of Food Science and Technology
Virginia Tech/Virginia Sea Grant
Blacksburg, Virginia 24061 USA -
Gregory D. Boardman, Ph.D.
Department of Civil and Environmental Engineering
Virginia Tech/Virginia Sea Grant
Blacksburg, Virginia 24061 USA -
George J. Flick, Jr., Ph.D.
Department of Food Science and Technology
Virginia Tech/Virginia Sea Grant
Blacksburg, Virginia 24061 USA -
Addison L. Lawrence, Ph.D.
Texas A & M University – Corpus Christ
Corpus Christi, Texas, USA
Tagged With
Related Posts
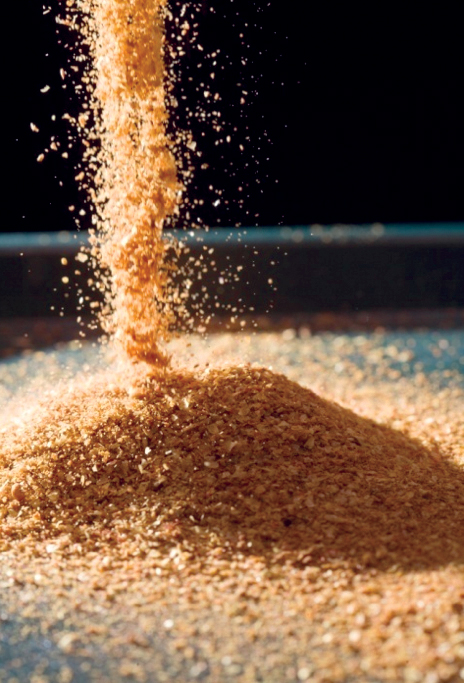
Aquafeeds
A look at corn distillers dried grains with solubles
Corn distillers dried grains with solubles are an economical source of energy, protein and digestible phosphorus to reduce feed costs and fishmeal usage.
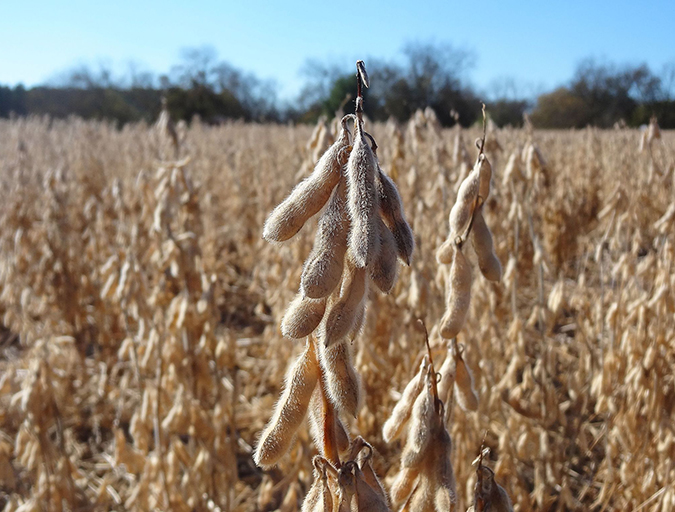
Aquafeeds
A look at phospholipids in aquafeeds
Phospholipids are the major constituents of cell membranes and are vital to the normal function of every cell and organ. The inclusion of phospholipids in aquafeeds ensures increased growth, better survival and stress resistance, and prevention of skeletal deformities of larval and juvenile stages of fish and shellfish species.
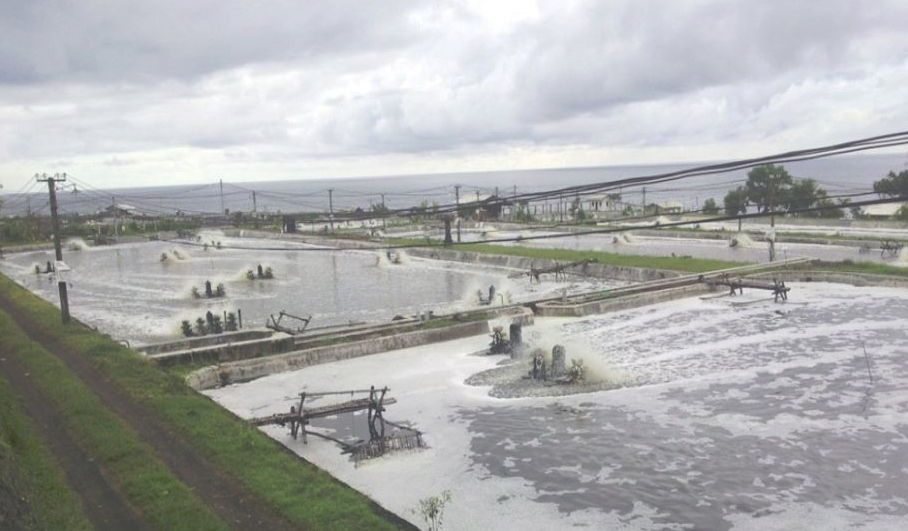
Responsibility
A look at various intensive shrimp farming systems in Asia
The impact of diseases led some Asian shrimp farming countries to develop biofloc and recirculation aquaculture system (RAS) production technologies. Treating incoming water for culture operations and wastewater treatment are biosecurity measures for disease prevention and control.
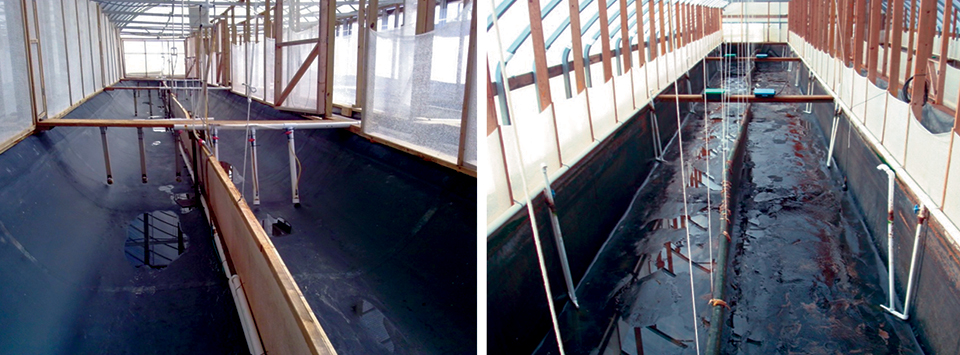
Responsibility
Advances in super-intensive, zero-exchange shrimp raceways
Research at the Texas AgriLife Research Mariculture Laboratory is investigating ways to improve the economic viability of super-intensive raceways for shrimp production.