More environmentally friendly packaging could help tackle the seafood industry’s polystyrene problem, say innovators

When it comes to ocean health, marine pollution is a hot topic. Concern is growing among scientists and citizens alike about the pervasiveness of microplastics (small pieces of plastic less than 5 millimeters in size) as well as the harmful impact of ghost gear (abandoned, lost or discarded fishing gear). Most recently, the UN Ocean Conference opened with an urgent call to action to address the “ocean emergency,” which included dealing with plastic pollution “choking” the seas.
A major source of marine plastics is expanded polystyrene – a type of plastic that when puffed with air is lightweight, buoyant, water-resistant and an excellent insulator. For these reasons, expanded polystyrene (also known as foamed polystyrene, EPS or “Styrofoam”) is a popular choice for the seafood industry, often used by fisheries and aquaculture operations for buoys, food packaging (e.g., fish boxes or cool boxes), the interior of pontoons and marina platforms and more.
But these advantages come at a steep cost. While EPS can hold a rigid shape, it’s not very durable and easily crumbles into smaller pieces. Because of its lightweight, popularity and potential to break down, it’s a common form of plastic pollution in the ocean and other bodies of water.
“The problem is extremely widespread,” said Annkathrin Sharp, program officer at Fauna and Flora International, the world’s oldest international wildlife conservation organization. “[Although] we were not able to find statistics on polystyrene packaging specifically, foamed polystyrene (from all sources) has been widely recorded as a common component of marine litter, including pieces that have found their way to the Arctic Ocean.”
Disintegrating into thousands of puffed fragments, research suggests that foamed polystyrene pollution in the ocean threatens marine life and human health, leading select U.S. states and countries to restrict or ban its use.
In taking stock of the issue, some innovators are thinking outside the EPS box and developing more sustainable packaging for the seafood industry. Could such alternatives help tackle the seafood industry’s polystyrene problem?
‘A waste nightmare’
Expanded polystyrene wasn’t always the bad guy. First discovered in 1839, EPS took off during World War II as an inexpensive building material for military aircraft and catapulted into widespread use for everything from energy-efficient building insulation to soilless hydroponic gardening.
“For many years, EPS was considered a ‘wonder product’ due to its low-cost, lightweight and good insulation performance,” explained Peter Meredith, VP-Americas at FoodCap International, a global food technology and product development company that focuses on circular packaging systems. “That has changed, and it is increasingly recognized as a waste nightmare.”
As Meredith explains, EPS is essentially non-biodegradable, taking hundreds of years to decompose and consuming “vast space” in landfills. While EPS degrades in seawater, it does not biodegrade – it just breaks down for marine life and eventually seeps into the food chain. EPS also contains the toxic substances, Styrene and Benzene, and the beads of polystyrene produced by suspension polymerization are tiny and hard.
“To make them expand, special blowing agents are used, including propane, pentane, methylene chloride and the chlorofluorocarbons,” said Meredith. “Toxic micro pieces can break down in oceans, potentially contaminating the marine food chain, and ultimately, the human diet.”
Nonetheless, EPS remains the go-to packaging for transporting seafood, used for both packaging and insulation purposes. But EPS packaging generates a significant environmental burden through its production, use and disposal and its single-use also feeds into the plastic pollution problem.
“Once in the marine environment, foamed polystyrene fragments can persist for decades, if not hundreds of years, where they present a chemical and physical risk to marine species,” said Sharp. “Foamed polystyrene is a particular threat because of its propensity to rapidly fragment into microplastic pollution, and microplastics are a disproportionately serious problem: firstly, because of their ability to be eaten by almost all marine species; and secondly, due to their high surface area to volume ratio, enabling them to collect high amounts of toxic chemicals.”
While EPS is technically recyclable, Sharp says this “very rarely” happens due to its high volume-to-weight ratio – meaning that without first being crushed, it takes up a lot of space. That reality creates challenges for the seafood industry.
“Transporting it to recycling centers isn’t economically viable when one factors in fuel and other freight costs – particularly given the low value of foamed polystyrene itself,” said Sharp. “It’s also because once foamed polystyrene has been contaminated with residues and fluids from the seafood itself, mechanical recycling is a less attractive option, and chemical recycling is not yet viable at scale.”
For these reasons, reusing or recycling the fish boxes, used to transport fish prior to packaging for supermarket sale or to deliver directly to markets or restaurants, is not widespread. Sharp said that one estimate puts the percentage of fish boxes in Europe that end up in landfill at 45 to 50 percent.
Many seafood processors and processors are aware that fish packaging needs to become more sustainable, with Salmon Scotland holding a panel discussion on the issue during COP26. The organization’s sustainability charter also commits the sector to “work towards using 100 percent reusable, recyclable or biodegradable packaging.” Aside from the hurdles with recycling, the industry is aware that consumers are increasingly demanding change.
“If you turn back the clock 10 years ago, consumers were a bit aware of packaging, but nothing like they are in the last five years,” said Meredith. “Now, consumers know it’s a product that very heavily ends up in landfill and typically is single use in the commercial environment. People are making purchase decisions based on the packaging that they see at a retail level.”
With consumer “plastic panic” spreading and trending on social and mainstream media, Meredith says many supermarket groups around the world are setting deadlines on their seafood processors and producers to eliminate EPS from the supply chains.
“Progress has been glacial, as many seafood processors have resisted change, but this no longer fits today’s CSR objectives and target,” said Meredith. “Innovative supermarket groups are looking to be sustainability leaders, not followers that wait until legislation forces change.”
Venturing outside the EPS box
With growing consumer concern about sustainability, FoodCap has taken on the challenge and developed FishCap – a reusable replacement for the EPS fish box, designed for storage and transportation of fish and seafood products between harvest and further processing. At the end of their use life, Meredith estimates that 10,000 FishCap containers could eliminate up to 1 million single-use EPS fish boxes.
“FishCap is the first commercial solution that offers all of the advantages of EPS without the negative handling and environmental outcomes,” said Meredith. “Every time you reuse a FishCap [box], it is one less new Styrofoam container that doesn’t need to be produced.”
The boxes are made from a highly durable “cradle-to-cradle” technical material, a proprietary resin that can effectively remain in a continuous closed-loop system of production, reuse, recycling, reproduction and subsequent reuse.
“FishCap resin is chemically inert and unaffected by most organic solvents as well as blood, protein or fat,” said Meredith. “It has outstanding shock absorption and compression resistance – it can withstand multiple impact strikes to reduce product contents damage-in-transit. FishCap is designed to fit existing systems and infrastructure in processing plants and transfer.”
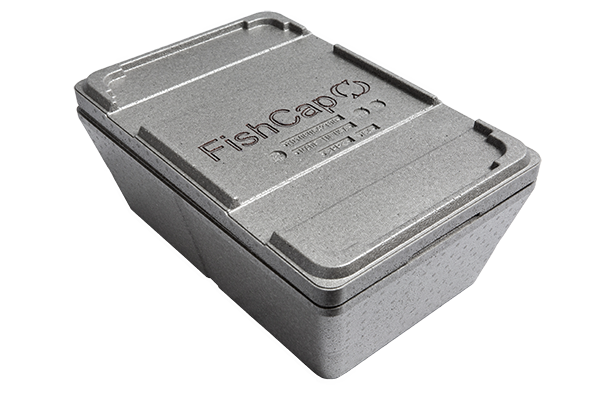
How it works: FishCap capsules are supplied to a seafood harvest facility for packing. Chilled whole fish or fillets are packed into the boxes and industry-standard conveying transfers the FishCaps for manual or automated palletizing. Each box locks securely when cross-stacked, and then, they’re dispatched to further processing.
“After arrival at a further processing facility, FishCaps can be stored in a chiller or transferred directly to a processing line,” said Meredith. “Once emptied, FishCaps are moved to an on-site or off-site cleaning facility where they are washed, sanitized and dried prior to palletizing for reverse logistics and reuse.”
In terms of other advantages, FishCap is lightweight, has high thermal insulation, and is fully recyclable with end-of-cycle product applications. Because of its high strength, durability and impact resistance, it eliminates the box breakage that’s common during EPS transport of seafood between harvest and further processing.
“FishCap is crumble-resistant to minimize potential microplastics pollution,” said Meredith. “It has a low environmental impact from the manufacturing process, including production without the use of toxic chemicals used in EPS production.”
With EPS boxes reportedly doubling in price over the last 12 to 18 months, Meredith said the economics of the reusable FishCap handling solution is becoming more attractive. FishCaps are typically leased on a monthly or usage basis, with the company looking at each organization and figuring out the logistics for operating in the most efficient manner.
“We review how long it takes to complete a full loop from loading to being available for reload,” explained Meredith. “And then we take care of how many FishCaps we need in the loop to make it work.”
For instance, it may not be logical to air freight empty FishCaps back to Chile for reuse; instead, it may make more sense to have a larger fleet of FishCaps to support a longer sea freight return logistics model. However, if it was a circular reusable cycle allowing the use of road freight, Meredith said that the number of FishCaps required in the cycle could be “considerably less.” As a result, the FishCap pricing model is largely based on a per-use basis.
“It really comes down to how many are actually required in the loop,” said Meredith. “To give you an example, South America to the U.S. is around $2 per use.”
In the best-case scenario, Meredith said that goal is for FishCap to be “less than using Styrofoam,” and at worse, for it be cost neutral. However, the current situation presents some hurdles to getting there.
“Because of the way freight prices are at the moment, we’re close [to neutrality], but not quite there,” said Meredith.
‘An excellent step forward’
Despite technological advances, finding a practical EPS alternative that can meet acceptable quality and food safety standards isn’t simple. Still, many innovators are still game to give it a go.
At COP26, independent producer Organic Sea Harvest showcased its plastic-free, compostable biomaterial packaging, called CF422. The material is made from vegetable oils and esters purpose-grown and sourced in the European Union, and calcium carbonate, which adds minerals to the soil when the material is composted.
The company said that the compostable packaging contains less than half the amount of CO2 in normal packaging, reduces the need for energy at the packing stage and eliminates the issue of microplastics, while still ensuring food safety and storage time.
Likewise, Mondi, a multinational packaging and paper group, is developing an alternative insulating box using paper fibers and starch. Called the Mondi FishBox, it consists of a hot-melt closing bottom tray and a top tray, and the packaging solution creates an “optimal barrier against grease and moisture while maintaining its structural integrity.”
“The construction is leak-proof, fast to fold and designed for cold chain shipping,” said Dawid Pilcek, Managing Director at Mondi Corrugated Swiecie. “It is available with either a brown or white top surface, and a transparent or metalized barrier on the inside, in silver, gold or other colors.”
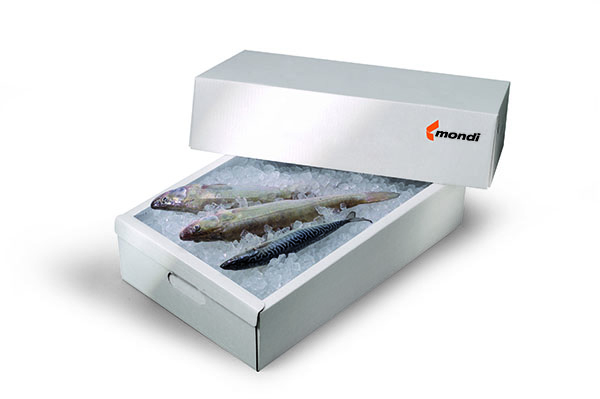
Currently, Mondi is in the final testing phase with a Scottish company and is in contact with customers in Norway and Iceland. Aside from the environmental benefits, Pilcek said that customers will experience cost-efficiency when it comes to transportation and storage, as well as a less expensive recycling process. For producers using manual production lines, the product can also be implemented without any additional investment in equipment.
“Paper-based packaging is made from a renewable resource and is fully recyclable,” said Pilcek. “Mondi’s FishBox can be sent to the producer in a flat format, which means less air is shipped and more boxes can fit in trucks thereby minimizing the fleet and lowering CO2 emissions in transportation. Less space is also needed when it comes to storing the boxes in warehouses.”
Another cost-cutting benefit: Starting January 2023, the European Union will introduce Extended Producer Responsibility, which includes an additional fee that varies based on the weight and type of material of the packaging used. Paper-based solutions generate lower fees, while fees for plastic packaging, such as polystyrene, will be highest.
“With more and more export destinations introducing taxes on polystyrene or choosing to ban it entirely, we are here to help our customers innovate,” said Pilcek.
While technology isn’t going to solve the large-scale problem of ocean pollution, Sharp said alternative packaging solutions like FishCap are an “excellent step forward.”
“We encourage any innovations that reduce the amount of foamed polystyrene (or plastic packaging of any kind) being produced and discarded after few (or single) uses,” said Sharp. “The further a capsule’s useful life could be extended, the better, as with every time it is returned and re-used, the demand for another foamed polystyrene box is avoided.”
Follow the Advocate on Twitter @GSA_Advocate
Now that you've reached the end of the article ...
… please consider supporting GSA’s mission to advance responsible seafood practices through education, advocacy and third-party assurances. The Advocate aims to document the evolution of responsible seafood practices and share the expansive knowledge of our vast network of contributors.
By becoming a Global Seafood Alliance member, you’re ensuring that all of the pre-competitive work we do through member benefits, resources and events can continue. Individual membership costs just $50 a year.
Not a GSA member? Join us.
Author
-
Lisa Jackson
Associate Editor Lisa Jackson lives in Hamilton, Ontario, Canada. Her work has been featured in Al Jazeera News, The Globe & Mail, The Independent, and The Toronto Star.
Tagged With
Related Posts
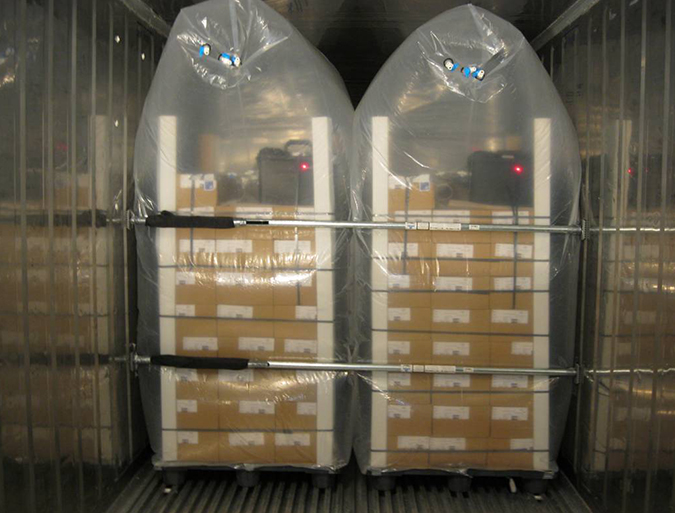
Responsibility
Slow fish: Preventing waste via packaging
BluWrap shipping technology can cut the seafood industry's abysmal food-waste statistics by dramatically extending the shelf life of fresh product. Company CEO Mark Barnekow's mission is to get fresh fish off airplanes and onto ocean-bound cargo ships.
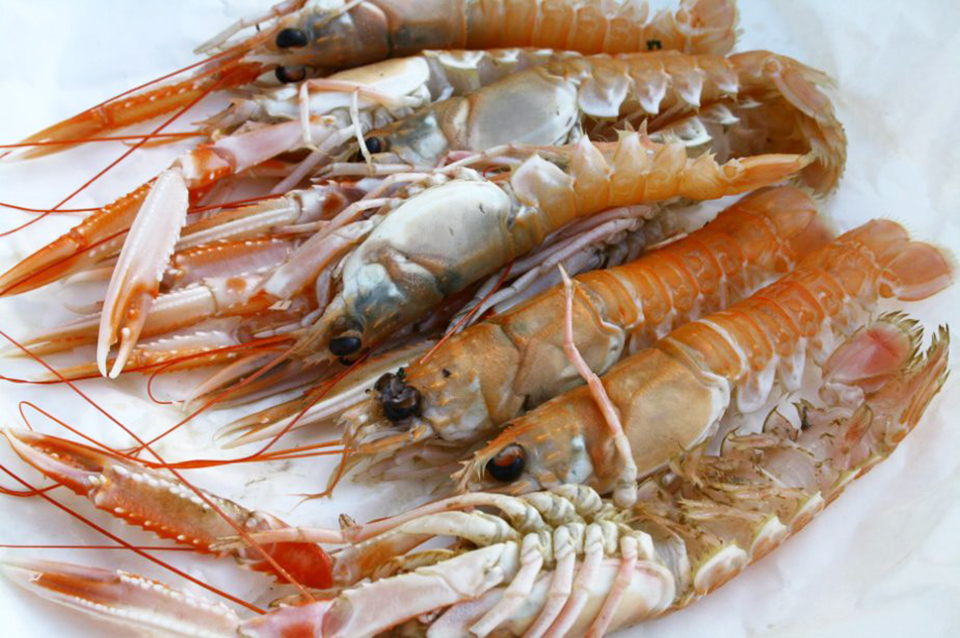
Innovation & Investment
Plastic 2.Ocean: Seafood packaging, made from shellfish
A new type of chitosan-based bioplastic, made from shellfish shells, emerges as a potential solution for global food waste and marine plastic pollution.
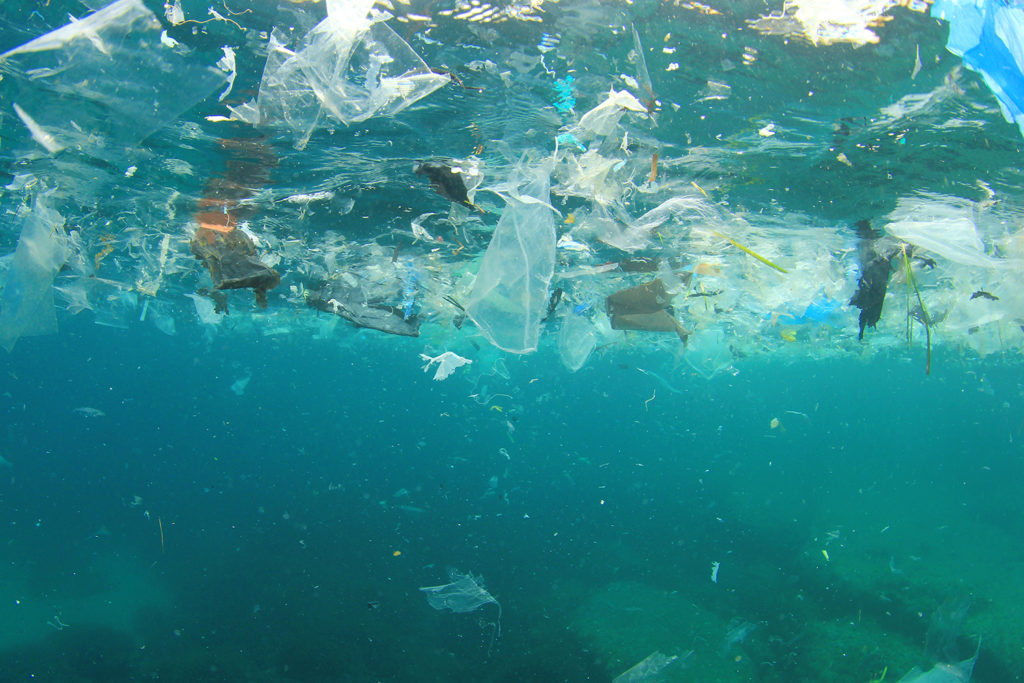
Responsibility
What threat do microplastics, a.k.a. ‘ocean hitchhikers’, pose to aquaculture?
A Trends in Microbiology paper posits that ocean microplastics could be a vector for pathogens, spreading antimicrobial-resistant genes.
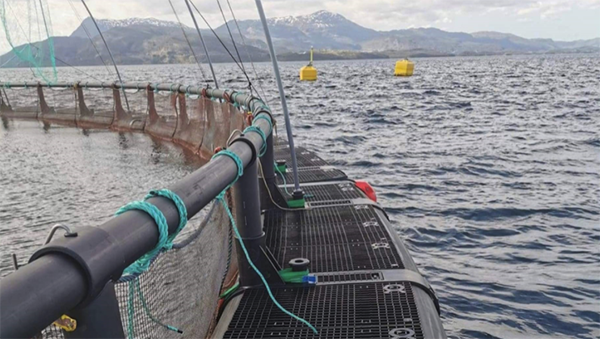
Innovation & Investment
AKVA develops ocean net pens without polystyrene
Aquaculture equipment manufacturer AKVA Group says its new ocean net pens are free of polystyrene, a plastic foam common in consumer packaging.