System developed at University of Georgia Marine Shellfish Laboratory

Computer-controlled water-recirculation and fluidization technologies can help reduce operational costs in a bivalve nursery. These technologies reduce labor requirements, raise the utilization efficiency of algae, and improve systems operation. They can also cut wastes in the seed culture system, sustain water quality for optimum seed growth and reduce fouling of the culture units.
An integrated system utilizing these technologies for the production of algae and culture of northern quahog seed clams (Mercenaria mercenaria) was developed at the University of Georgia Marine Shellfish Laboratory in Savannah, Georgia, USA. Its three units work efficiently together as a test bed for the concept.
Algal culture system
The microalgae Chaetoceros muelleri was selected for the system because it grows well at high temperatures over a wide range of salinities, and is a suitable food source for Mercenaria seed. The algae were grown in conical, 550-liter fiberglass tanks covered with clear plexiglass to minimize the entrance of airborne contaminants. A diaphragm pump supplied air for culture aeration through a 0.2-μ filter. Carbon dioxide was continuously injected into the air line at a rate of 0.5 cubic centimeters per minute for six hours.
Treatment of the incoming brackish water included bag filtration (20 and 5 μ), chlorination, active carbon filtration, ultraviolet sterilization, and ozonation. A one-micron cartridge filter at the central inflow point of the culture tanks was the final water treatment step. Level sensors controlled the water level in each tank, while float valves served as back-up mechanisms to prevent tank overflow.
The millivolt output from a commercial turbidimeter was used to estimate the algal biomass in the culture tanks. A computer-controlled 1/10th-hp centrifugal pump harvested the algal cultures and transferred them to a 500-liter harvest reservoir. A peristaltic pump, activated after harvesting, transferred nutrient solution into each culture tank.
Seed clam nursery
The culture upwellers of the seed clam nursery system were 5 cm in diameter, 76 cm in height, and constructed of clear PVC tubing. A 400-liter feed reservoir and 1/10-hp centrifugal pump recirculated water. An inline solids separator removed the large particulate waste material, and a bead filter provided additional particle entrapment and nitrification.
A flow distribution plate with a radial pattern of 0.32 cm holes provided uniform water flow into the culture upwellers. Above the flow distribution plate was a 1.0 mm Nytex screen for retaining the seed mass. At the base of each upweller, manually adjusted gate valves controlled water flow through the seed mass.
Process control

The computer-control system included a laptop computer, multiport controller for the three control boards, and 10-volt, solid-state relays for each controlled output. The menu-driven control program, written in Turbo Pascal 6.0, contained over 40 commands to monitor or control all components of the integrated system.
The daily start and end times for algal culture sampling and harvesting operations were 8 p.m. and 8 p.m. to cover the range of observed algal growth in the greenhouse. Between these hours, the chambers were sampled every two hours to estimate the standing algal biomass. If the estimated biomass was lower than the harvest set point, the sampling procedure ended and repeated in two hours. If the estimated biomass was greater than the harvest point, command actions initiated the harvest cycle.
The recirculating nursery clam culture system had 10 input parameters. Eight parameters were used to calculate the amount of algae required for feeding the seed clams and adjusted the ration based on estimated clam growth. The other parameters set the frequency and duration of filter backflushing and solids separator purging.
Seed culture
Hatchery-reared northern quahog clam seed of a single cohort was initially stocked into each upweller at 60 grams whole wet weight and mean shell length of 2.5 mm. The initial stocking density was 3.0 grams seed (wet weight) per cubic centimeter. The seed clams were sorted on days 14, 52 and 73 of the 83-day culture period. Based on the amount of available algae, the daily ration ranged 1 to 4 percent dry algae per clam (wet weight).
Algal culture

Algae harvest levels were set at 60 milligrams per liter dry weight from March to October, and 30 milligrams per liter during the winter. Sunlight availability and photoperiod, as well as the ambient temperature in the greenhouse, governed the harvest set point. In the summer months, high ambient air temperature inside the greenhouse raised the water temperature in the closed culture chambers above 35 degrees-C.
To minimize the collapse of algal cultures from the high temperatures, the chambers were batch-harvested approximately every three days at 90 percent of the culture volume. Refilling the chambers with chilled reservoir seawater after such harvest volume helped maintain target culture temperatures below 35 degrees-C.
The 90 percent harvest volume also minimized the growth of biofilm on the tank walls, thereby extending the culture period between tank cleanings and reinoculation. However, this harvest approach made it difficult to maintain a harvest biomass level above 60 milligrams per liter. In the winter, the reduced sunlight and low greenhouse temperatures limited biomass growth. At a four-day harvest interval, a culture biomass level of 30 milligrams per liter was attainable. But beyond the four-day culture period, minimal additional growth was observed.
Culture of seed clams
The growth of the seed clams in the integrated system is presented in Fig. 1. Two weeks after initial stocking, seed survival was 76.8 percent (+11.5 percent). The stocking density was thinned from 3.7 grams of clam per square centimeter to 2.0 grams of clam per square centimeter. After an additional four and a half weeks of culture, byssal thread attachment among the smaller seed in the culture units was observed, resulting in lower survival and growth rates.
The seed clams were sorted to remove seed less than 3.0 mm in shell length. On day 73, three weeks after the removal of the small seed, the mean shell length increased from 3.6 to 4.4 mm. The growth rate tripled to 0.029 per day and survival rate improved to 88 percent.
Another sorting was conducted to separate the larger seed from the smaller seed. Due to declining ambient temperature inside the greenhouse, culture was terminated 10 days later. During the last 10 days of culture, the average growth rates of the two groups improved to 0.060 per day and survival rates were above 70 percent.

Results

The integrated control system performed dependably. It sampled and harvested the alga culture chambers as required, delivered the calculated volume of algal food, and purged the solids separator and backflushed the bead filter as directed. During the culture period, there were no valve, pump, or computer failures.
Part of the harvest strategy was to withdraw the maximum amount of usable algae from the system when the desired culture phase was attained. Consistent and reliable long-term algal production was primarily limited by ambient greenhouse conditions of variable light and temperature. Other significant culture constraints were bacteria and protozoan contamination, and biofilm build-up on the tank walls, particularly in the summer. Adjusted harvesting methods helped to reduce culture contamination and biofilm growth.
This culture procedure extended culture operation to approximately three weeks before tank cleanings and reinoculation with fresh alga cultures where necessary. The control program was modified to allow the removal of an algal culture tank from system operation for this process.
Increasing the flow to fluidization velocities in the upwellers, the seed densities were increased more than tenfold. However, for smaller seed (less than 3 mm shell length), the fluidized-flow conditions induced greater byssal thread attachment. The bysall thread attachment caused clumping of the seed mass, thereby affecting water flow, food distribution, and seed growth.
The clumping of the seed mass was minimized and cleaned of settled solids by air scouring the seed mass, which was more effective than hydraulically expanding the seed mass. A pulse feeding strategy was also incorporated to limit the food concentration to the seed, because a high feeding level can result in the production of pseudofeces and inefficient utilization of the feed.
When a 4 percent daily ration was provided and divided into four feedings per day, psuedofece production was not observed, and over 90 percent of the algal feed was cleared from suspension within the six-hour feeding time. The daily exchange of the system water volume was 40 to 160 percent of the seed clam system volume. This high water-exchange volume offset the need of the bead filter for ammonia removal and reduced alga losses by filter entrapment.
Conclusion
Automating the production of algae provides an alternative to the current manual batch culture method for alga culture and offers potential labor savings. The approximate total cost of this integrated system was $20,000. This cost included a laptop computer, software and all components for the water-treatment, alga-culture, clam-culture and computer-control units.
Greater use of algal products (pastes, dried algae) and computer control equipment (PLCs, single-board computers) could lower such costs and offer commercial facilities the benefits of optimized, automated feeding systems without the need of alga-production or water-treatment units.
(Editor’s Note: This article was originally published in the October 2001 print edition of the Global Aquaculture Advocate.)
Now that you've reached the end of the article ...
… please consider supporting GSA’s mission to advance responsible seafood practices through education, advocacy and third-party assurances. The Advocate aims to document the evolution of responsible seafood practices and share the expansive knowledge of our vast network of contributors.
By becoming a Global Seafood Alliance member, you’re ensuring that all of the pre-competitive work we do through member benefits, resources and events can continue. Individual membership costs just $50 a year.
Not a GSA member? Join us.
Authors
-
Timothy J. Pfeiffer, Ph.D.
USDA/ARS Aquaculture Systems Research Unit
1200 North University Drive
Mail Stop 4912
Pine Bluff, Arkansas 71601 USA -
Kelly A. Rusch, Ph.D.
Department of Civil and Environmental Engineering
Louisiana State University
Baton Rouge, Louisiana, USA
Tagged With
Related Posts
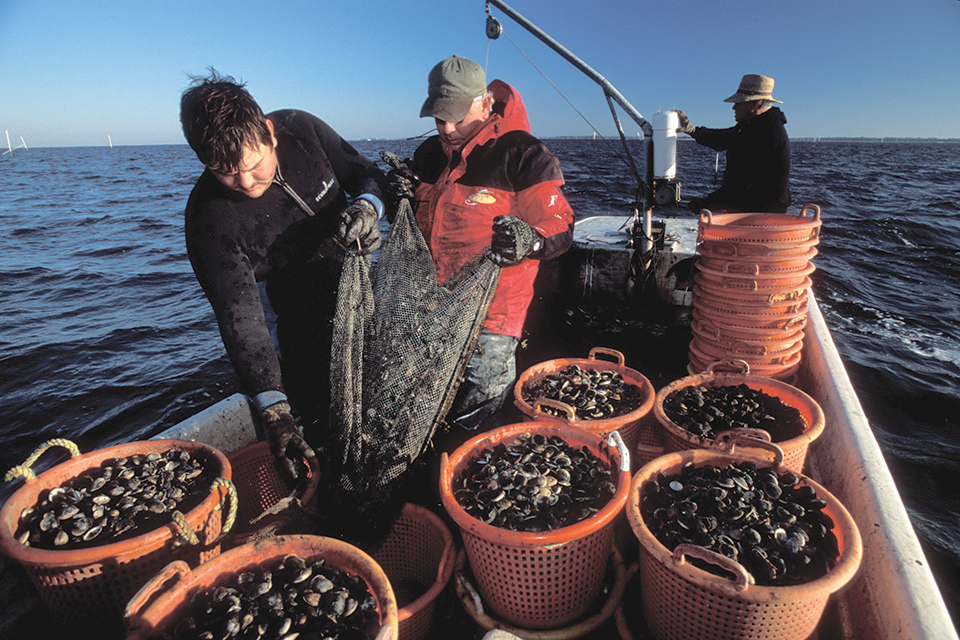
Intelligence
Research, extension efforts support hard clam industry in Florida
Breeding research is pursuing a hardier hard clam strain to improve survival during Florida’s hot summers. Diversification would support additional growth.
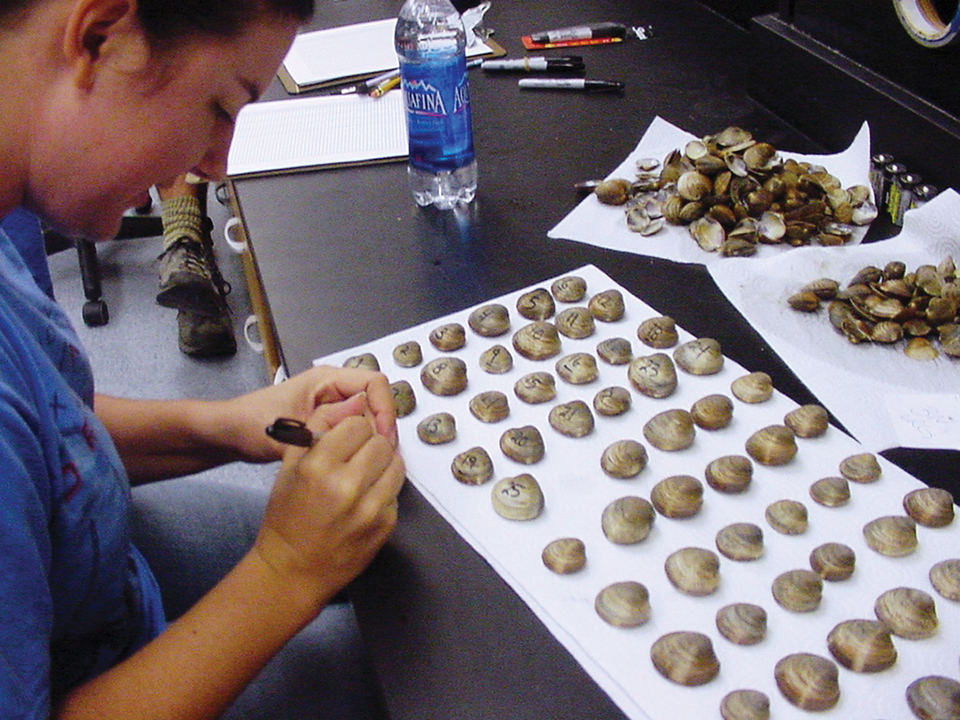
Health & Welfare
Triploid hard clams evaluated for Florida aquaculture
Induced triploidy could theoretically improve the survival of cultured hard clams because triploids divert energy from reproduction to somatic growth, resulting in larger and potentially hardier clams than diploids.
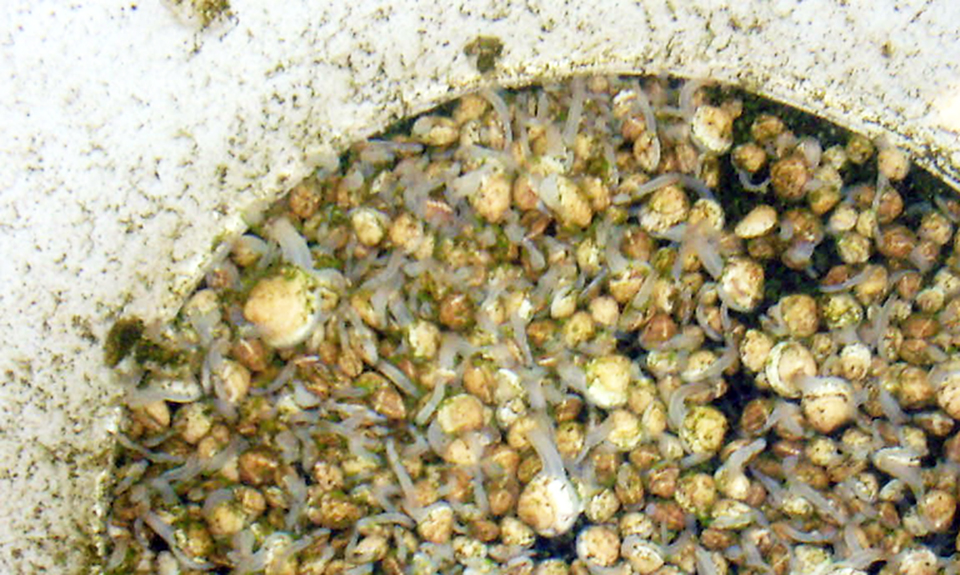
Intelligence
Researchers develop low-tech recirculating culture system for quahog clams
One shellfish species commonly raised in the northeastern United States is the quahog or hard clam (Mercenaria mercenaria).
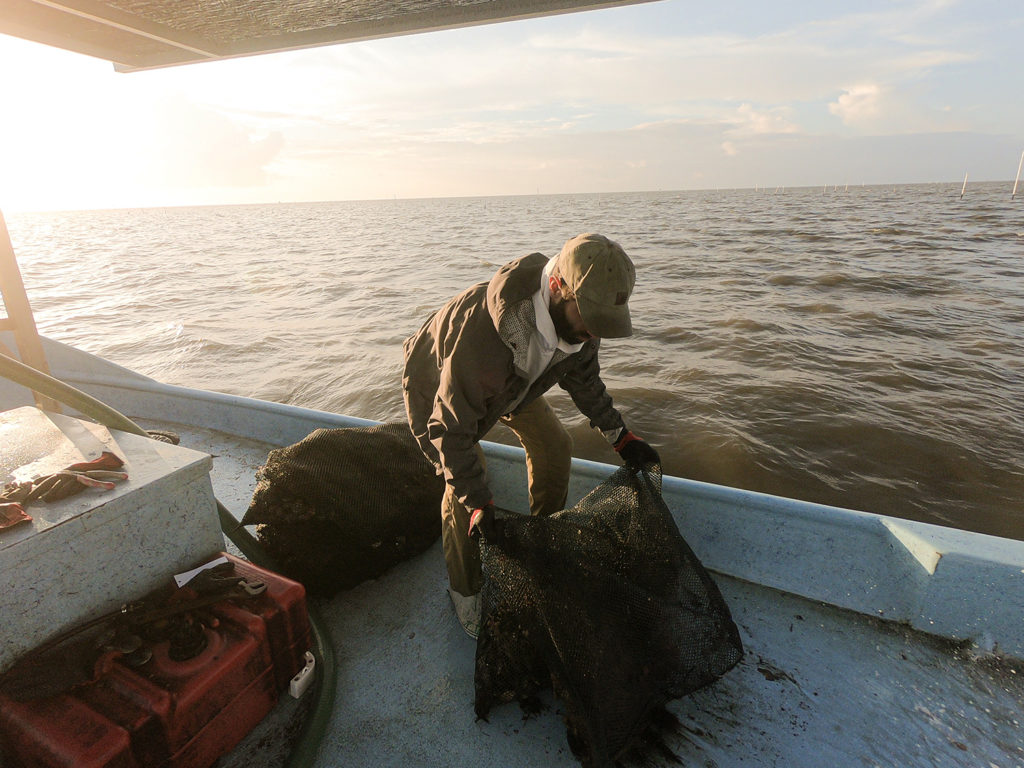
Intelligence
Farmers trade Kansas cornfields for Florida clam beds
The Stones came to Florida without experience in clams and no ties to the fishing community. Their backgrounds in farming, however, are proving valuable.