First phase of iSHARP project nearly complete

A large-scale integrated shrimp aquaculture park (iSHARP) project started by Blue Archipelago Berhad in Malaysia in 2009 is approaching completion of its first phase of operations. Based on biosecure recirculating systems using biofloc technology along with an associated hatchery and processing plant, iSHARP expected to build 216, 0.5-ha culture ponds by the end of 2012. Its goal is to complete over 600 ponds and reservoirs for raising Pacific white shrimp, Litopenaeus vannamei, on 1,000 ha of land.
The project is located at Setiu in the state of Terengganu, northeast of Kuala Lumpur. A total of 144 ponds were in operation when this article was written in mid-November 2012. No incidents of white spot syndrome or early mortality syndrome have been reported at the facility.
Biosecure modules
Biosecurity is a priority at iSHARP. Each commercial unit or module comprises two rows of 12 growout ponds with four treatment ponds. Their design allows individual modules or ponds to be completely “locked down” to prevent disease from spreading.
Water from the main supply canal is pumped through the treatment ponds before entering a module supply canal, which is elevated to remain dry when not in use. Dikes lined with high-density polyethylene (HDPE) incorporate crab fencing approximately 30 cm outside the pond perimeters.
Lined discharge canals are shared by two modules. Secured inlet and outlet gates prevent contamination between culture ponds and canals. They also help conserve treated water in the zero-water-exchange system. Culture ponds each include a harvest pit to avoid contamination with waste water during harvest.
Biosecurity measures are mainly applied to prevent outbreaks of white spot syndrome. In addition to basic measures such as bird nets and crab fencing, other farm biosecurity practices involve keeping farm equipment clean and controlling the movement of farm technicians and pond operators.
Strict biosecurity also needs to be implemented for visitors when entering growout facilities. All visitors need to strictly follow one simple rule: Look, but don’t touch.

Culture water treatment
Seawater for the whole farm is drawn via an HDPE-lined pipe from 1.8 km offshore to a large-volume pump station. From the main pump house, water is distributed through 2.5 km of HDPE-lined main canal to the culture modules.
There is no way to contaminate the main pump, as it is on the dike when not in operation. The inlet pipes are fitted with 250-μ mesh screens covered by 1,000-μ mesh to strengthen the nets. The water then has to pass through the treatment ponds before being pumped into module supply canals.
During this period, the water is treated with a crustacide at 1 ppm to eradicate crabs and other potential disease carriers that could enter the modules. The seawater that finally flows into ponds has aged for 74 hours, which is the time at which white spot syndrome virus particles disintegrate without a live host to infect.
Effluent treatment
The project is designed as a recirculating aquaculture system. All discharge waters are directed to a main settling basin to be treated for reuse or discharge back to the environment.
The treatment system involves four phases. Beyond the settling basin, large first and second treatment canals contain fish, mussels, oysters and seaweeds for biofiltration of suspended particles and nitrification of dissolved effluence. The fourth and final ponds provide aeration and chemical treatment with chlorine or liming before the water is returned to the main supply canal or discharged. Water quality parameters such as chemical and biochemical oxygen demand, total ammonia nitrogen and phosphate levels are routinely checked against Malaysia’s government requirements.
Biofloc technology
For optimized, sustainable commercial biofloc shrimp culture, HDPE- or concrete-lined ponds are basic requirements. High stocking densities of 130-150 postlarvae/m2 and high aeration rates of 28-32 hp/ha are also essential for expected production over 20 mt/ha. Energy efficiency is 680 kg/hp and can be as high as 1,000 kg/hp in partial harvest. Paddlewheel aerators placed in ponds keep dissolved-oxygen levels high, suspend biofloc and guide sludge toward the central areas of ponds. The sludge can then be siphoned out periodically when needed.
Bioflocs are conglomerates of microbes, algae and protozoa together with detritus and dead organic particles. The aerators help suspend the bioflocs in the pond water – a main requirement for maximizing the potential of microbial processes in shrimp culture ponds. The suspended biofloc is also readily available as feed for shrimp.
Pelleted grain and molasses are used to sustain carbon:nitrogen ratios above 15. In addition to typical chemicals such as dolomite and lime, kaolin is required in the preparation of pond water and during operation. Kaolin is applied at 50-100 kg/ha.
Operation, control
Only specific pathogen-free postlarvae are stocked. Once ponds are stocked, a major factor to control is biofloc volume. Using Imhoff cones for assessment, biofloc volumes need to be maintained below 15 mL/L for full biofloc and 5 mL/L for semi-biofloc systems. At least two samples need to be taken concurrently from two locations below the water surface. Green or brown water is acceptable, but black water is an indicator of abnormal conditions.
Grain pellets and molasses supply carbon as needed. Generally, grain pellet applications vary from 15 to 20 percent of the total feed used during operations. Molasses can be applied two or three times weekly at 15-20 kg/ha/pond. Dissolved-oxygen levels need to be monitored frequently to keep levels higher than 4 mg/L. Especially in biofloc systems, aerators need to be constantly monitored for malfunctions and repaired or replaced without delay. At the present, most of the iSHARP ponds are “semi-biofloc” systems used to train technicians. Only a few ponds have full biofloc levels. During trials, when monsoon season and its heavy rainfall and flooding approached, densities of 40, 60, 80 and 130 postlarvae/m2 (full biofloc) were stocked to determine a benchmark for the farm. For the first commercial production cycle, the two initial pond modules were stocked with 100 P.L.10/m2 and applied semi-biofloc technology. Presently, the two modules are in the third cycle under normal culture conditions.
Performance
The performance data for a trial and first commercial run are shown in Table 1 and Figs. 1 and 2. The trial was a success but, as expected, had management and environmental problems due to heavy rainfall and flooding. The salinity dropped from 22 ppt to as low as 12 ppt in two weeks, then fell to 4 ppt in some ponds. Temperatures were as low as 24 degrees-C during the culture period.
Park, Performance of shrimp, Table 1
Trial – Modules 1 and 2 Density (40/m2) | Trial – Modules 1 and 2 Density (60/m2) | Trial – Modules 1 and 2 Density (80/m2) | Trial – Modules 1 and 2 Density (130/m2>) | Cycle 1 – Modules 1 and 2 Density (100/m2) | Cycle 1 – Modules 1 and 2 Density (100/m2) |
---|
Trial – Modules 1 and 2 Density (40/m2) | Trial – Modules 1 and 2 Density (60/m2) | Trial – Modules 1 and 2 Density (80/m2) | Trial – Modules 1 and 2 Density (130/m2>) | Cycle 1 – Modules 1 and 2 Density (100/m2) | Cycle 1 – Modules 1 and 2 Density (100/m2) | |
---|---|---|---|---|---|---|
Number of ponds | 20 | 16 | 8 | 4 Biofloc | 24 Biofloc | 24 Biofloc |
Aeration (hp) | 12 | 12 | 12 | 16 | 12 | 12 |
Days of culture | 113 | 108 | 94 | 88 | 100 | 99 |
Survival (%) | 112.23 | 101.22 | 106.05 | 69.56 | 97.30 | 104.92 |
Body weight (g) | 21.65 | 17.41 | 13.86 | 12.56 | 16.05 | 16.31 |
Feed-conversion ratio | 1.34 | 1.47 | 1.32 | 1.74 | 1.39 | 1.26 |
Average production (kg/pond) | 4,875 | 5,294 | 5,828 | 5,677 | 7,714 | 8,547 |
Average production (kg/ha) | 9,749 | 10,587 | 11,655 | 11,354 | 15,428 | 17,093 |
Production/power input (kg/hp) | 406 | 441 | 486 | 355 | 643 | 712 |


The heavy rain caused pond water levels to increase, and at times, water levels in the discharge canal were higher than in the ponds, which made it impossible to siphon out sludge and resulted in unstable pond water environmental condition. For these reasons, the two biofloc ponds had to be harvested prematurely. The remaining two ponds did well but below the targeted performance. The low-density ponds performed as expected.
The first commercial cycle, stocked with 100 P.L./m2 under 24 hp/ha energy and semi-biofloc conditions, performed better than expected. The target was to produce an average of 7.0 metric tons (MT) per pond, but harvests of 7.7-8.5 MT/pond were achieved. The environmental conditions were stable during the period with high salinity and high temperatures.
The shrimp in the commercial cycle took 100 days to reach average marketable sizes of 16.0 and 16.3 grams. For feed conversion, both modules performed as expected, with rates between 1.39 and 1.26, and in some ponds, as low as 1.2. Another important economic factor was energy efficiency. As expected, in biofloc systems, the energy efficiency was between 643 and 712 kg/hp.
Due to cases of overstocking in the commercial cycle, the survival data indicated values over 100 percent. Since survival is an important tool to control pond carrying capacity during culture operations, iSHARP needs to be prepared to cope with this situation, possibly by using an autocounter for more accuracy in the future. To address survival rates, contingency plans could account for extra energy inputs and early or partial harvests.
Lined ponds reduce pond preparation times and enable more than two cycles in one year. About 2.4 cycles in one year are probably possible.
(Editor’s Note: This article was originally published in the January/February 2013 print edition of the Global Aquaculture Advocate.)
Authors
-
Nyan Taw, Ph.D.
Senior Technical Advisor
Blue Archipelago Berhad
T3-9, KPMG Tower, 8 First Avenue
Persiaran Bandar Utama 47800, P.J.
Selangor, Malaysia -
Umar Saleh, M.S.
Bujang Slamat
i SHARP Farm
Blue Archipelago Berhad
T3-9, KPMG Tower, 8 First Avenue
Persiaran Bandar Utama 47800, P.J.
Selangor, Malaysia
Related Posts
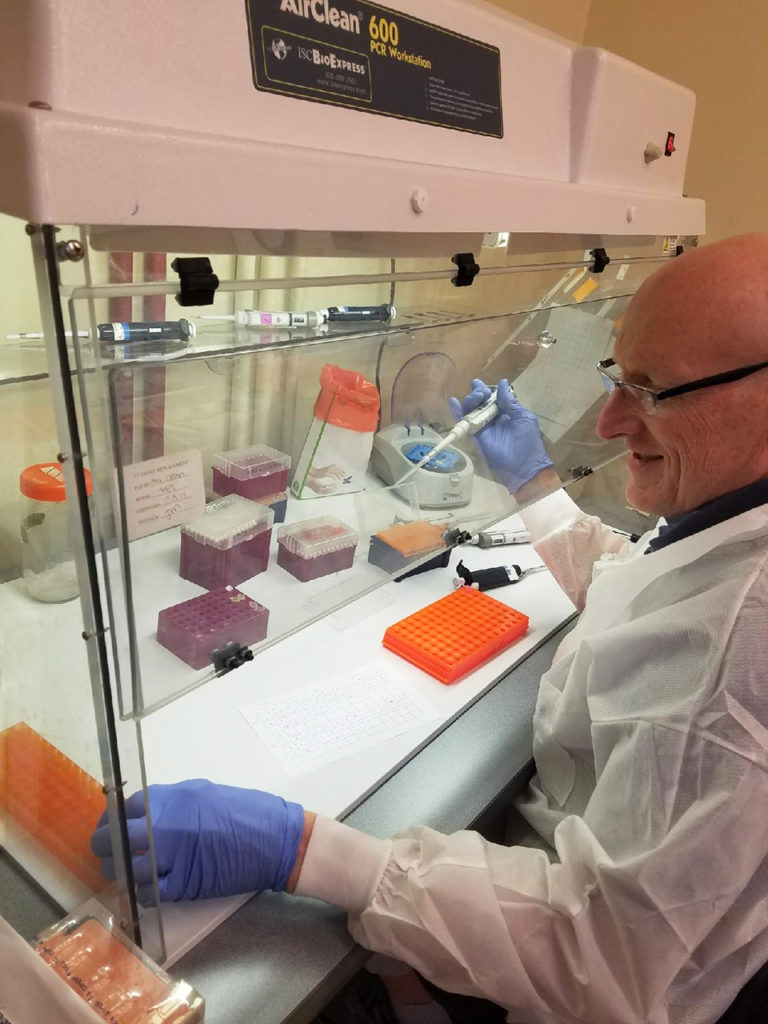
Health & Welfare
A comprehensive look at the Proficiency Test for farmed shrimp
The University of Arizona Aquaculture Pathology Laboratory has carried out the Proficiency Test (PT) since 2005, with 300-plus diagnostic laboratories participating while improving their capabilities in the diagnosis of several shrimp pathogens.
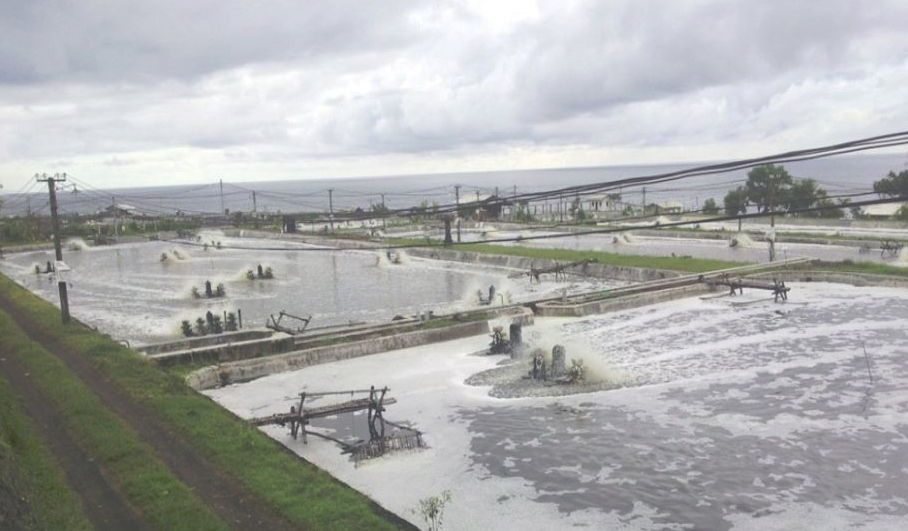
Responsibility
A look at various intensive shrimp farming systems in Asia
The impact of diseases led some Asian shrimp farming countries to develop biofloc and recirculation aquaculture system (RAS) production technologies. Treating incoming water for culture operations and wastewater treatment are biosecurity measures for disease prevention and control.
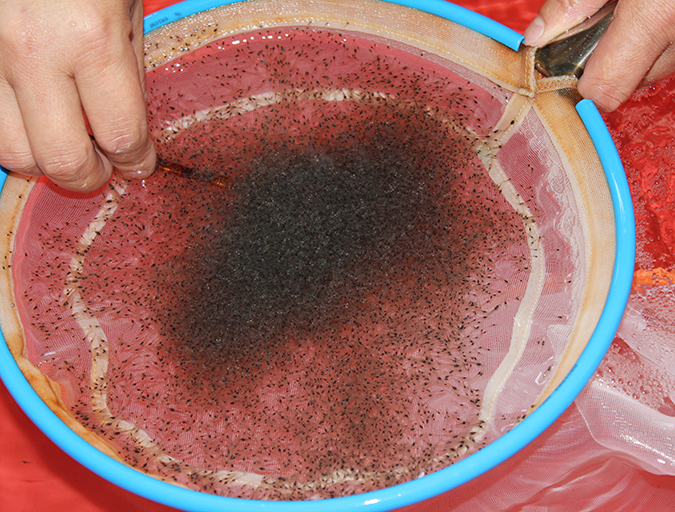
Health & Welfare
Acclimating shrimp postlarvae before pond stocking
Shrimp postlarvae acclimation before stocking into the various growout systems (ponds, raceways, tanks) is a critical – and often overlooked, sometimes taken for granted – step in the shrimp culture process. Various water quality parameters should be changed slowly so that the young shrimp have the time to gradually adapt to the new conditions.
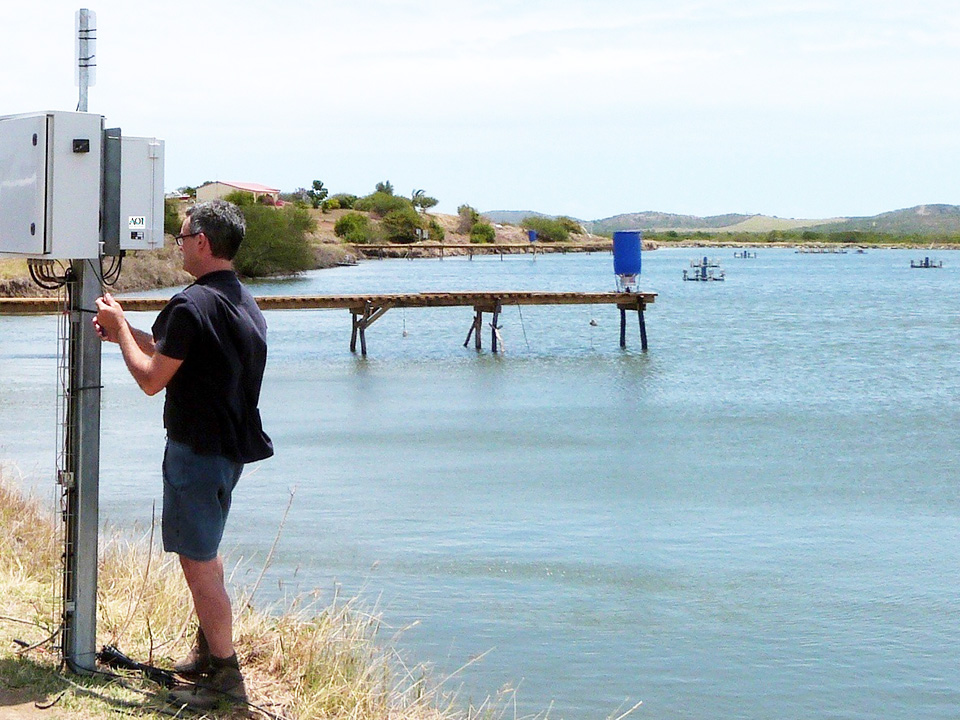
Innovation & Investment
Acoustic control improves feeding productivity at shrimp farms
In systems recently developed for shrimp farms, passive acoustic-based technology enables sensor-based control of multiple automatic feeders. Improved growth and feed conversion have been recorded at commercial farms using the technology.