Potential for nearly complete water recovery for reuse

Fish farming using recirculating aquaculture systems (RAS) can produce wastewater containing high concentrations of total suspended solids (TSS), nitrogen, phosphorus and biological oxygen demand. Often, this wastewater flow is more highly concentrated in pollutants than water treated at municipal wastewater treatment plants. As a result, some form of solids removal and nutrient recovery is needed prior to discharge. If the intent is to reclaim and reuse this water resource, then advanced secondary wastewater treatment is required.
Membrane biological reactors
Membrane biological reactors (MBRs) provide highly scalable, on-site wastewater treatment that utilizes activated sludge to remove nitrogen (nitrification and denitrification mechanisms), phosphorus (microbial assimilation), and five-day biological oxygen demand. Further, membranes submerged in the activated sludge are capable of filtering out a particulate-free permeate. Consequently, MBRs have the potential for nearly complete water recovery for reuse in fish culture systems.
The MBR located at the Conservation Fund’s Freshwater Institute in West Virginia, USA, was operated for the recovery of not only the water but the alkalinity, salts, phosphorus and protein contained in a highly concentrated aquaculture wastewater. The work was supported by a cooperative agreement with the United States Department of Agriculture – Agricultural Research Service.
The RAS uses biological filters to convert the total ammonia nitrogen (TAN) excreted by fish into nitrate-nitrogen. The net result is a backwash of biosolids that is low in TAN and high in nitrate-nitrogen.
The biosolids discharge from RAS that use low water flushing rates could contain nitrate-nitrogen and orthophosphate concentrations as high as 100 mg/L and 3 mg/L, respectively. And RAS utilizing biological filters operated at low flushing rates quickly consume alkalinity, which requires the addition of sodium bicarbonate to maintain alkalinity concentrations above 100 mg/L as calcium carbonate.
Study setup
In an experiment designed to determine the nutrient removal and resource reclamation capacity of an MBR, typical backwash wastewater collected from an RAS operated for rainbow trout culture was loaded to the biological reactor (control condition). In order to mimic waste produced from fish culture systems operated at low flushing rates, appropriate proportions of sodium nitrate and granular anhydrous monopotassium phosphate were added to the wastewater entering the MBR to achieve an additional 100 mg/L nitrate-nitrogen and 3 mg/L phosphorus. Each condition was maintained for 21 days and replicated four times.
Activated sludge must be removed from the MBR at regular intervals to maintain a consistent suspended solids concentration in a process termed “biosolids wasting.” As a result, a small amount of potentially reclaimable backwash is lost along with the wasted biosolids.
The research performed for this study indicated that the MBR processed approximately 7.1 cubic meters of RAS backwash daily, and the activated sludge wasting rate was approximately 460 L/day. The resulting wastewater recovery rate was approximately 93.5 percent, indicating little loss of reclaimable backwash due to activated sludge solids wasting and disposal.
Results
The MBR performed well, removing 99.97 percent and 99.98 percent of the total suspended solids under control and test conditions, respectively (Table 1). Similarly, no difference in five-day carbonaceous biological oxygen demand removal was apparent, with 100 percent removal.
Sharrer, Mean (± standard error) water quality parameters, Table 1
Total Suspended Solids | Total Volatile Solids | Five-Day Biological Oxygen Demand | Alkalinity |
---|
Total Suspended Solids | Total Volatile Solids | Five-Day Biological Oxygen Demand | Alkalinity | |
---|---|---|---|---|
Test Condition | ||||
Influent (mg/L) | 1,827 ± 272 | 1,488 ± 224 | 1,073 ± 182 | 281 ± 8 |
Effluent (mg/L) | 0.3 ± 0.1 | 0.2 ± 0 | 0 ± 0 | 560 ± 19 |
Removal efficiency | 99.98% | 99.99% | 100% | -115% |
Control Condition | ||||
Influent (mg/L) | 2,235 ± 346 | 1,768 ± 266 | 658 ± 98 | 259 ± 5 |
Effluent (mg/L) | 0.7 ± 0.3 | 0.2 ± 0 | 0 ± 0 | 312 ± 10 |
Removal efficiency | 99.97% | 99.99% | 100% | -21% |
Recovery of alkalinity was observed under both control and test conditions. Influent and effluent alkalinities were 259 ± 5 and 312 ± 10, respectively, under control conditions and 281 ± 8 and 560 ± 19, respectively, under test conditions (Table 1).
According to the United States Environmental Protection Agency Nitrogen Control manual, for each gram of nitrate-nitrogen that undergoes denitrification, approximately 3.70 grams of chemical oxygen demand is consumed, 0.45 grams of new cell is produced and 3.57 grams of alkalinity is formed. As a result, complete recovery of alkalinity was accomplished under control conditions, and enhanced recovery was observed under test conditions.
The alkalinity recovered in the permeate could replace the requirement for inorganic carbon supplementation in fish culture systems that operate at low make-up rates and utilize nitrification reactors for ammonia removal.
The MBR also achieved impressive nitrogen removal at either typical or elevated nutrient loading rates. Total nitrogen entering the MBR was 86 ± 10 mg/L under control conditions and 185 mg/L under test conditions with removal efficiencies of 98 percent under both conditions (Table 2). TAN and nitrate-nitrogen removal efficiencies were marginally reduced under test conditions, but their permeate concentrations were remarkably low at either nutrient loading condition.
Sharrer, Mean (± standard error) water quality parameters, Table 2
Total Nitrogen | Total Ammonia Nitrogen | Nitrate-Nitrogen | Total Phosphorus | Dissolved Reactive Phosphorus |
---|
Total Nitrogen | Total Ammonia Nitrogen | Nitrate-Nitrogen | Total Phosphorus | Dissolved Reactive Phosphorus | |
---|---|---|---|---|---|
Test Condition | |||||
Influent (mg/L) | 185* | 3.3 ± 0.9 | 105* | 55* | 5.6* |
Effluent (mg/L) | 2.1 ± 1.4 | 1.3 ± 0.6 | 0.6 ± 0.3 | 0.10 ± 0.03 | 0.10 ± 0.03 |
Removal efficiency | 98.0% | 60.6% | 88.0% | 99.8% | 96.1% |
Control Condition | |||||
Influent (mg/L) | 86 ± 10 | 2.1 ± 0.2 | 4.9 ± 1.4 | 50 ± 8 | 1.8 ± 0.2 |
Effluent (mg/L) | 1.8 ± 0.5 | 0.4 ± 0.3 | 0.1 ± 0 | 0.05 ± 0.01 | 0.05 ± 0.01 |
Removal efficiency | 98.0% | 81.0% | 98% | 99.9% | 97.2% |
Useful by-products
Phosphorus recovery in the MBR occurs as bacteria in the activated sludge take in this nutrient in excess when subjected to alternating aerobic and anaerobic conditions. The MBR produced exceptional phosphorus removal efficiencies under both control and test conditions, producing permeate total phosphorus concentrations of 0.10 ± 0.03 under test and 0.05 ± 0.01 under control conditions (Table 2). The phosphorus captured in the activated sludge can be further used in terrestrial agriculture as a soil amendment, potentially displacing the need for fertilizers derived from phosphate rock.
Another potential resource recovery process could utilize the proteins captured by the microorganisms in the activated sludge as a feed additive. The protein content of the sludge generated in this experiment was 25.2 ± 2.9 percent on a dry-weight basis, which is a little lower than the desired content needed for a feed additive. However, an MBR operated at a lower sludge age can produce activated sludge with higher protein content. Further research on this aspect is now under way.
Perspectives
Installation of MBR technology requires significant capital and ongoing operating costs. However, reclamation and reuse of wastewater could be an option for land-based RAS culture systems operating with limited water resources or utilizing costly synthetic or transported saltwater. Further, the ability to perform on-site, biosecure wastewater treatment while reclaiming water, salts, alkalinity, phosphorus and protein makes adoption of this technology even more appealing.
Editor’s Note: This article is a summary of an article by the authors that appeared in Bioresource Technology.
(Editor’s Note: This article was originally published in the July/August 2010 print edition of the Global Aquaculture Advocate.)
Now that you've reached the end of the article ...
… please consider supporting GSA’s mission to advance responsible seafood practices through education, advocacy and third-party assurances. The Advocate aims to document the evolution of responsible seafood practices and share the expansive knowledge of our vast network of contributors.
By becoming a Global Seafood Alliance member, you’re ensuring that all of the pre-competitive work we do through member benefits, resources and events can continue. Individual membership costs just $50 a year.
Not a GSA member? Join us.
Authors
-
Mark J. Sharrer
The Conservation Fund’s Freshwater Institute
1098 Turner Road
Shepherdstown, West Virginia 25443 USA -
Kata Rishel
The Conservation Fund’s Freshwater Institute
1098 Turner Road
Shepherdstown, West Virginia 25443 USA
Related Posts
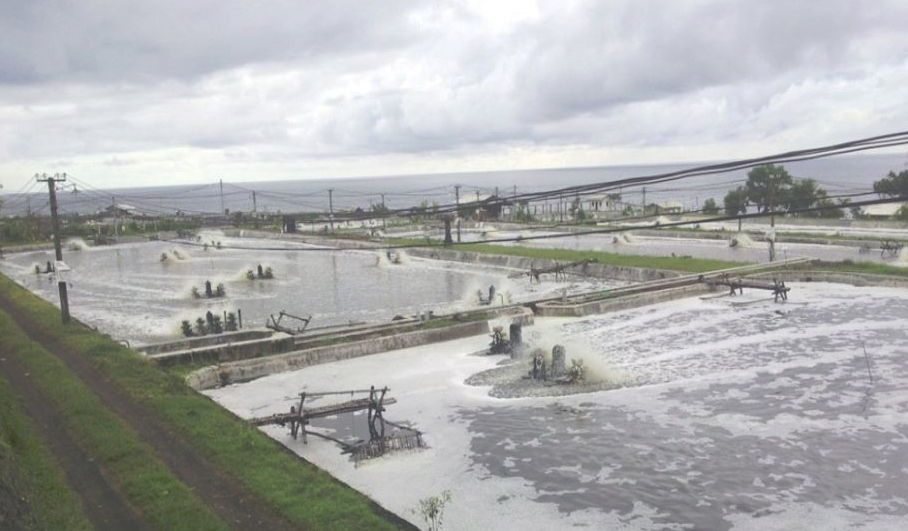
Responsibility
A look at various intensive shrimp farming systems in Asia
The impact of diseases led some Asian shrimp farming countries to develop biofloc and recirculation aquaculture system (RAS) production technologies. Treating incoming water for culture operations and wastewater treatment are biosecurity measures for disease prevention and control.
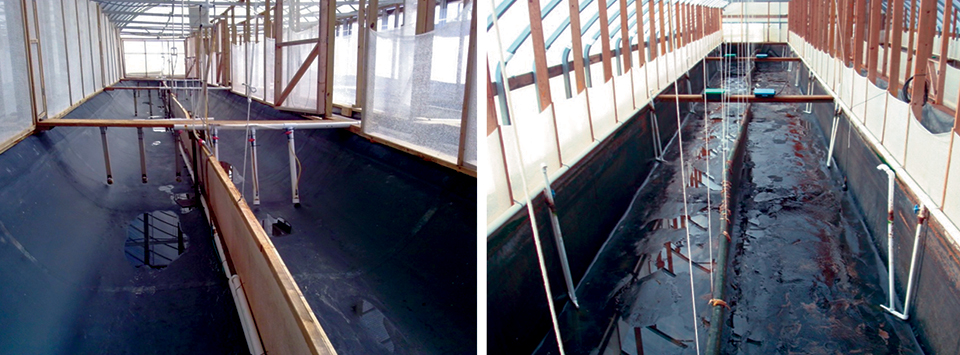
Responsibility
Advances in super-intensive, zero-exchange shrimp raceways
Research at the Texas AgriLife Research Mariculture Laboratory is investigating ways to improve the economic viability of super-intensive raceways for shrimp production.
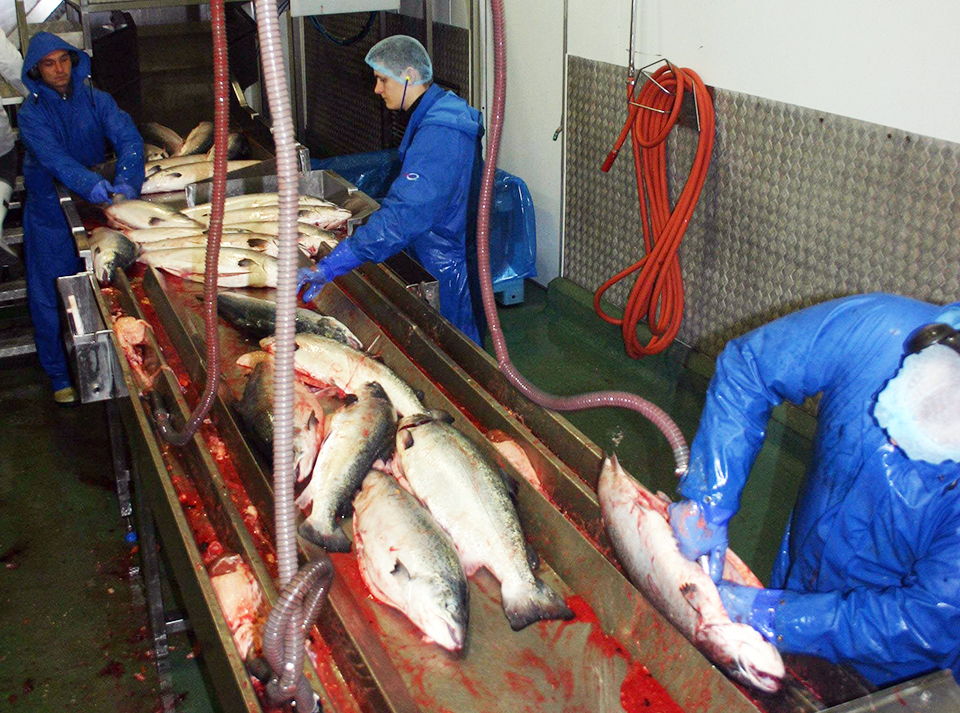
Responsibility
Aquaculture byproducts improve sustainability of seafood value chains
Tons of aquaculture byproducts are available as sources for fishmeal and fish oil to supplement the supplies obtained from fisheries. Innovative technologies are supporting more efficient use of these by-products in aquafeed.
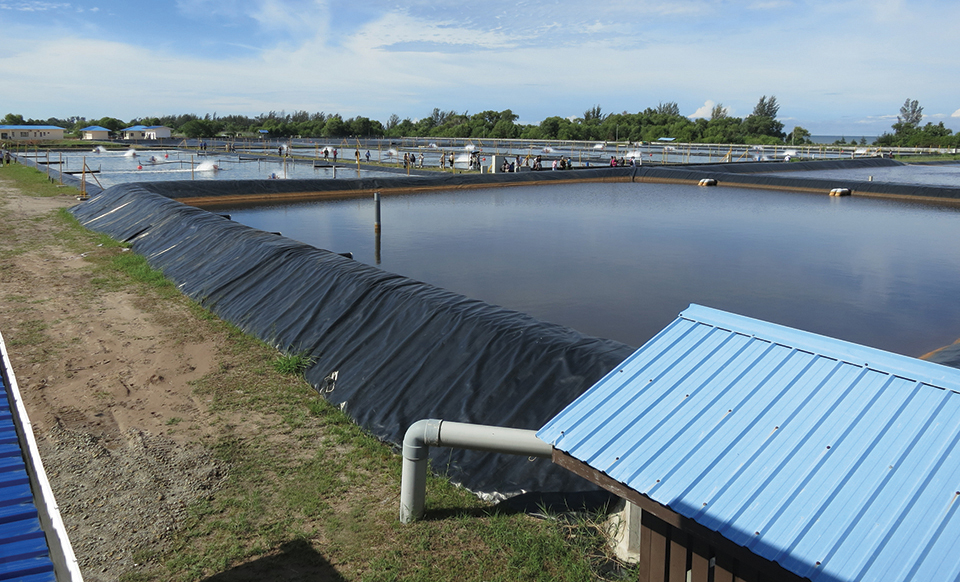
Health & Welfare
Brunei project develops technology for large black tiger shrimp production, part 5
The final article in a series about a project in Brunei to develop technology for production of black tiger shrimp focuses on the development of advanced grow-out ponds and practices with enhanced systems for biosecurity, sludge removal, water reuse, energy efficiency, automatic feeding and mechanical harvesting.