Mixing and residence time are important factors for water stability

Preconditioning is commonly used in both the pelleting and extrusion manufacturing of aquafeeds. In the preconditioning process, low-pressure steam is added to heat and increases the moisture of the meal. In the pelleting process, the maximum moisture that can be attained without causing the pellet mill to plug up is 17 percent. In contrast, in the extrusion process, moisture levels can be as high as 20 percent and if force fed into the extruder, the moisture can be even higher.
The extrusion process is more flexible in the amount of water it can handle, making it easier to raise the meal moisture and degree of cook to the desired levels.
The preconditioning process
To understand the preconditioning process, it is important to understand the heat and mass transfer between its components, a mixture of steam and ingredient meal. The medium in the pre-conditioner is a three-phase system of gas (steam), liquid (water) and solids (meal mixture). Steam transfers energy to the particles via condensation. The particles of meal are colder and steam condenses on them, forming a thin film of water around the particles. Thus, meal particles are surrounded by hot saturated steam, causing an increase in the temperature (heat transfer) and moisture.
How fast the heat transfer and moisture uptake occur will depend on two factors. The first is the film resistance at the surface of the particle. The more solid-to-fluid contact, the lower the film resistance. In other words, the more the material is exposed to the steam, the more contact between particles will occur. This can be accomplished by proper mixing in the pre-conditioner.
The second factor is how fast heat and moisture travel to the interior of the particles (mash meal), and this is governed by Fourier’s and Fick’s second laws. The meal is composed of particles that have different internal resistance for heat and moisture. Therefore, by knowing the coefficients of diffusivity one can apply physical laws to estimate the right time (residence time) to heat and humidify the particles homogeneously. In general, the higher the heat and water diffusivity, the faster the heat and moisture will flow into the particles.
Starch relevance
Most aquafeeds have high amounts of wheat flour or wheat byproducts, and one of their major components is starch. At ambient temperature, starch has a thermal diffusivity coefficient of 10-7 m2/s. In contrast, water diffusivity is 10-5 m2/s or 100 times less than the thermal diffusivity. In simpler words, heat transfer is faster that moisture internalization.

In most preconditioning scenarios, it is possible to heat up the meal to the target temperature but it will take longer to also increase the mash moisture. The latter is one of the reasons why it is important to have an adequate residence time in the pre-conditioner, to allow moisture to sufficiently penetrate the particles. Moisture and temperature are key elements to produce aquafeeds with high water stability.
Another important aspect in aquatic feeds is the hydration of other particles, in particular, the protein fraction of wheat, gluten. It is composed of two protein fractions and requires hydration and mixing to form the gluten matrix. Wheat gluten is considered a natural binder, and in most cases the best binder when proper hydration and mixing are provided during the aquafeed manufacturing process. In most single-pass conditioners, it is basically impossible to provide adequate mixing to expose particles to steam or to stimulate the gluten matrix formation.
Film resistance
Film resistance around the particle can be measured using the dimensionless Biot number (Bi). When the resistance is in the film around the particle, as is the case with pre-conditioners with poor mixing, the Biot number is very small (<0.1). In conditioners with good mixing action, the main resistance is the diffusion of water to the particle and the Biot number is large (>10). Based on this number, we can classify most pre-conditioners available for pelleting into an intermediate category in mixing efficiency where the Biot number is approximately 1. The film and internal resistance have a direct impact on the rate of hydration into the particle.
Particle size and hydration
Ingredient particle size has a major impact on the rate of hydration in the pre-conditioner. Larger particles (>400 microns) require twice as much hydration time than smaller particles (<200 microns). The following formula, based on their radius, is used to calculate the time required to hydrate the ingredient particles:
Fo = Dt / (R/3)2 where Fo is Fourier number, D is the water diffusivity, t the diffusion time, and R the radius of the particle.
Solving for t shows that, as the particle radius increases, a longer time is required to hydrate it. Thus, particle size not only needs to be small enough to improve feed digestibility, but also to improve the hydration rate that can lead to higher water stability of the final aquafeed product. If particles are of more uniform dimensions, the hydration rate will be similar in most particles. This is another good reason for considering post-grinding to achieve more uniform particle size, and hence better hydration rates in the mixer and pre-conditioner.
Residence time distribution
Residence Time Distribution (RTD) should not be confused with Residence Time (RT). The latter can be determined using a color marker, through the time it takes the marker to show at the exit of the pre-conditioner. The RTD is the average residence time the material stays in the pre-conditioner, and has a characteristic bell-shaped curve. The shorter the distribution, the more uniform and more efficient the pre-conditioner is in hydrating and heating particles more uniformly.

There are many kinds of pre-conditioners with different configurations for paddle design, shaft speed, paddle angle and volumetric capacity. Understanding RTD can help understand how hydration time can be improved in the pre-conditioner. There are two types of mixing in the pre-conditioner. One is axial mixing, which contributes to increase the particle to steam/fluid contact in the preconditioning chamber. The second is the radial mixing, which also affects the contact of particles with the steam and liquid, but depends more on shaft rpm and paddle configuration/geometry. Depending on their design, pre-conditioners can exhibit a plug flow (very little mixing) and mixed flow (highly axial mixing). These flows depend on the paddle geometry, shaft speed, and degree of fill.
Fill ratio
Fill ratio represents the volume occupied by the meal in relation to the total volume of the pre-conditioner. The meal volume is measured when the pre-conditioner is stopped. Most pre-conditioners used in the pelleting industry today have very low fill ratio (~ 30 percent). Having a small fill ratio means that the pre-conditioner has more empty spaces. Because steam is a gas, it will tend to fill the voids in the pre-conditioner. When this happens, it can be expected that less steam will be in contact with the mix to heat it and hydrate it. Therefore, increasing the fill ratio improves not only the residence time but also the temperature and hydration uniformity of the mix.
The degree of fill can be improved by properly adjusting the paddle configuration (angle). Twist paddles can increase axial mixing. In contrast, paddles placed at 180 degrees can increase the filling ratio. Most commercial pre-conditioners are fitted with paddles that can be adjusted by the operator. In most cases a good paddle configuration will include paddles in the reverse, some forward and some flat. Some pre-conditioners also incorporate retention plates that have the purpose of providing an obstacle at the end of the unit and thus increase the residence time.

Irregular coloration
A common problem during the pelleting process of shrimp feeds is the appearance of irregularly colored pellets. In most cases, this is caused by inadequate moisture distribution in the pre-conditioner. This can be more easily explained by understanding the RTD. In this particular case, the RTD is broad, meaning that some particles spend a short time in the pre-conditioner, thus receiving insufficient moisture. This problem is not only associated with inadequate paddle configuration, shaft speed or degree of fill, but also with uneven particle size. Even if the pre-conditioner is properly optimized, a broad particle distribution size can result in uneven moisture distribution among particles. The large ones will have less moisture, while the small ones will have higher moisture content. Therefore, particle size needs to be as uniform as possible and the RTD needs to be as narrow as possible.
Perspectives
Preconditioning is a key step during the aquafeed manufacturing process, because it increases the temperature and moisture content ingredients (feed meal particles). This is vital to achieve finished aquafeeds with the desired water stability. The efficiency of a pre-conditioner depends on consistent particle size and adequate mixing, residence time, and fill ratio, and different equipment manufactures offer different designs.
Now that you've reached the end of the article ...
… please consider supporting GSA’s mission to advance responsible seafood practices through education, advocacy and third-party assurances. The Advocate aims to document the evolution of responsible seafood practices and share the expansive knowledge of our vast network of contributors.
By becoming a Global Seafood Alliance member, you’re ensuring that all of the pre-competitive work we do through member benefits, resources and events can continue. Individual membership costs just $50 a year.
Not a GSA member? Join us.
Author
Tagged With
Related Posts

Aquafeeds
Analyzing the hydrostability of shrimp feeds
The physical integrity and nutrient leaching of shrimp aquafeeds are important aspects in their quality control. The water stability of shrimp aquafeeds is often evaluated in various subjective manners. This analytical procedure provides a baseline for the aquafeed manufacturer to assess product quality.
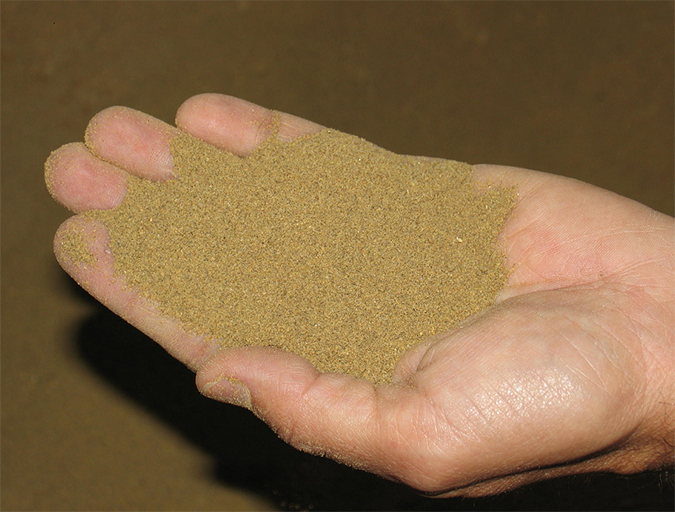
Aquafeeds
Mixing Cost Center is at the heart of feed manufacturing
Ingredients that are properly proportioned and mixed for an adequate mixing time are very important to assure the manufacturing of aquafeeds that meet the standards for the shrimp species and life stage for which the formula was designed.
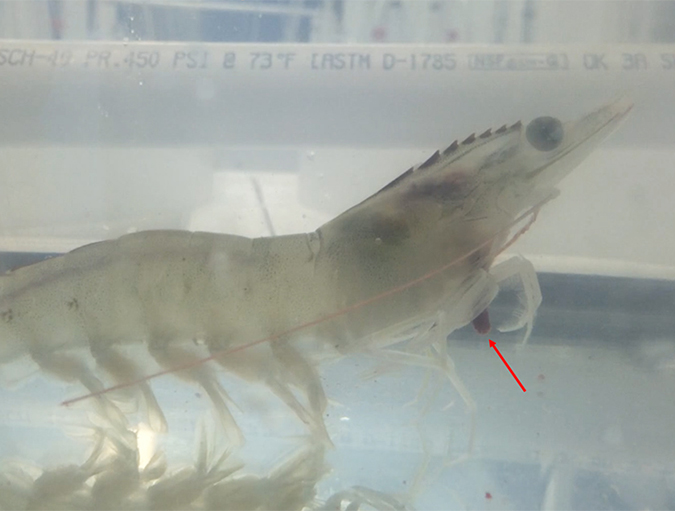
Aquafeeds
Twin screw technology for better extruded feeds
Extrusion processing can be a better alternative to produce high quality-low- polluting shrimp feeds. Extruded pellets with high water stability can be produced by controlling the Specific Mechanical Energy (SME) and without the inclusion of artificial binders. New extruders are equipped with state-of-the art SME controls that permit the adjustment of the SME to the desired range, to produce soft very hydrostable pellets.
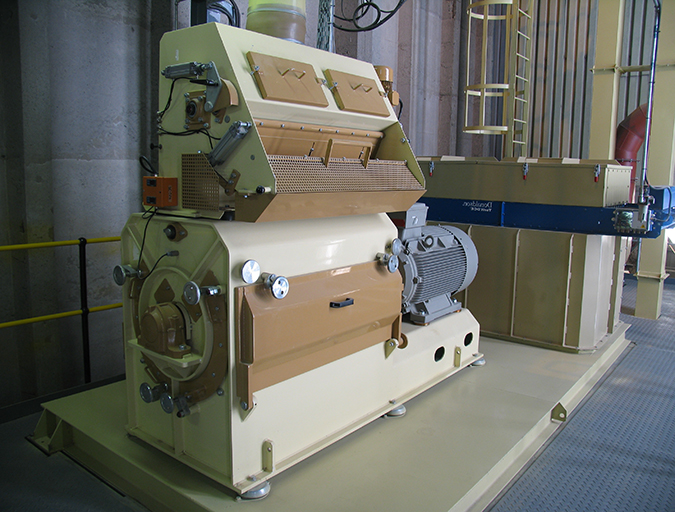
Aquafeeds
Optimizing crucial cost centers for shrimp feed manufacturing
Assuring that aquafeed ingredients are processed properly into a high-quality product requires monitoring each manufacturing process through the proper in-line quality assurance, to produce a consistent quality continuously.