Enhancements for land-based aquaculture systems

Currently, just over a dozen commercial facilities use land-based, closed-containment systems to produce primarily food-size Atlantic salmon, as well as steelhead and coho salmon. The largest of these farms are located in Canada, Denmark, Poland and China. The ‘Namgis First Nation’s Kuterra salmon farm in Canada and the Langsand Laks and Danish Salmon facilities in Denmark are frequently highlighted in the trade press.
When all of these facilities reach full production levels, their estimated total production potential will approach 7,000 mt annually. In addition, another dozen facilities are being built or planned around the world, including additional production in the United States and Scotland. These additional projects, which would potentially produce more than 10,000 mt of food-size salmon, are bringing new principles into the salmon industry.
It is obvious that confidence in recirculating aquaculture system (RAS) technologies has risen. Private investment in land-based closed-containment fish farms is growing, and projects with fixed capital investments of U.S. $1.5 million to $30.0 million are the general trend, but some larger projects are being discussed. The technical and biological viability of these operations has been demonstrated, while their economic success, considered viable through theoretical modeling, is now being assessed in practice.
Rising quality, performance
Regulations established in Norway and other areas are combining with performance criteria developed by owners to ensure that newly constructed systems maintain reliable production and excellent water quality and fish health. In addition, the rising availability of RAS to smolt and post-smolt producers around the globe, particularly in Norway, has increased the number of large production systems delivered and provided opportunities to make improvements with each successive generation.
Finishing systems
Salmonids and many other fish must be “finished” or depurated for four to 14 days to remove earthy flavors that can potentially accumulate in the fish when grown in RAS. In particular, most farmers producing rainbow trout, coho salmon, Atlantic salmon and Arctic char in RAS are paying close attention to their purge system designs and standard operating practices.
The goal of purging designs, which typically incorporate partial water reuse without a biofilter, is to ensure that depuration systems can be maintained relatively cleanly and kept free from biofilms in order to maximize the removal of earthy and musty flavors.
Gas balancing
An emerging trend to increase production efficiency and reduce operating costs has been to apply technologies that increase the available oxygen provided to the fish while simultaneously improving carbon dioxide (C.O.2) removal. Increasing oxygen to the fish must be accomplished without creating total gas pressure super-saturation.
Using oxygen transfer technology that treats the full flow at low pressures without side-stream oxygenation has been widely applied across North America and in some other locations to create oxygen super-saturation while venting nitrogen off-gas to the atmosphere and reducing the opportunity for total gas pressure super-saturation. With the increased use of pure oxygenation to increase carrying capacity, carbon dioxide has become a larger challenge in RAS.
Improving carbon dioxide removal has required increasing culture tank exchange rates and treating large flows with a combination of centralized aeration and distributed treatment technologies. Distributed C.O.2-stripping technologies can include cascade aeration as water exits the sidewall drain of a culture tank, large traditional airlift pumps or vacuum airlift pumps located adjacent to the culture tank.
Even in-tank stripping systems can be used if they do not degrade culture tank hydrodynamics and impact solids removal. The increased tank turnover rate and water treatment technology that must be applied typically increase both fixed and variable costs for production, but the improved C.O.2 control is critical.
Pollution mitigation

Industry expansion in some locations also hinges upon the development of pollution-mitigating technologies to reduce nutrients in effluents. Large farms must typically capture and reclaim waste biosolids. Substantial improvements have been made in dewatering and drying biosolids into a thick slurry or cake that can be readily used elsewhere.
In addition, more cost-effective technologies, like woodchip bioreactors, are being applied to remove nitrate from RAS effluents. Advanced denitrification technologies such as membrane biological reactors (MBR) are being fine-tuned for use within RAS to eliminate water-flushing requirements and waste discharges, while reclaiming the water, heat, salinity and alkalinity that would otherwise be lost in the effluent.
Perspectives
Closed-containment systems are making major strides in the salmonid industry. They have a small footprint, requiring less than 1 percent of the land required by pond culture in warmwater applications, and less than 1 percent of the water required by flow-through salmonid culture, while capturing and controlling wastes.
Increased economies of scale and improved water recirculation technologies have improved RAS economics. RAS have the potential to produce the best survival and most efficient feed conversion. In addition, they provide significant barriers that prevent escapes and interactions with wild populations.
And finally – location, location, location – these farms can be built almost anywhere that makes economic sense to provide local, fresh seafood or leverage less-expensive power, feed, labor and other cost considerations.
(Editor’s Note: This article was originally published in the May/June 2015 print edition of the Global Aquaculture Advocate.)
Now that you've reached the end of the article ...
… please consider supporting GSA’s mission to advance responsible seafood practices through education, advocacy and third-party assurances. The Advocate aims to document the evolution of responsible seafood practices and share the expansive knowledge of our vast network of contributors.
By becoming a Global Seafood Alliance member, you’re ensuring that all of the pre-competitive work we do through member benefits, resources and events can continue. Individual membership costs just $50 a year.
Not a GSA member? Join us.
Authors
-
Steven Summerfelt, Ph.D.
The Conservation Fund Freshwater Institute
1098 Turner Road
Shepherdstown, West Virginia 25443-4228 USA -
John Davidson, M.S.
The Conservation Fund Freshwater Institute
-
Travis May
The Conservation Fund Freshwater Institute
-
Christopher Good, DVM, Ph.D.
The Conservation Fund Freshwater Institute
-
Brian Vinci, Ph.D.
The Conservation Fund Freshwater Institute
Tagged With
Related Posts
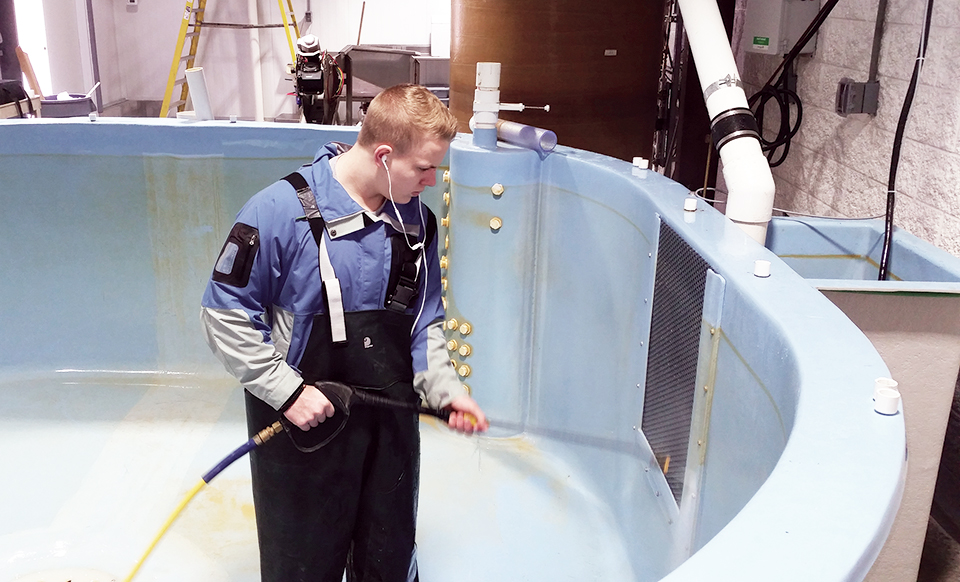
Health & Welfare
Emerging trends in salmonid RAS, part 1
The benefits realized by recirculating aquaculture systems – including enhanced fish growth, product quality and survival, as well as reduced treatment costs – have made the RAS approach an important production trend.
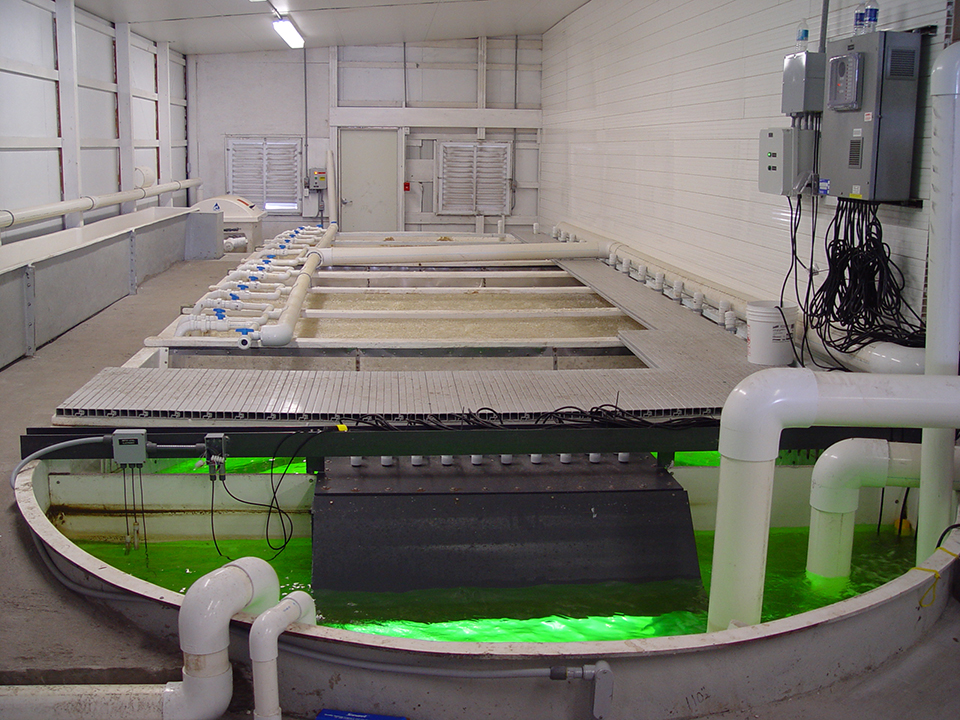
Innovation & Investment
Flow rate estimation for RAS
The water quality in recirculating aquaculture systems is generally a function of the tank size, biomass, feed inputs and waste treatment efficiency. Adequate biofiltration can control the build-up of ammonia-nitrogen and nitrate-nitrogen in the systems.
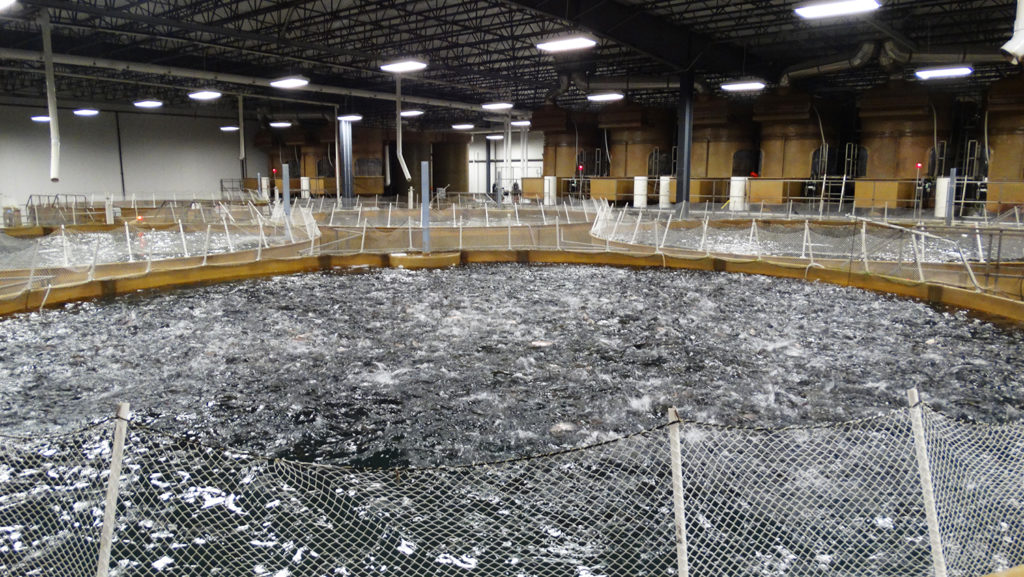
Innovation & Investment
AquaBounty, with new RAS facility, hopes to win public support for GM salmon
Ron Stotish, CEO of AquaBounty Technologies, believes genetically modified salmon is no threat to its opponents and the outlook for AquAdvantage is good. With its purchase of the Bell Fish Co. RAS facility, commercialization will soon commence.
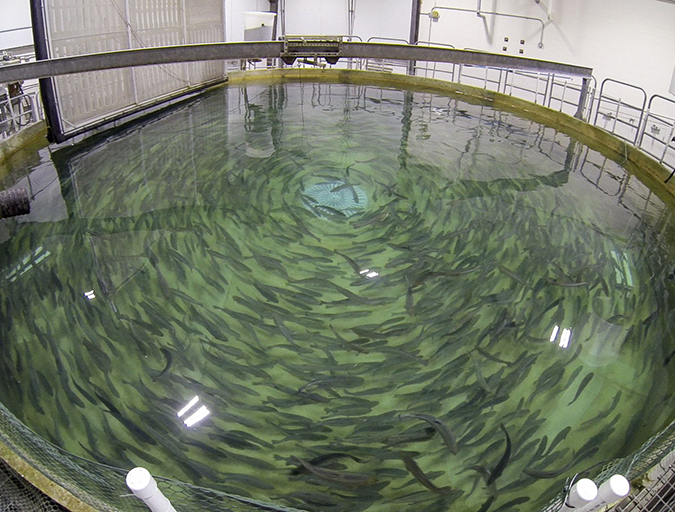
Innovation & Investment
Getting proficient in RAS fundamentals
A number of large salmon farming companies are now investing significantly to increase land-based, water recirculating aquaculture systems (RAS) in northern Europe and North America, and there is likely a need for more trained farm personnel to run and manage these and other close-containment aquaculture facilities.