Survival for all treatments in the trial exceeded 90 percent

Extruders have been somewhat limited in terms of capacity when producing small-diameter floating or sinking aquatic feeds. Extruders require restriction or die hole number limitation for developing the back pressure and energy required for product expansion and the cooking effect for floating feeds. Extruders also require more holes or a greater open area for reduced expansion for sinking feeds.
In either case, extruders typically have a 60 to 70 percent reduction in capacity for small feed production. A standard 5- to 6-ton per hour extruder can produce 1 to 2 tons per hour of either floating or sinking small-diameter feeds or products less than 3 mm in diameter. The relationship is similar for larger-capacity extruders.
How can we achieve higher capacities on basically the same machines?
Preliminary considerations
A general plant review is needed before changes can be implemented to achieve higher extruder capacity. Does your mixing and grinding system achieve a good mix on finely ground raw materials? Is your grinding equipment designed to achieve a fine grind for small die openings at a significantly higher capacity? It is recommended that all particles be one-third in diameter or smaller than the final die opening.
When using a 1-mm final die opening, the raw material particles should be in the 300-µ−diameter range. Can your conveyors handle higher rates of small-diameter products? Generally, drying capacity is limiting, as dryers for small-diameter products are larger or require additional drying area. Sifting and dust control should also be evaluated.
Be aware of the potential changes required for the use of this technology to increase production rates to avoid moving the bottleneck to a different location.
Streamlining extrusion
The authors studied extrusion and streamlined the process in order to achieve higher rates for small-diameter feeds. This was accomplished and patented for both single- and twin-screw extruder designs.
The traditional cone screw was removed, and a divergent cone screw was placed on the single-screw extruder. The twin-screw model required some additional modifications, but basically was converted to a single-screw extruder at the critical point of the process, the end of the extruder barrel. This allowed the additional open area needed in both cases, as well as maintained the ratio of distance from the cone screw to the final die for expansion control on floating feed production.
These developments allowed final dies with increased hole population, which was needed for increased capacities. They also allowed elimination of flare-out dies, which did increase the hole numbers but also decreased evenness in overall pellet uniformity. The distance or length of flare-out die adapters results in less expansion in floating feeds.
The benefits of the new technology allow the final screw to be close to the die and increase hole population for floating feeds, which yields higher capacities, increased percentage of floating feeds and greater expansion.
Sinking feeds
Similar capacity problems existed when making small-diameter sinking feeds such as shrimp feeds. Knowing that aquatic feed producers generally make a range of products, a die to increase sinking feed capacity as well as density needed to be developed for use alone or in conjunction with the diverging-cone screw discussed above.
An oblique tube die was engineered and patented for increased sinking feed capacities for products at or under 3 mm in diameter. Densities have been averaging in the 650 grams/L range with this new technology, which allows three times the die hole population. The long tubes associated with this device increase cooking, decrease expansion, control pressure drop and increase retention time. The tubes’ internal design gives a uniform cross-sectional flow, and thus the pellets are very uniform.
Feeding trial
The question always remains after changing a feed production process whether the change adversely affects the growth rate of the animals to be fed. Feed was therefore produced and shipped to Texas A&M University in Port Aransas, Texas, USA, where the second author fed shrimp to verify their growth. The feed was a proven formula with reduced fishmeal content and increased vegetable proteins that was readily accepted by most white shrimp.
Pacific white shrimp (Litopenaeus vannamei) of 0.26 grams initial weight were stocked in 100 tanks at 5 shrimp/tank for a 35-day trial. The water was filtered and recirculated with salinity, temperature and dissolved oxygen checked daily. Ammonia, nitrite, nitrate and pH levels were measured weekly. The light regimen was 12 hours dark and 12 hours dim daily.
The shrimp were fed 15 times daily, and the unconsumed feed was removed daily. Water recirculation was 4,193 percent daily in this clean water system with no natural productivity at salinity levels between 25 and 37 ppt. The shrimp:area ratio was equal to 150 shrimp per cubic meter placed in water with a temperature range of 29 to 31 degrees-C and oxygen levels above 5 ppm. The pH was held between 8.0 and 8.2, and ammonia, nitrite and nitrate were at very acceptable low levels.
The percentage of survival for all treatments in the trial was over 90 percent. The linear growth phase was reached at week 4 and expected to continue at 1.7 grams/shrimp/week (Table 1). If this is extrapolated out, the final result would be about 30 shrimp/kg in 16 to 18 weeks.
Kearns, Estimated weekly shrimp growth, Table 1
Week | Weight (g) | Weight Change (g) |
---|
Week | Weight (g) | Weight Change (g) |
---|---|---|
0 | 0.26 | Initial |
1 | 0.65 | 0.39 |
2 | 1.30 | 0.65 |
3 | 2.60 | 1.60 |
4 | 4.30 | 1.70 |
5 | 6.00 | 1.70 |
Perspectives
Interest in the extrusion of shrimp feeds has mostly centered on the ability to modify the formula and achieve growth at a lower cost. This has been possible for years, for extruders can handle higher levels of vegetable proteins and lower levels of fishmeal, resulting in feed with good characteristics as well as lower cost and good shrimp growth rates.
Other additional points of interest include the fact that extruded shrimp feeds do not require binders other than the 10 to 15 percent starch normally included in feed formulas. Formulators can use least-cost formulation programs with lower restrictions.
Cleaner feed from the pasteurization effect of an extrusion cooker is achieved. There is less leaching in extruded feeds due to the binding effect of the extrusion process. Extrusion is famous for increased digestibility from cooking ingredients for most animals.
The main point, however, is economics. Make a quality feed with a lower cost with the same growth results. This can now be accomplished at high extrusion rates.

(Editor’s Note: This article was originally published in the May/June 2011 print edition of the Global Aquaculture Advocate.)
Now that you've reached the end of the article ...
… please consider supporting GSA’s mission to advance responsible seafood practices through education, advocacy and third-party assurances. The Advocate aims to document the evolution of responsible seafood practices and share the expansive knowledge of our vast network of contributors.
By becoming a Global Seafood Alliance member, you’re ensuring that all of the pre-competitive work we do through member benefits, resources and events can continue. Individual membership costs just $50 a year.
Not a GSA member? Join us.
Authors
-
Joseph P. Kearns
Aquaculture Process Engineering Manager
Wenger Manufacturing, Inc.
714 Main Street
Sabetha, Kansas 66534 USA -
Addison L. Lawrence, Ph.D.
Professor, Senior Faculty Fellow, Project Leader
Texas AgriLife Research Mariculture Laboratory
Texas A&M University System
Port Aransas, Texas, USA
Related Posts
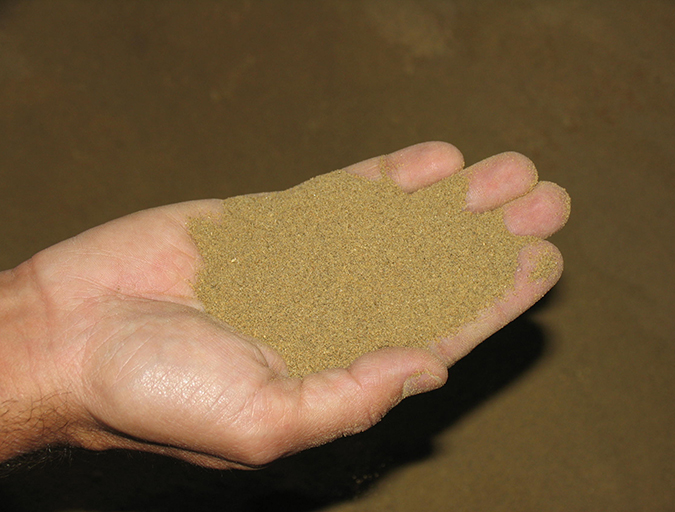
Aquafeeds
A look at the SME controlled extrusion process
A study was conducted using a Twin-Screw Extruder equipped with Specific Mechanical Energy (SME) and Density Control valves, to determine the effect of SME on the water stability of shrimp feeds. Further research is needed to evaluate the performance.
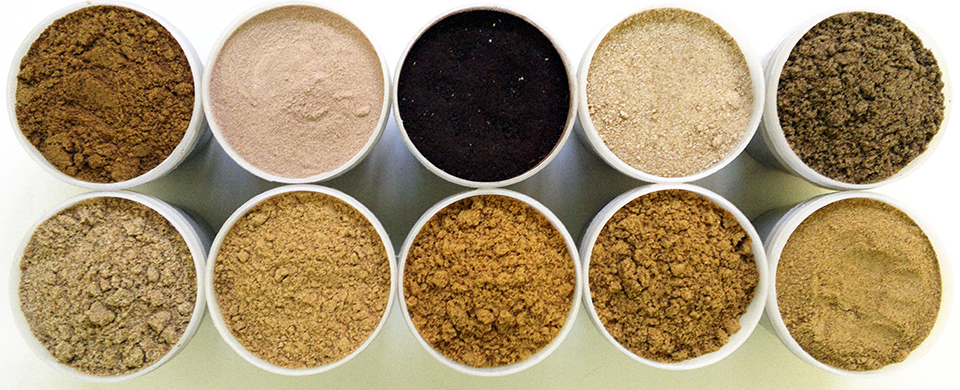
Aquafeeds
Animal protein meals reduce feed costs but don’t improve shrimp performance
The authors conducted a study to determine how replacement of salmon meal with various animal protein meals in feed affected the growth performance of white shrimp.
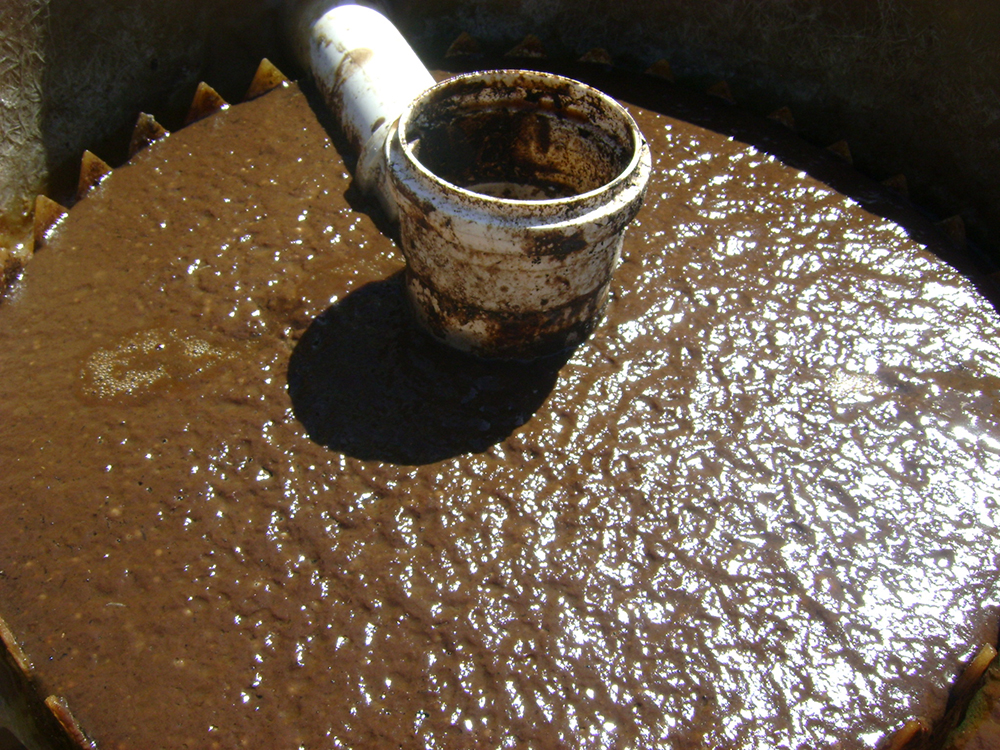
Aquafeeds
Crude protein and lipid from biofloc meals from an activated sludge system
A study compared the bioavailability of crude protein and lipid from biofloc meals generated with an activated sludge system using two water sources: wastewater from shrimp experimental culture (BFL-W) and, artificially, using clean seawater (BFL-C).
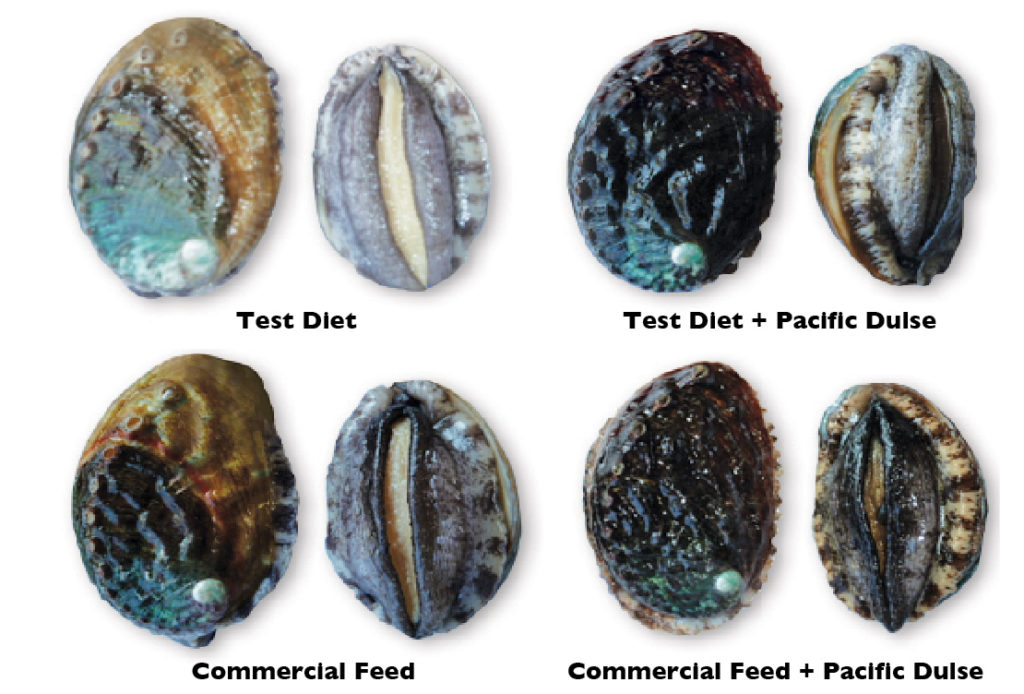
Health & Welfare
Diets affect abalone meat quality, shell color
A preliminary study investigated the effects of diet on the meat quality and shell color of Pacific abalone. A test diet and a commercial abalone feed resulted in lower meat protein content compared to that achieved with a diet of Pacific dulse seaweed. The artificial diets also caused the abalone to have yellow or orange shells. The seaweed diet alone resulted in abalone with dark-brown shells. However, a combination of seaweed and either artificial diet improved abalone growth, meat quality and shell color.