Offers advantages in shrimp production
With current low farm gate prices for shrimp, many farmers are looking for ways to improve the economics of shrimp production. For growers committed to using mechanical aeration and intensive culture densities for production over 8 tons per hectare per cycle, electrical power consumption is a major cost. Reducing power consumption can improve profitability significantly.
Pressure differential piping
Numerous wastewater treatment plants use a form of aeration that has been around for 25 years called bottom diffusion piping. Unfortunately, the name does not accurately convey its function, and aquaculturists refer to it as pressure differential piping (PDP).
As generally practiced in the aquaculture industry, diffusion piping systems use a ceramic or rigid porous material that allows air to escape into the water at depth with only the pressure differential associated with the size of the pores affecting the pressure delivery requirement.
With PDP piping, a self-weighted polyethylene pipe is cut with numerous slots along its length. These slots are normally closed, and as the blower builds pressure above the ambient surrounding pressure, the polyethylene distends within its elastic limit and gradually releases air as the surface tension of the polyethylene/water interface is exceeded.
The length of the slots, number of slots per meter, and stiffness of the polymer durometer control the air release rate. The bubbles produced are quite small at 200-500 μ, allowing their own surface tension to prevent coalescence and production of bubbles that rise at a rate above the laminar flow limit.
Advantages
The slower-rising bubbles produce longer transit times and greater oxygen transfer efficiency. This translates into much higher oxygen transfer per unit horsepower and shrimp production capacities of more than 700 kilograms per horsepower. Comparing this with the generally accepted figure of 400-450 kilograms per horsepower for paddlewheels shows why PDP is attractive from an energy-consumption standpoint.
Maintenance and durability
Other advantages are not so obvious. Many farmers have dragged paddlewheels in for repair in the middle of the night. With the shore-based blowers used in PDP systems, maintenance is convenient and replacement is measured in decades, not months. The average life expectancy of an intermediate blower in a wastewater treatment plant is in excess of 12 years. How many paddlewheels would a farm replace over these same 12 years?

Improved feeding success
Another prime advantage is the improvement in feeding with the low flow velocities produced by PDP piping. In a high-yield system such as Belize Aquaculture, with production of 15 to 20 tons per hectare, the use of 40 to 45 horsepower per hectare of paddlewheels is required to generate the needed aeration. In this situation, a single device – the paddlewheel – is asked to provide circulation as well as aeration.
Paddlewheels are successful at generating a lot of production, but at relatively high energy costs and feed-conversion ratios of 1.5 to 2.0. Research previously published by this author showed a very significant relationship between flow velocity and feeding success.
Conventional paddlewheels used at rates above 15 horsepower per hectare reduce feeding success rapidly. PDP piping uses the laminar flow of the rising bubbles to displace water vertically, thereby reducing benthic velocities and improving feeding success. This vertical mixing effect, called a gyre, eliminates concentration differentials from top to bottom in the water column.
Reduced bank erosion
One of the more important aspects of using a vertical gyre is the lack of bank erosion. Many PDP pipe systems are deployed in unlined ponds, and a comparison between the bank erosion in a paddlewheel pond and a PDP pond is striking. There is literally no sediment movement from the banks with PDP, so cleanup is simplified after harvest.
This also has implications regarding waste disbursement in ponds. Paddlewheels are generally deployed to produce create a central, anaerobic pile of sludge and sediment that should be removed after every crop. This sludge pile can occupy 10 to 25 percent of the pond bottom. It is typically only 15 to 25 percent organic, with the rest sediment from the benthos and pond banks.
PDP piping oxidizes waste over the entire bottom of the pond and makes more of the pond bottom available to the shrimp as habitat. This reduces the average density of shrimp per unit area and improves feeding success by reducing flow velocity at the same time. Commercial farms in China that use PDP have achieved 15 to 20 tons per hectare with 15 horsepower per hectare, and simultaneously realize feed-conversion ratios of 1.2 to 1.4.
The piping and aeration on the bottom do not disturb the shrimp. Shrimp often sit astride the pipe between feedings.

Costs
Although PDP offers definite advantages, the capital costs to install a PDP system are significant if facilities are already committed to paddlewheels. PDP piping is not cheap, and the distribution system to deliver air at intermediate pressure can be expensive.
Conventional regenerative or ring blowers do not produce enough pressure to operate PDP systems. Such systems function at 2.7 to 4.0 psig above ambient values, so at a depth of 2 meters, a blower capable of at least 6 psig is needed.
During annual cleaning, pressures roughly double that of normal operating pressures may be needed temporarily for brief periods. Blowers of Roots rotary-lobe or rotary positive-displacement designs are suitable for the task.
There are economies of scale in centralizing blowers, and a single blower can be sized to operate multiple ponds. However, a PDP system capable of supporting 20 tons per hectare per cycle at a 20-ha farm would cost U.S. $12,000 to 15,000 per hectare.
The PDP approach probably does not make sense for growers unless their crop production goals are greater than 8 tons per hectare per cycle. At these intended production levels, the return on investment is less than two years.
Equipment
There are two principal manufacturers of PDP pipe: Air Diffusion Systems of Illinois, USA, and ProAqua of Brisbane, Australia. The main difference between the manufacturers is the diameter of the pipes they produce, with Air Diffusion Systems producing 12-mm pipe and ProAqua producing 19-mm pipe.
The advantage of the larger piping is its ability to make longer runs with lower pressure drop. The 12-mm piping can be used for 60-meter runs if fed from one end, or 110 meters if fed from both ends. The 19-mm pipe can be run for 150 meters when fed from one end and 275 meters when fed from both ends. If even greater distances must be spanned, a floating header can be deployed down the center of the pond to allow doubling the distance covered by the PDP pipe. The level of air delivery is controlled by the number of slots per meter.
Layout
The layout of PDP piping is simple. A header pipe is run along one edge of the pond with penetrations made along its length to run air into the feeder pipe. The feeder pipe runs air to the bottom and releases air into the PDP pipe. Since the feeder and PDP pipes have integral ballast, there is no need to add weights to hold them down.
Another advantage of PDP over diffusion piping is that the pressure differential of the pipes’ operation allows them to deliver uniform air flow over a fairly wide range of bottom elevation. The PDP pipes are placed a specific distance apart to maximize the mixing produced by the vertical gyre. The optimum spacing is 2.82 times the water depth, so at 2 meters of water depth, the pipes would be about 5.6 meters apart.
(Editor’s Note: This article was originally published in the June 2004 print edition of the Global Aquaculture Advocate.)
Now that you've reached the end of the article ...
… please consider supporting GSA’s mission to advance responsible seafood practices through education, advocacy and third-party assurances. The Advocate aims to document the evolution of responsible seafood practices and share the expansive knowledge of our vast network of contributors.
By becoming a Global Seafood Alliance member, you’re ensuring that all of the pre-competitive work we do through member benefits, resources and events can continue. Individual membership costs just $50 a year.
Not a GSA member? Join us.
Author
-
Rod McNeil
Director, Research and Development
Meridian Aquatic Technologies LLC
Kerr Dam Road
P.O. Box 876
Polson, MT 59860 USA
Tagged With
Related Posts
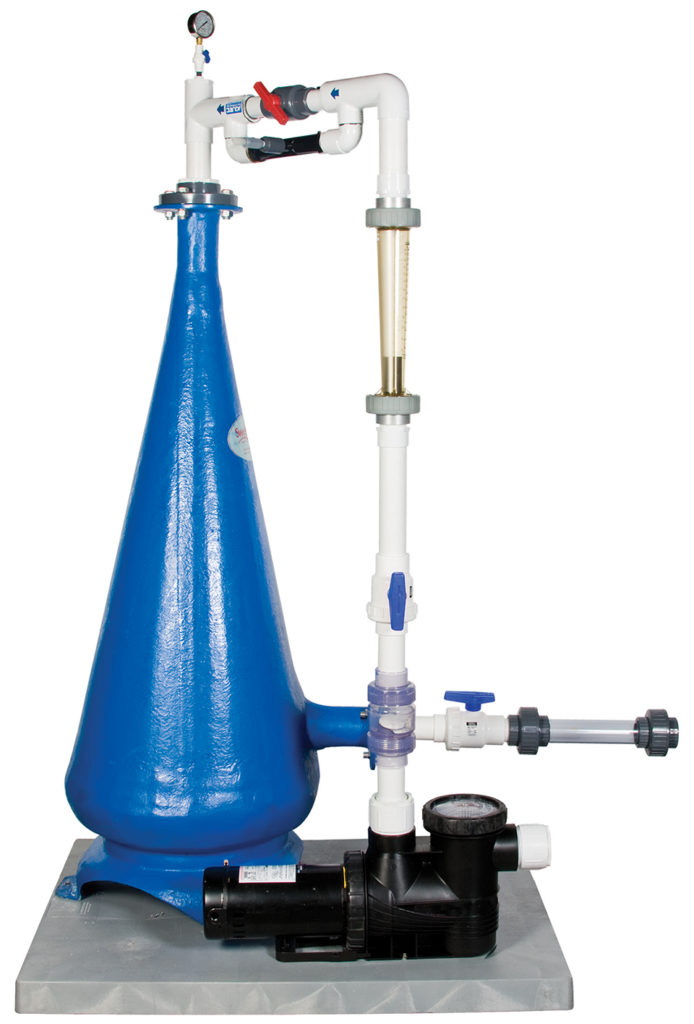
Responsibility
A look at unit processes in RAS systems
The ability to maintain adequate oxygen levels can be a limiting factor in carrying capacities for RAS. The amount of oxygen required is largely dictated by the feed rate and length of time waste solids remain within the systems.
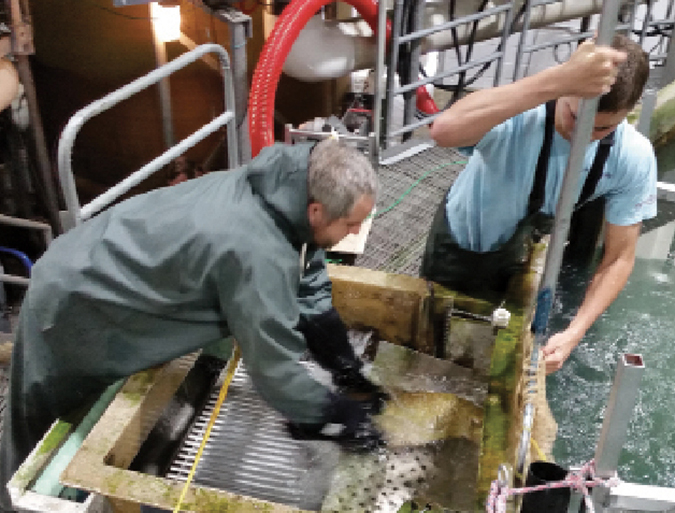
Health & Welfare
Novel air-based system transfers large salmon during harvest
To evaluate the application of an air pressure-based transport method within a recirculating aquaculture system, the authors performed testing with harvest-size salmon at The Conservation Fund Freshwater Institute.
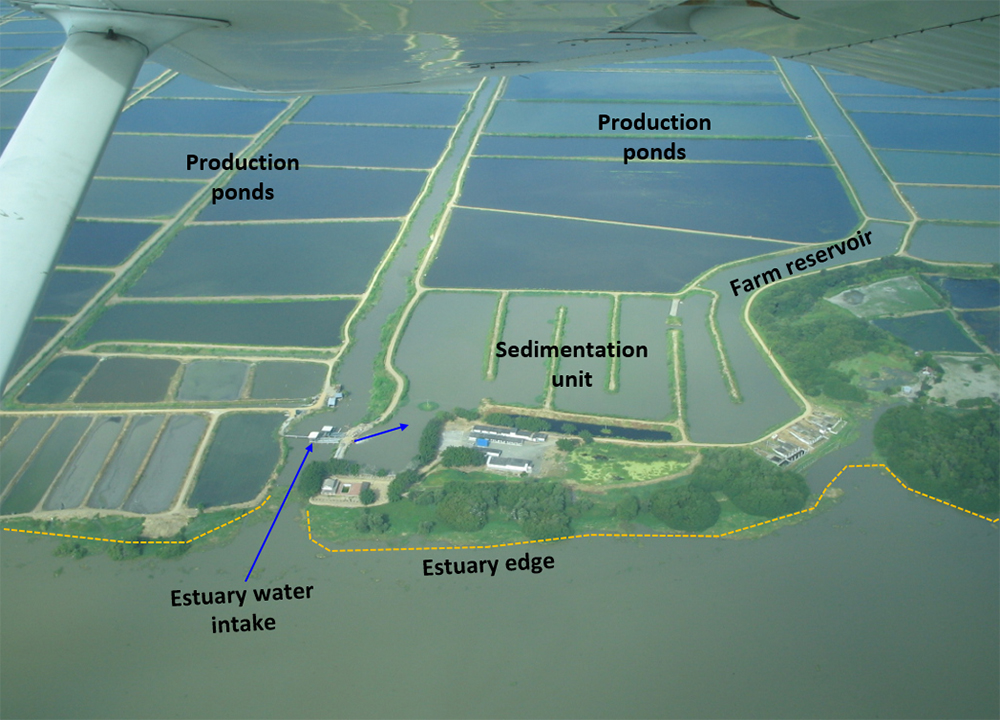
Responsibility
Retrofitting shrimp farms to recirculating systems
Several large shrimp farms in Latin America, originally built to operate using significant, flow-through water exchange with the surrounding environment, have been retrofitted to a recirculating operation mode. This modification provides numerous benefits, including improved biosecurity.
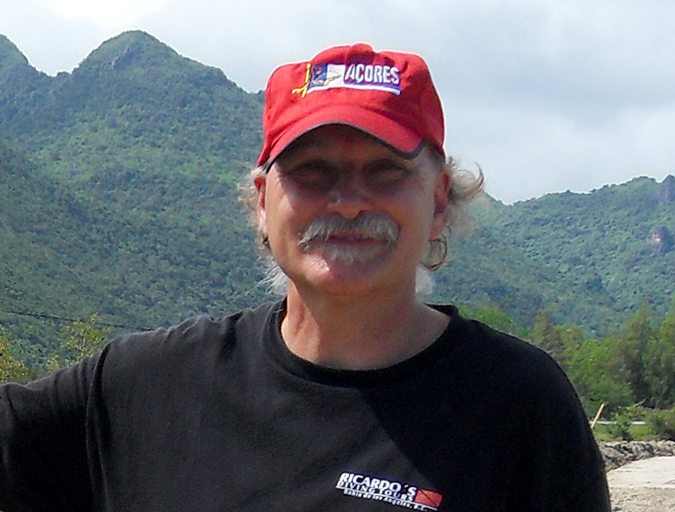
Innovation & Investment
Aquaculture Exchange: Barry Costa-Pierce, UNE
University of New England Professor Barry Costa-Pierce says aquaculture is often neglected in studies examining ocean health and ecosystem and resource management. The “Ocean Prosperity Roadmap” released this summer, he said, was more of the same.