By turning shipping containers into AI-enabled, biofloc-based shrimp farms, Atarraya aims to bring shrimp farming closer to market
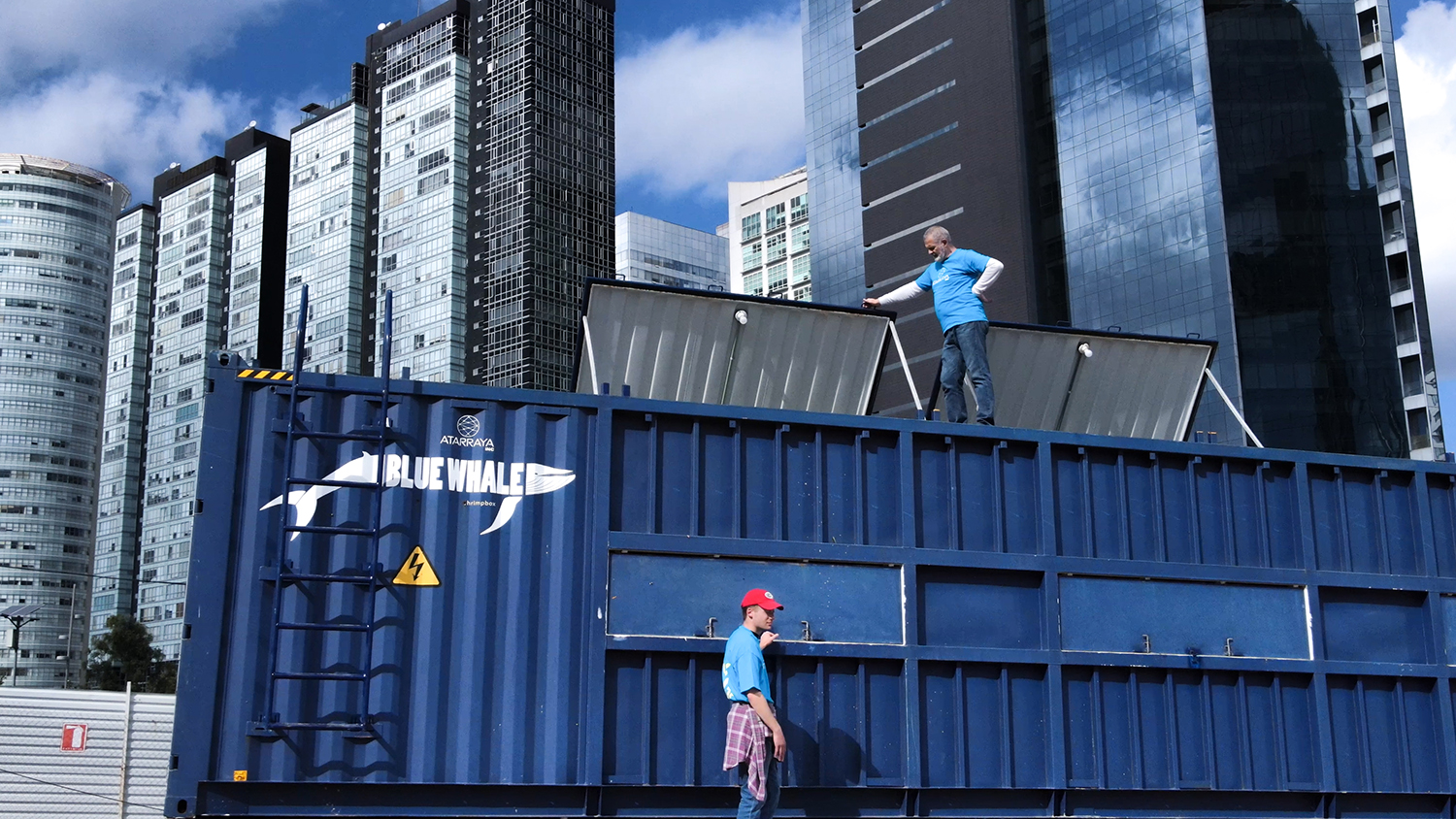
In 2019, Mexico City entrepreneur Daniel Russek was brainstorming on how to grow shrimp sustainably closer to top markets. The solution he came up with, the Shrimpbox, has just been named one of the best inventions of the year by TIME Magazine, and it may well be a game-changer for shrimp aquaculture.
Shrimpbox is a 40-foot-long cargo container containing a shrimp farm in an AI-powered, automated system where everything can be operated remotely. Shrimp can be fed and water quality can be monitored at the touch of a button, and each container can produce up to 1.5 metric tons of shrimp annually. Located on land, the Shrimpbox uses a zero-discharge biofloc system, which means it has no adverse environmental impacts. Russek says an ROI comparable to the Shrimpbox would require two farm acres using traditional shrimp farming techniques.
To date, his company Atarraya – with headquarters in Indianapolis and Puerto Escondido, Mexico – has eight operational Shrimpbox units with 12 more on the schedule by January 2023. There are orders for 250 units and plans to manufacture those next year in Mexico. “We’re talking with five different farmers in the U.S., and they’ll start with between 20 and 70 boxes each,” he said.
Atarraya had its first Shrimpbox running in Indianapolis in July 2022 and just four months later the company harvested its first shrimp on the site. “This is a plug-and-play system and all you need is to connect the Shrimpbox to energy and water to get it operational. We believe investors will start making money after just six months,” he said.
Belief in biofloc
Russek’s introduction to aquaculture began back in 2005, when he was an economics student in Mexico City, serving as president of the students’ council. That year, a hurricane hit Oaxaca and he spearheaded an effort to raise funds and donations for the emergency response. He traveled to the region to deliver goods, and while there, he was introduced to some of the local Indigenous communities. They had relied on subsistence fish farming for generations but were now struggling because their waters had experienced overfishing. He returned home incentivized to find a way to work with these communities, and specifically, to create economic opportunities for its members so they wouldn’t be tempted to leave.
Russek, just 22 years old at the time, thought the answer was aquaculture and hired consultants to create a business plan for shrimp farming in Oaxaca. But his board of advisors cautioned that investment for shrimp farms would be impossible due to the diseases plaguing top-producing regions. Mexico’s former minister for environmental protection of natural resources, Julia Carabias, was among the individuals Russek met with. She suggested innovating outside of conventional shrimp farming practices.
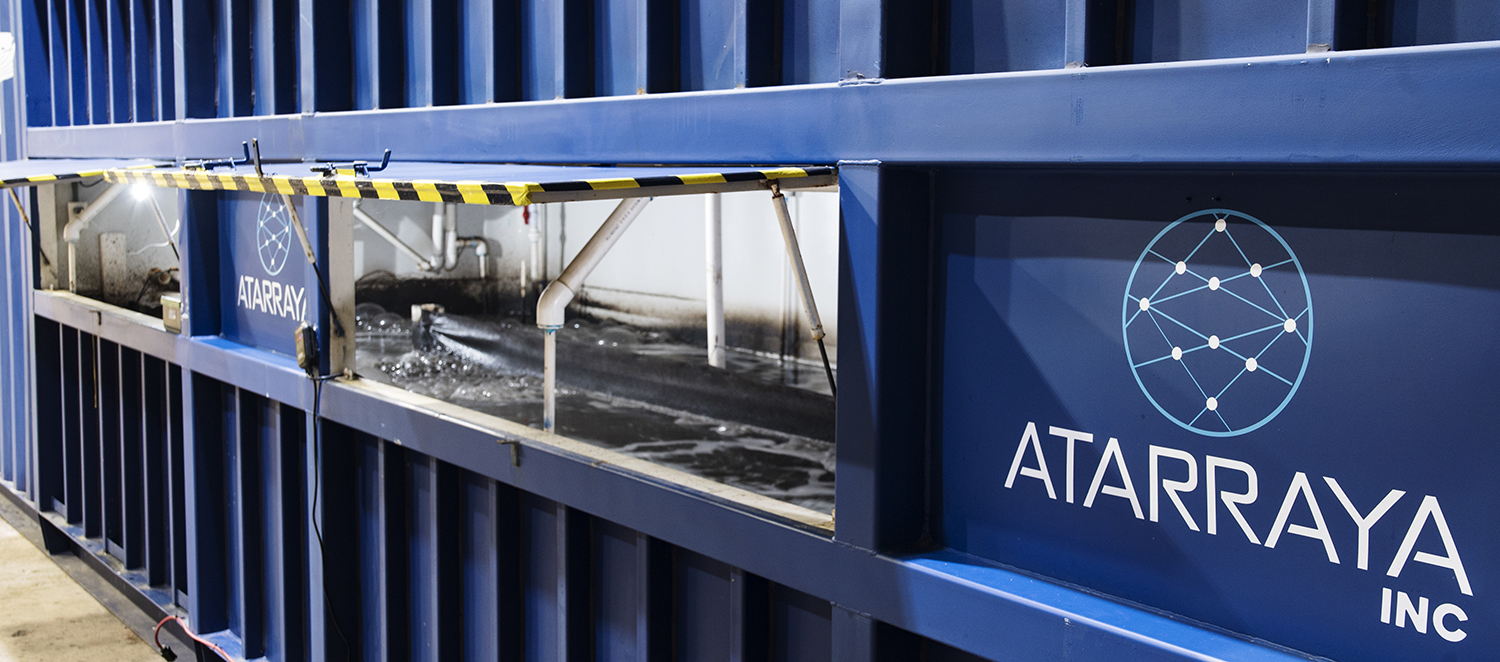
Russek and his team began working with scientists from Israel and Brazil and by 2011 they determined that a biofloc system, in which microorganisms recycle cultured animal waste into a food source, would be the best option. That year, he built a pilot shrimp farm in Puerto Escondido, with 39 lined biofloc ponds and a nursery, larviculture and algae-growing zones. Russek says it’s the world’s first commercial shrimp farm running on biofloc, and he staffed it with workers from the African-Mexican Indigenous community he’d met six years prior.
In 2015, he began exporting shrimp from the farm to restaurants in Orlando, New York, Washington, San Francisco, Los Angeles and Las Vegas under the Agua Blanca brand. He quickly discovered that the transportation logistics made the export financially unfeasible, while also quashing any environmental claims for Atarraya.
We believe investors will start making money after just six months.
That’s when the idea for Shrimpbox gained traction. He built the first Shrimpbox prototype in 2020, using the zero-discharge biofloc system he’d mastered on the farm. It uses less than 0.2 percent water per ton of shrimp than a traditional system, he explained.
“We lose water through evaporation, composting and biodigesters, so we do need to bring in some new water to compensate for that loss,” he said. “But all the toxins and nitrates generated by the shrimp are turned into nutrients. Sludge is removed for composting and biodigesters turn it into biogas and fertilizer.”
Each box has a control room with an automated feeding system, pumps, waste collection and equipment to maintain oxygen levels, all linked to the cloud so that customers can be remotely alerted when issues arise. The growing space consists of two 33-foot tanks with a low air-to-water ratio that optimizes heat retention. The boxes in Indianapolis are located in a warehouse kept at 68 degrees-F. The boxes themselves are kept at 82 degrees-F. Russek said that customers in cold locations would need a warehouse to house the Shrimpboxes, but that testing is underway on insulated Shrimpbox units that could stand outside in colder climates.
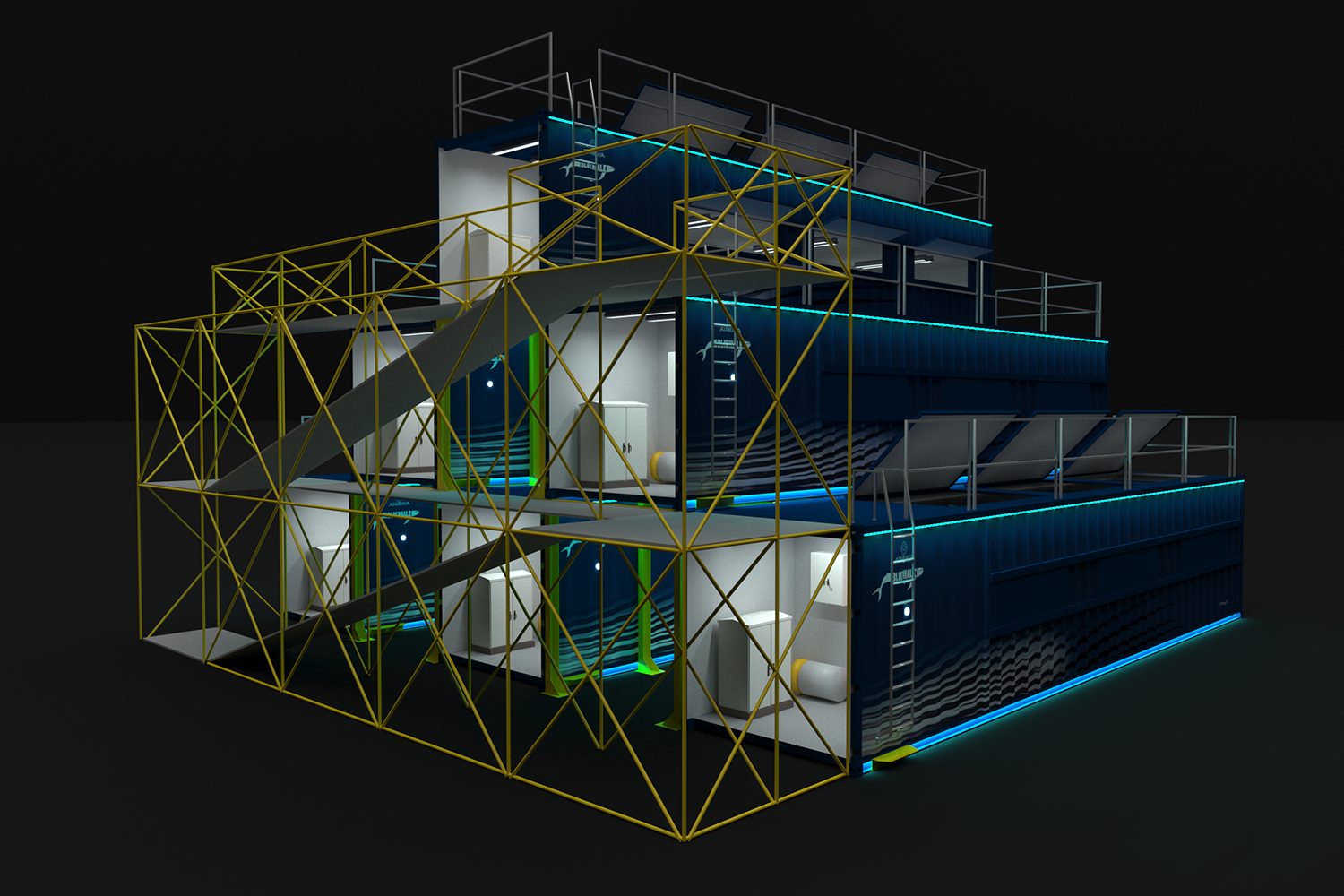
‘We know our tech is complex’
With a team of 100 staff working on research, development and manufacturing, Russek says prospective farmers can be trained to use the Shrimpbox within four weeks. His aim is to manufacture each Shrimpbox for (U.S.) $25,000.
“Our business model is based on selling the equipment with a small markup, selling the shrimp larvae and shrimp feed at market price, and charging a tech royalty around 8 percent for every kilogram of shrimp sold,” he said. “This means our profits will come from real income generated by our farmers. In the current farming structure, the farmer is the last one to make money. With our business model, we want to subsidize the hardware to share the risk with the farmer.”
Ten years from now, he hopes that Atarraya will occupy 5 percent of the U.S. market and that the company will be working closely with farmers around the world. The short-term challenge will be how to manufacture large quantities of Shrimpboxes. The company is launching its bid for series B funding and looking to raise $15 to $20 million in the next few months that it intends using it to lower manufacturing costs.
Reflecting on his achievements since that 2005 visit to Oaxaca, Russek says he has a lot to be proud of.
“My goal was to have a sustainable shrimp farm in Oaxaca that would give better opportunities to those communities, and we now have a farm that is run by Zapotecs from a community called Guapinole,” he said. “They are operating one of the most complex and efficient shrimp farms in the world, and they’re the experts! They are the people going to Indianapolis and teaching others how to grow shrimp, and they can explain the metabolism of nitrogen and equipment inside the Shrimpboxes. For that I’m very proud.”
As for the vote of confidence from TIME, Russek is quick to admit that the Shrimpbox is not about him at all. “We’re almost 100 people right now and we’ve been working on the same challenge for the past 10 years. This idea is the one that got traction but there were at least five failed projects that didn’t work. It wasn’t easy to get to this point,” he said. “And that’s why we have an unconditional open-door policy. We know our tech is complex and we encourage people to visit our Indianapolis facility and ask as many questions as they want. Our advantage is more on the experience and the software.”
Follow the Advocate on Twitter @GSA_Advocate
Now that you've reached the end of the article ...
… please consider supporting GSA’s mission to advance responsible seafood practices through education, advocacy and third-party assurances. The Advocate aims to document the evolution of responsible seafood practices and share the expansive knowledge of our vast network of contributors.
By becoming a Global Seafood Alliance member, you’re ensuring that all of the pre-competitive work we do through member benefits, resources and events can continue. Individual membership costs just $50 a year.
Not a GSA member? Join us.
Author
-
Lauren Kramer
Vancouver-based correspondent Lauren Kramer has written about the seafood industry for the past 15 years.
Tagged With
Related Posts
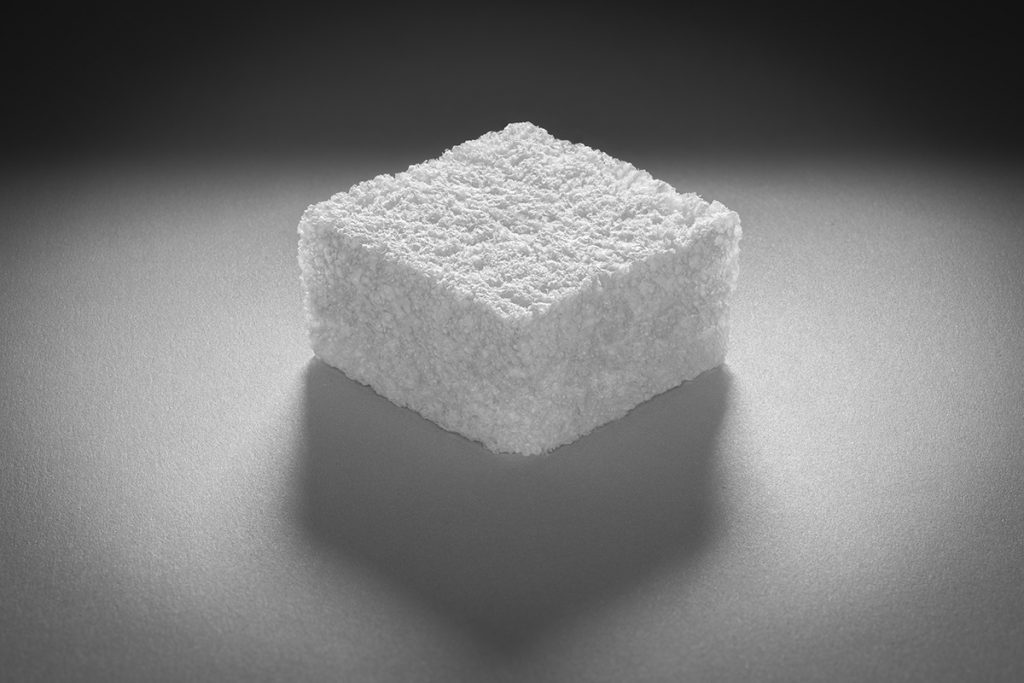
Fisheries
‘Regulation is pushing toward greenifying materials’: How one innovator is upcycling seafood waste into biodegradable packaging foam
GOAL 22: Cruz Foam’s biodegradable packaging foam made with shrimp shells is a finalist for GSA’s inaugural Global Fisheries Innovation Award.
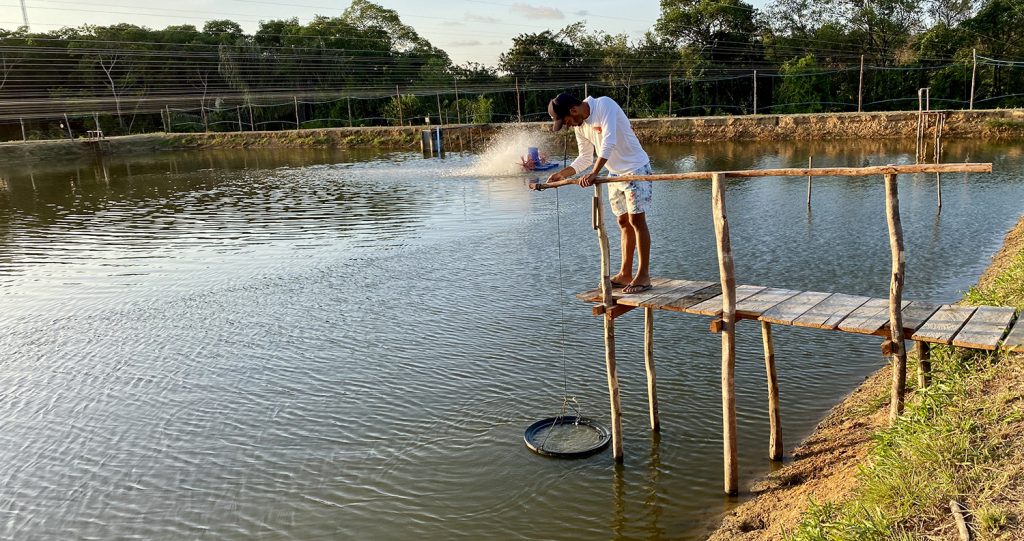
Aquafeeds
This Las Vegas-based company is converting ammonia into a regenerative fishmeal alternative for shrimp
A regenerative fishmeal alternative for shrimp feeds from Ocean Ranch is created by the natural conversion of ammonia to protein.
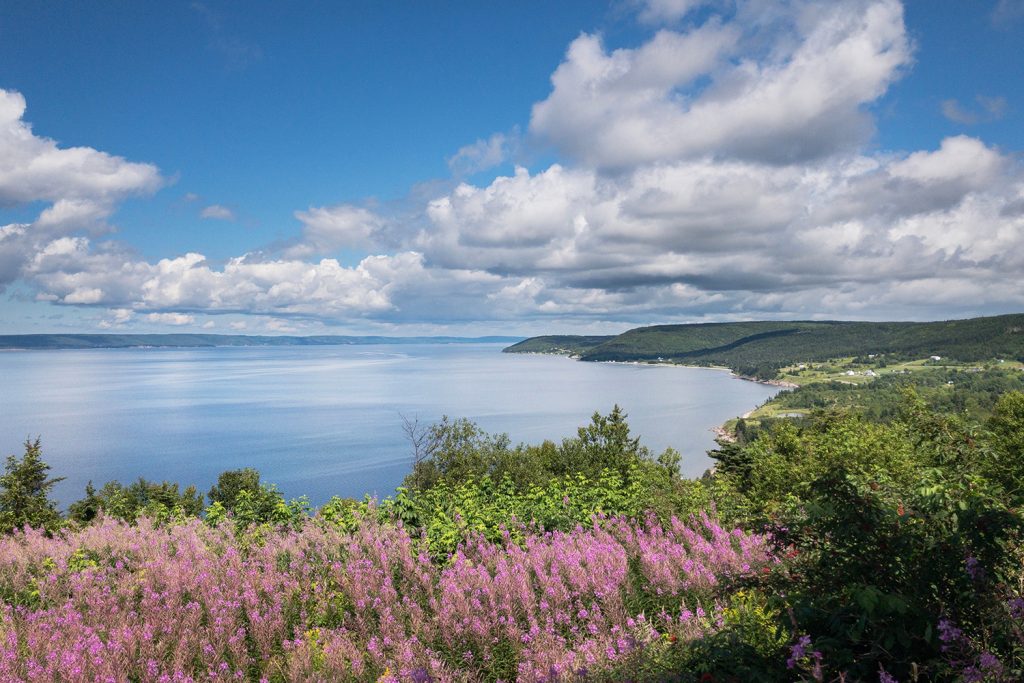
Intelligence
Could floating cages revitalize an oyster farming industry decimated by the MSX parasite?
Study says floating cages could help revitalize the Cape Breton oyster farming industry destroyed by MSX parasite 20 years earlier.
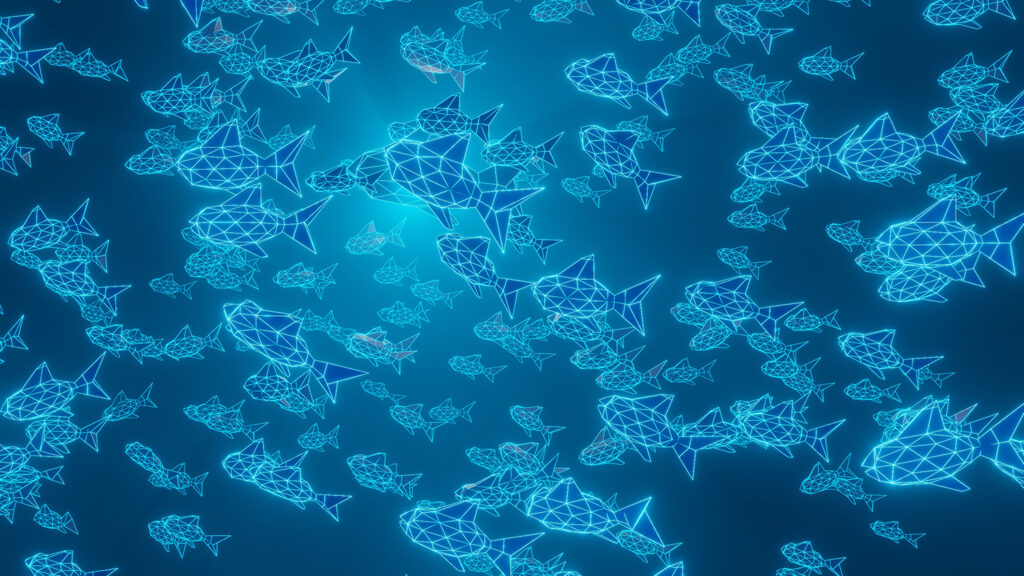
Innovation & Investment
‘AI ticks all the boxes’ and is proving to be a perfect match for aquaculture
Artificial intelligence (AI) is rippling through the aquaculture industry, promising greater efficiencies and insights, as well as investor interest.