Extrusion can provide feeds for species that require higher levels of fat and/or floating characteristics

Growth in aquaculture production has sparked demands for increasing quantities of processed feeds, as well as a broad range of feed characteristics to accommodate the vast spectrum of species now cultivated. To meet these demands, the aquatic feed industry strives to target species’ nutritional requirements, meet farmers’ expectations for performance, satisfy environmental concerns, and process feed in a cost-effective manner.
The two major approaches to aquatic feed processing are pelleting and extrusion. Each method offers benefits and advantages.

Pelleted feeds
Advanced pelleting systems are capable of delivering durable, water-stable particles that increase feed efficiency. Pelleting also increases nutrient digestibility and reduces microbiological activity.
Many of these advantages are the result of heat treatment of ingredients, followed by pressing the mix into discrete particles. Treating feeds with moist heat not only improves pellet press performance, but also reduces microbial populations. Recognition of the importance of heat treatment has led to an explosion of technology in preconditioners, or “ripeners,” and post-pellet conditioners.
The use of expanders represents another attempt to improve the performance of pellet presses. Expanders, which deliver additional energy input to pelleting by increasing product temperature, have been added as an additional operation between steam preconditioners and pellet presses.
Extrusion cooking
The improved handling and performance of feeds brought about by additional processing also led to the application of extrusion in the feed industry. Low-moisture and dry extrusions have been utilized for many years. Although their applications are usually limited to the extrusion of dietary ingredients such as full-fat soy, extrusion of complete diets without a pellet press have also been employed.
Extrusion cookers and extruders have general similarities in design and function, but there are many not-so-subtle differences that have major effects on the characteristics of the end products. Extruders can be broadly classified as wet or dry, and single-screw or twin-screw.
Dry extrusion
Dry extrusion employs moisture levels below 18 percent, while wet extrusion processes material at higher moisture levels. Dry extruders do not utilize preconditioning. Therefore, they are limited in their ability to process a wide range of raw materials (Tables 1 and 2).
Rokey, Typical process parameters, Table 1
Process | Temperature (° C) | Max BBL Pressure Bar (Bar) | Moisture (%) | Maximum Fat (%) | Cook* (%) |
---|
Process | Temperature (° C) | Max BBL Pressure Bar (Bar) | Moisture (%) | Maximum Fat (%) | Cook* (%) |
---|---|---|---|---|---|
Pellet Press | 60-100 | – | 12-18 | 12 | 15-30 |
Expander/Pellet Press | 90-130 | 35-40 | 12-18 | 12 | 20-55 |
Dry Extrusion | 11-140 | 40-65 | 12-18 | 12** | 60-90 |
Wet Extrusion | |||||
Single Screw | 80-140 | 15-30 | 15-35 | 22 | 80-100 |
Twin Screw | 60-160 | 15-40 | 10-45 | 27 | 80-100 |
** Dry extrusion successfully processes full-fat soy (18-20% fat) and other ingredients where final product durability is not a concern.
Table 1. Typical process parameters.
Rokey, ypical production capacities and costs, Table 2
Process | Capacity Range (Ton/Hour) | Average Life/Major Wear Components (Hours) | Average Wear Cost ($/Ton) Complete Diet |
---|
Process | Capacity Range (Ton/Hour) | Average Life/Major Wear Components (Hours) | Average Wear Cost ($/Ton) Complete Diet |
---|---|---|---|
Pellet Press | 2-60 | 2,300 | 1.23 |
Expander/Pellet Press | 2-40 | 700* | 1.14 |
Dry Extrusion | 0.5-2 | 1000 | 1.78 |
Wet Extrusion | |||
Single Screw | 1-22 | 5000 | 0.90 |
Twin Screw | 1-14 | 5000 | 2.01 |
Table 2. Typical production capacities and costs.
The similarities between dry extruders and expanders are striking, and close examination of the principles involved and effects on final products reveal only subtle differences. Expanders are usually quoted at much higher capacities than dry extruders. This is made possible by putting less energy into the product per unit of throughput. This fact is reflected in the typical cook values of cereal grains processed through each system (Table 1). Extrusion cooking imparts more thorough processing of feeds compared to expanders or pellet mills (Table 1).
Wet extrusion
The physical components of wet extruders (both single and twin) are illustrated in Fig. 2. The mash to be extruded is fed from a holding bin, through a steam pre-conditioner, and into the extruder barrel. The pre-conditioner hydrates the mash to 18 to 25 percent moisture and simultaneously mixes and heats the mash to 80 to 95 degrees-C, at average retention times up to 2.5 minutes. This preconditioning phase, coupled with positive-conveyance screws in the extruder, effectively processes diets containing fat levels as high as 27 percent.
The extruder barrel houses a series of segmented screws and shear locks that convey and extrude the material through die orifices that control size and shape of the final pellet. Steam can be injected into the extruder barrel to reach processing conditions described in Table 1. Retention time in the extruder barrel can be as low as 15 seconds. This principle of high-temperature/short-time processing has made extrusion an effective process for individual ingredients and complete diets in feed manufacturing.
Five years ago, twin-screw wet extrusion was not common as a processing tool in the manufacturing of feeds. However, twin-screw extruders have become the process of choice when fat levels in recipes are above 17 percent, when fresh meats or other wet ingredients are added to recipes above the 35 percent level, or when the required pellet size is less than 1.5 mm in diameter. These extruders are also useful when ingredient flexibility is required.
Production vs. material costs
Early extrusion systems focused mainly on production of floating feeds, but more advanced systems are capable of delivering a complete range of expansion control. The greater process flexibility for extrusion as outlined in Table 4 is primarily due to the ability to impart more energy into the product.
Rokey, Table 4. Comparison of product characteristics, Table 4
Product Characteristics | Process Pelleting | Extrusion |
---|
Product Characteristics | Process Pelleting | Extrusion |
---|---|---|
Expansion Control | Negligible | Excellent |
Soft-Moist Diets | Difficult | Easy |
Control of Durability | Good | Excellent |
Product Size Less Than 1.6 mm | Not possible | Possible to o.3 mm |
Pasteurized Product | Good | Excellent |
Level of Starch Gelatinization | Low | High |
> 12% Fat Levels | Difficult | Easy |
Inactivation of Allergins, Growth Inhibitors | Poor | Excellent |
This increased flexibility is reflected in higher processing costs, as extrusion will generally require more than double the cost inputs per ton compared to pelleting. In compensation for this greater cost, extrusion offers the capability of utilizing lower levels of starch and supplemental binders and higher levels of fat and fiber. This can substantially reduce the raw-material cost of the diet.
Conclusion
Both pelleting and extrusion have found a niche in the manufacture of aquatic feeds. Pelleted feeds are largely confined to sinking aquatic feeds such as those for shrimp, trout, and others where the fat requirements are below 12 percent. Extrusion, on the other hand, can provide feeds for these species plus those that require higher levels of fat and/or floating characteristics.
(Editor’s Note: This article was originally published in the April 2001 print edition of the Global Aquaculture Advocate.)
Now that you've reached the end of the article ...
… please consider supporting GSA’s mission to advance responsible seafood practices through education, advocacy and third-party assurances. The Advocate aims to document the evolution of responsible seafood practices and share the expansive knowledge of our vast network of contributors.
By becoming a Global Seafood Alliance member, you’re ensuring that all of the pre-competitive work we do through member benefits, resources and events can continue. Individual membership costs just $50 a year.
Not a GSA member? Join us.
Author
Tagged With
Related Posts
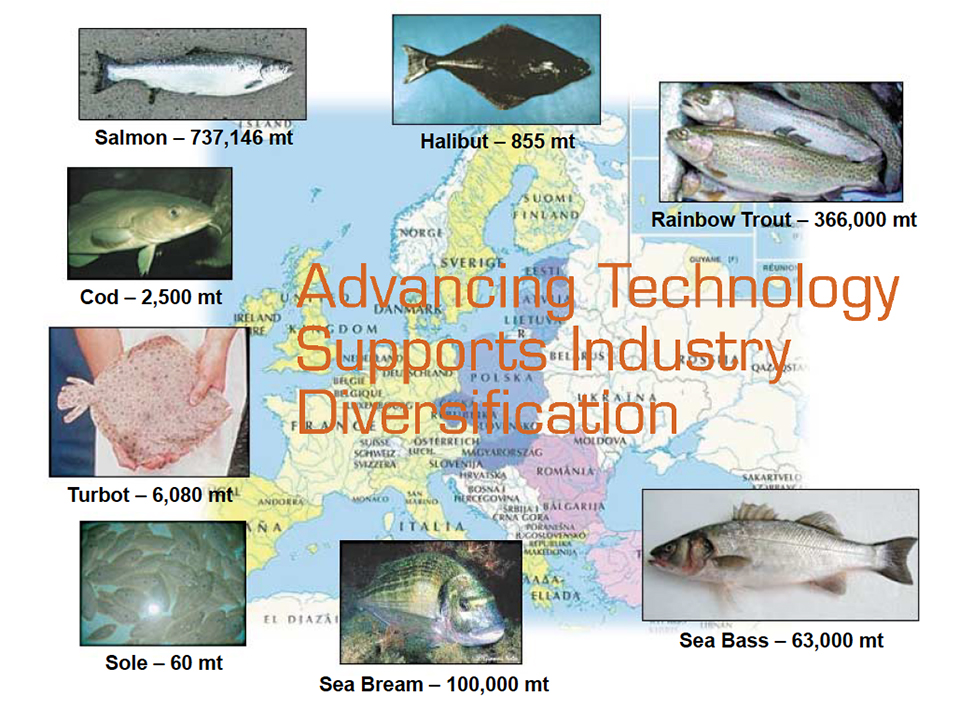
Intelligence
A review of European marine finfish hatcheries
As European aquaculture continues to diversify in the marine fish sector, technology advances and methodology in marine finfish hatcheries are proving vital.
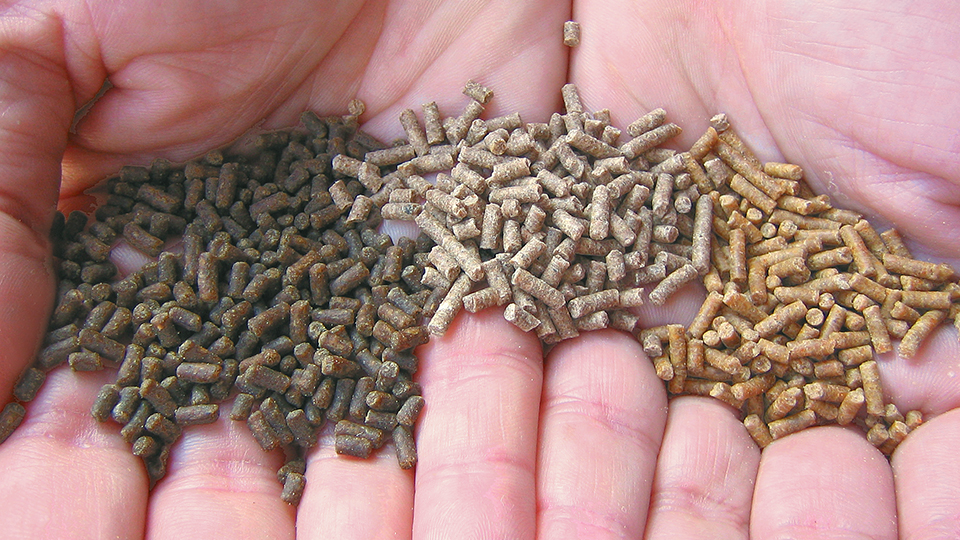
Aquafeeds
Extruded shrimp feeds reemerge
The process for making extruded shrimp feeds has flexibility to produce diets with a wide range of fat levels, densities, shapes and sizes.
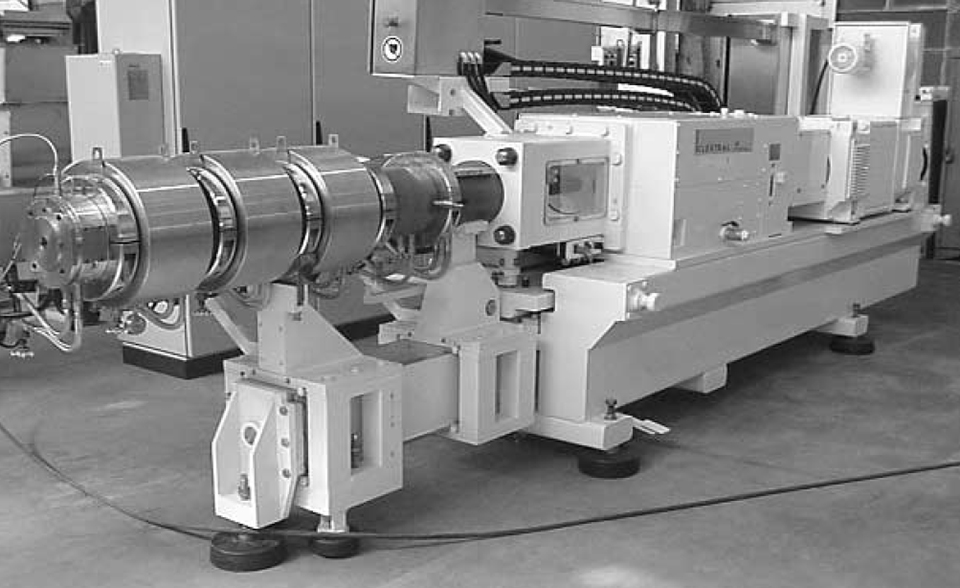
Aquafeeds
Extrusion processing of aquatic feeds, Part 1
Depending on the extrusion processing conditions and ingredients used, different products such as floating or sinking feed can be produced.
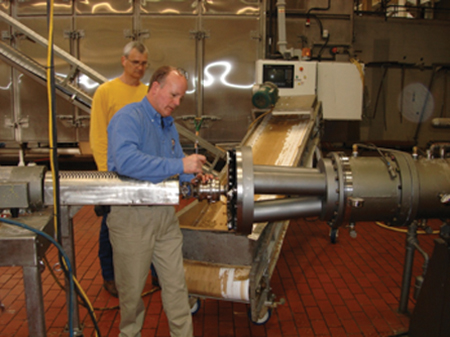
Health & Welfare
Extruder design changes increase production capacity for small-diameter feeds
The authors designed changes for single- and twin-screw extruders that streamlined the extrusion process to achieve higher output rates for small-diameter aquafeeds.