Economic analysis compares modular, multiple-batch production

For channel catfish producers in the United States, the current challenges of rising feed and fuel costs require a focus on efficient production systems that lower costs of production. Research results obtained from both experimental and commercial-size ponds demonstrate that the modular catfish production system may become part of that focus by producing catfish in a very consistent and cost-efficient manner. Further research focused on increasing catfish survival rates through disease control would also reduce production costs.
Modular approach

Over the past several years, the authors evaluated modular catfish production system consisting of three growth periods – fry to fingerling, fingerling to stocker and stocker to harvest phases – in Mississippi, USA. This approach contrasts with the traditional multiple-batch production system for catfish based on continuous harvest of food fish combined with restocking of fingerlings into the same production pond as larger fish are removed for transport to the processing plant.
Multibatch systems can have three or more different size classes of catfish in the pond at a time. In the modular system, all fish are completely harvested at the end of each phase and either restocked into the next phase of growth or transported to the processor at harvest size.
Modular production offers better fish inventory control than the multiple-batch system, takes full advantage of early-age growth rates and results in reduced variation in fish size at harvest. Because each production phase in the modular system allows isolation of different fish sizes, bird predation can be substantially reduced by locating ponds of smaller fish in more active areas of the farm. Additionally, managers have the ability to respond quickly to changes in fish size specifications from processing plants by changing the stocking density in the final grow-out phase.
Fingerling to stocker phase
During 2004 and 2005, the authors carried out studies in small, 0.048-hectare research ponds devoted to optimizing the fingerling to stocker phase. In study 1, 10.90-cm, 10.5-gram fingerlings were stocked at about 98,850; 123,550 and 148,250 fish per ha initial densities. A 35 percent-crude protein fingerling feed was fed daily to satiation over a grow-out of six months.
In study 2, 11.94-cm, 13.8-g fingerlings were stocked at 123,550 per ha and fed either a low- or high-cost 35 percent-protein fingerling diet.
Verification study
In 2006-2007, a verification study was conducted in commercial-scale 1.62-ha earthen ponds to determine whether the production achieved in the fingerling to stocker and stocker to harvest phases was economically practical and comparable to the multiple-batch system.
Starting with the fingerling to stocker phase, channel catfish fingerlings of about 11.9-cm length and 13.8-gram weight. were stocked into six ponds in early April at a density of 123,550 per ha. They were daily fed a 35 percent-crude protein, floating fingerling feed to satiation every day, unless some physical or biological factor warranted a brief cessation.
After 142 days, the individual weight of fish samples from all ponds ranged 30.70 to 38.28 grams. Feeding continued approximately three months, and fish were harvested in late January of 2007. At that time, the individual weight of fish harvested from all ponds ranged 22.40-32.70 grams with a mean of 29.25 grams. Survival ranged 38.8 to 62.0 percent with a mean of 47.7 percent – approximately 20 percent lower than that obtained in the small experimental ponds.
Mortality was primarily attributed to several incidences of proliferative gill disease and enteric septicemia of catfish (ESC). To mitigate mortality due to ESC, a feed incorporating a commercial medication was fed according to the recommended protocol.
Harvested fish were then stocked at 12,350 or 16,065 animals per ha into each of three 1.62-ha ponds for the final stocker to harvest size period of growth.
For both phases of culture, two in-pond paddlewheel aerators that collectively provided the equivalent of 9.9 hp per ha were operated as needed to ensure that levels of dissolved oxygen did not decrease below 4 ppm.
Economic analysis
In studies that involved both experimental and verification ponds, an economic analysis compared the costs of stocker to food-size production in the modular system to the costs for multiple-batch production. The costs of stocker production from the two studies using results from the experimental ponds and the third study using commercial-sized ponds are presented in Table 1.
Hanson, Costs for stocker and food fish production, Table 1
Stocker Variable Costs (U.S. $/kg) | Food Fish Variable Costs (U.S. $/kg) | Fixed Costs (U.S. $/kg) | Total (U.S. kg) |
---|
Stocker Variable Costs (U.S. $/kg) | Food Fish Variable Costs (U.S. $/kg) | Fixed Costs (U.S. $/kg) | Total (U.S. kg) | |
---|---|---|---|---|
Study 1 98,850/ha 123,550/ha 148,250/ha | – 0.346 0.309 0.289 | – 0.937 0.928 0.931 | – 0.168 0.161 0.154 | – 1.451 1.398 1.374 |
Study 2 123,550/ha Low-cost feed High-cost feed | – 0.357 0.404 | – 0.889 0.853 | – 0.161 0.161 | – 1.407 1.418 |
Study 3 123,550/ha | – 0.397 | – 0.891 | – 0.161 | – 1.449 |
Multiple batch | – – | – 1.316 | – 0.161 | – 1.477 |
For study 1, the total production costs were estimated at U.S. $0.026 to 0.103 per kg less that those reported for the multi-batch production system. In study 2, the total cost of production was estimated $0.059 to 0.070/kg less than that for the multi-batch system. For study 3, stocker production cost was higher than that obtained from results in the small research ponds, but overall cost was $0.028 per kg less than in the multiple-batch system.
(Editor’s Note: This article was originally published in the September/October 2008 print edition of the Global Aquaculture Advocate.)
Now that you've reached the end of the article ...
… please consider supporting GSA’s mission to advance responsible seafood practices through education, advocacy and third-party assurances. The Advocate aims to document the evolution of responsible seafood practices and share the expansive knowledge of our vast network of contributors.
By becoming a Global Seafood Alliance member, you’re ensuring that all of the pre-competitive work we do through member benefits, resources and events can continue. Individual membership costs just $50 a year.
Not a GSA member? Join us.
Authors
-
Terry Hanson, Ph.D.
Department of Fisheries and Allied Aquacultures
203 Swingle Hall
Auburn, Alabama 36849 USA -
Lou D’Abramo, Ph.D.
Department of Wildlife and Fisheries
Mississippi State University
Mississippi State, Mississippi, USA -
Jim Steeby, Ph.D.
National Warmwater Aquaculture Center
Mississippi State University
Stoneville, Mississippi, USA
Tagged With
Related Posts
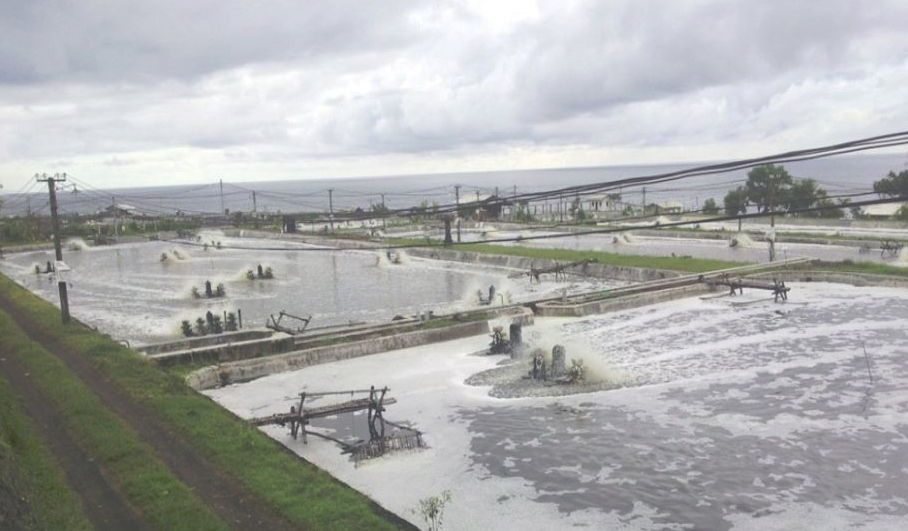
Responsibility
A look at various intensive shrimp farming systems in Asia
The impact of diseases led some Asian shrimp farming countries to develop biofloc and recirculation aquaculture system (RAS) production technologies. Treating incoming water for culture operations and wastewater treatment are biosecurity measures for disease prevention and control.
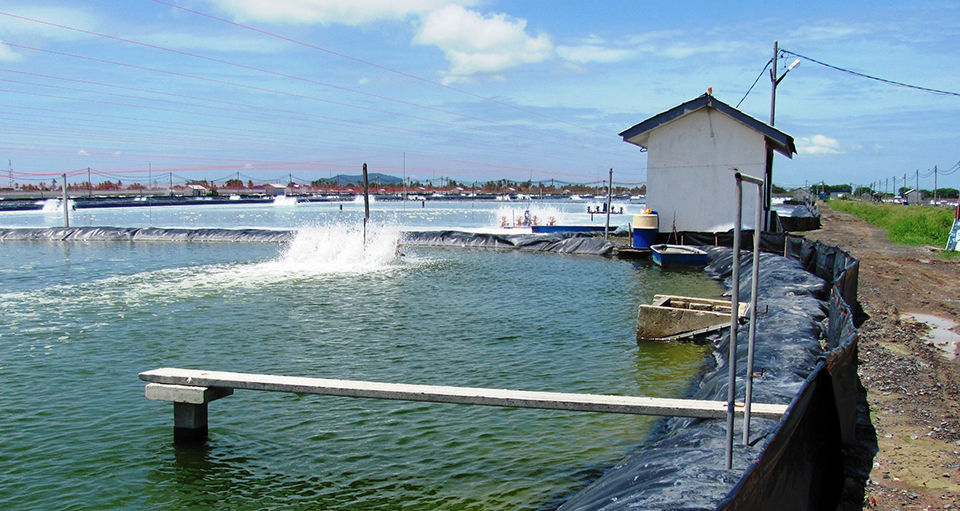
Health & Welfare
Biosecurity for shrimp farms
With the global spread of viruses, biosecurity has become an essential element of every shrimp farm. Biosecurity starts with quality of farm design.
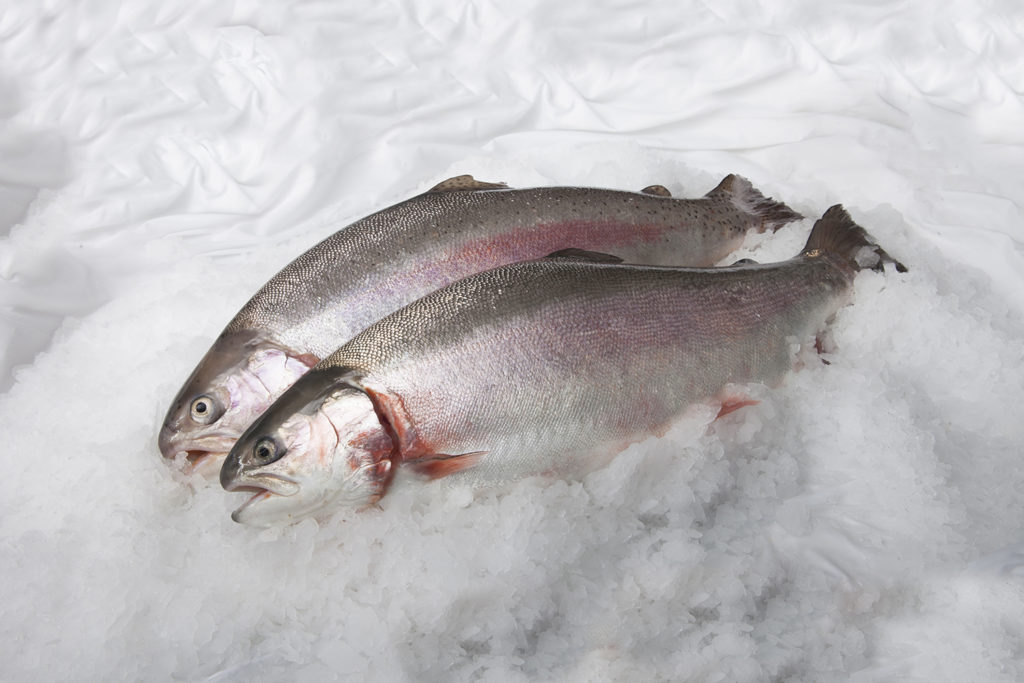
Innovation & Investment
Developments in closed-containment technologies for salmonids, part 1
The recent 2017 Aquaculture Innovation Workshop in Vancouver brought together numerous stakeholders involved in and interested in fish farming – particularly salmonids – in the growing industry of closed-containment systems.
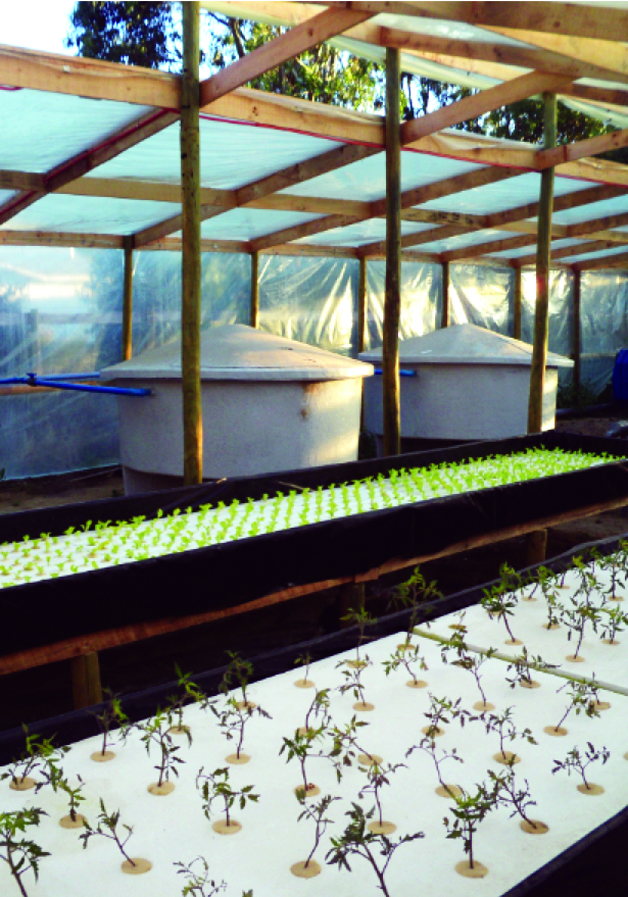
Health & Welfare
Integrated aquaponics systems evaluated for arid zones of Chile
Integrated aquaponic operations can improve water use efficiency because plants participate in nitrogen and phosphorus removal and integration.