Reduction of artemia cyst consumption an ongoing effort

An Eastern proverb says “Experience is a comb that nature gives to men when they are bald.” Indeed, technology seems to change so fast that many of our experiences may not seem to have much application in today’s world.
However, the accumulated bits of knowledge that we have gained through experience are like stepping stones that allow us to advance to higher levels. As we enter this new millennium, I would like to reminisce about the status of shrimp larviculture when I began in 1975 as compared to the technology of using liquid larval diets today.
Early shrimp larviculture production and diets
I began my larviculture career in 1975 at Marifarms, Inc. (Panama City, Florida USA), where I was trained in the use of a modified “Japanese Method.” Marifarms required large quantities of postlarvae to stock grow-out ponds of 112 and 150 ha each and a netted bay enclosure of approximately 800 ha. The production cycle for Marifarms was seasonal, because temperature limitations allowed only one cycle per year. Consequently, the hatchery operated only from March through June of each year.
The Marifarms method stocked low densities (usually 20 to 40 nauplii per liter) and harvested about 10 to 20 PL10-15 per liter. On the positive side, the system was very forgiving. It produced good quality postlarvae with low labor input in comparison to work requirements prevalent at many laboratories today. However, it required lots of everything else, including algae, artemia, water, and mated wild broodstock.
The Marifarms larviculture system consisted of four larval rearing complexes and ancillary facilities supervised by a biologist/manager. Each complex was comprised of eight 120-metric ton, square, flat-bottomed concrete tanks. Between 1974-75, eight 25-ton fiberglass tanks were added to each complex to split the larval culture cycle into two phases (nauplius to PL1 and PL1 to PL15) to increase production. Each complex was operated by one la viculture technician and a part-time laborer.
Marifarms utilized naturally-mated broodstock of three different species (Penaeus setiferus, P. aztecus and P. duorarum). Availability of broodstock varied from year to year, as did the salinity and temperature of the bay. Within a given year, broodstock of the three species matured at different times of the year, according to their natural reproductive cycles. P. setiferus was the dominant species used, and was the most productive in the hatchery and grow-out systems.
The productivity of the Marifarms hatchery varied from year to year, probably because it was very similar to a natural system. During the 2-3 month spawning season of P. setiferus, the hatchery would produce 200 to 300 million PL for stocking the grow-out systems. This amounted to around 100 million PL per month, which compares favorably to some of today’s production facilities.
As stated earlier, this larviculture system was very forgiving, and the methodology was more “art” than science. Tank preparation consisted of several steps, including: washing down the concrete or fiberglass tanks with a chlorine solution, filling with sand-filtered seawater, and checking temperature and salinity. If needed, salinity was adjusted with rock salt, and temperature was raised using electrical immersion heaters.
Naturally mated broodstock were collected from contract fishing boats and placed in net cages within the larviculture tanks. They were allowed to spawn for one to two days, depending upon the species. After spawning, broodstock were removed and samples of eggs or nauplii were collected from each tank. Then, the tanks were fertilized with sodium nitrate, potassium phosphate, and sodium silicate. Adjustments of the timing and quantities of fertilizers, and the decision on whether or not to inoculate algae from adjacent tanks, were parts of this fine “art” of larviculture.
Microalgal densities were not monitored using a microscope, because with experience one could get a feel for “good” algal levels based on the coloration and turbidity of the fertilized tank water. We were very lucky at this site, since Skeletonema sp., a chain diatom that is an excellent feed for larval shrimp, would bloom each time a tank was fertilized. The diatom bloom would normally last from 5-7 days (could be prolonged by additional fertilization and dilution), usually long enough for the larvae to reach the late mysis stage, at which time live artemia nauplii could be added to the tank. At the post-larval stage, a “high protein” pond pellet, which had been ground and sieved to an appropriate size, would be used to supplement the diet of microalgae and artemia.
Artificial larval diets (microparticles) were relatively rare during the 1970s and up to the early 1980s, and even the “Galveston Method,” a “high tech” system at the time, was based on the use of algae and artemia for larval rearing. The larviculture methods during this period were heavy consumers of artemia, with ranges of 10 to 20 kg of cysts per million PL produced. Artemia consumption varied widely, because of cyst quality, hatching technology and feeding method.
In the early to late 1970s, nauplii were available only from wild-mated broodstock. Nauplii production was variable, because all the factors affecting natural production changed from year to year. To improve dependability of nauplii production, maturation technology was gradually developed. At this time, only a few researchers and companies were investigating maturation of penaeid broodstock, mainly P. vannamei and P. stylirostris. Little was known regarding the dietary and environmental requirements to induce maturity and natural mating. In 1978, Marifarms brought P. vannamei and P. stylirostris nauplii into the US, and in 1981 it sold the operation and moved to Ecuador.
Advancements in hatchery technology
In the early to mid 1980s, larval production facilities in the Americas were based on modified “Galveston” or “French” production methods. At the same time, larval diets became increasingly available, and Asian, European and U.S. companies began producing specifically formulated shrimp larviculture diets, which essentially supplemented the original feeding scheme. Improvements in cyst quality and increased implementation of cyst decapsulation increasingly started reducing artemia consumption.
There were other natural foods tested or used in larviculture, including rotifers, nematodes, and boiled egg yolks, but algae and artemia remained the foundation of feeding regimes. Maturation had been incorporated into several operations by this time, using either wild or pondraised broodstock. It was achieved through eyestalk ablation of the females – which increased the rate of maturity – and by controlling photoperiod and temperature in maturation systems. The maturation diet used consisted mainly of fresh foods supplemented with commercial pellets. A typical diet consisted of squid, marine bloodworms, oysters, clams, and a high protein pellet.

The improvement trends that began in the 1980’s continue today, but shrimp larviculture operations still rely heavily on algae and artemia to produce PL, although artificial diets today make up a much larger percentage of the diet than they did back in the 1980’s. In addition, at many maturation facilities the use of wild broodstock is diminishing, as is ablation of females.
Bloodworms are being replaced by enriched adult artemia, but fresh foods still make up a large proportion of the diet. We still have not achieved complete replacement of microalgae and artemia in larviculture, or a complete fresh food replacement in maturation. We have certainly made many advances in larval shrimp nutrition in recent years, but still have to go further until we can economically produce nauplii and PL using only artificial diets.
Larviculture and liquid diets at Aquamarina de la Costa
During the last 10 years, Aquamarina de la Costa, a prominent shrimp farm and hatchery in Venezuela, has tested several diets on a commercial scale, including microparticles, microencapsulated particles, and during the last three years, liquid larval diets. It is difficult to compare diets between years, because many variables that affect larval production (i.e., water quality, broodstock and nauplii quality, management, etc.), are continually changing, sometimes gradually and at other times drastically. However, I will describe in general terms our current conditions and management practices.
The Aquamarina de la Costa larviculture operation currently practices an “all in / all out” production scheme; that is, after each production cycle the larviculture system (i.e., tanks, pipes, aerators, etc.) are all sterilized and then dried out. Starting with a clean system for each production cycle, the tanks are filled with filtered, sterilized seawater (using chlorine, ozone and UV sterilization). Microalgae is added at low density (50,000 cells per milliliter). Nauplii (N- 3) are acclimated to tank conditions and then stocked at a density of 120 to 150 per liter.
Liquid larval diets are first administered when the larvae are molting to the protozoea one stage (12 to 16 hours post-stocking), and they are incrementally increased until harvest , based on larval stage, population, and tank conditions. In addition, each tank is provided with a constant flow of sterilized seawater. Microalgae densities are monitored several times per day, and additional microalgae added if required. When the shrimp larvae molt into the post-larval stage, live artemia nauplii are then added based on the population counts of each tank, with a specific and predetermined number of artemia nauplii per shrimp larvae for each stage.

When we began testing commercial liquid diets at our larviculture facility, we followed the feeding recommendations listed on the packages of the various commercial manufacturers. Over the last three years, we have made only minor adjustments to the original feeding formats. Our current feeding program is based on water volume (particles per milliliter) from protozoea 1 through mysis 1 stage. After the larvae molt into the mysis two stage, we adjust our feeding program to a population feeding (particles per larvae) regime. We follow this scheme through to harvest. In addition to the programmed feeding schedule, visual observations of the tank condition and larval activity are used to increase or reduce the level of feed. The two critical points of an effective feeding program, whether using dry or liquid feeds, are visual monitoring and accurate population estimates.
We have not tested all of the available diets, but under our production conditions (i.e., sanitation level, water quality, nauplii quality, etc.), we have seen very positive quantitative and qualitative results when using liquid larval diets. There are several commercial manufacturers of liquid larval diets for penaeid shrimp, and in this article, one product will not be promoted over others. Nevertheless, I will present some general observations and comments regarding our use of liquid feeds. The liquid products are available in two forms: ready to use, or in a concentrated, high solids form which must be diluted before use. We have used each brand product singularly and in conjunction with each other.
Our first observation regarding liquid feeds was that under our specific situation, savings on labor were possible, because a larviculture technician could pour, measure and dilute the liquid feed much more rapidly than he/she could weigh and blend dry microparticle diets. Using the liquid diet also lends itself to the possibility that one day an automated feeder (based on a peristaltic pump) could be used to apply larval feed to several tanks on a continuous basis, thereby significantly reducing labor needs and associated costs.
The second observation was that, on average, the production cycle was reduced by one day when compared to our original feeding regime (without liquid diets). With 12 or more production cycles per year, this represents a significant cost saving. Additionally, larvae that are molting faster are less prone to infections by filamentous bacteria and protozoans.
Over the last several years, we have made a concerted effort to reduce the consumption of artemia cysts during PL production at our facility. Each year, we have adjusted the feeding rate or schedule to aid in achieving this reduction. We operate on a 24-hour basis, apply the liquid diets to the larval tanks every two hours, and add artemia nauplii (starting at mysis-3 – PL1 stage) every four hours. During 1999, we consumed a little under one kg. of artemia cysts per million PL5 produced. This constituted a significant reduction, which we felt was accomplished by the use of liquid larval diets and the high survival rates (averaging > 70 percent), with harvest densities of slightly less than 90 PLs per liter. PL size and quality were excellent at this density, and improved survival was carried over to the nursery tank system at the farm site.

The future
The system described at the beginning of this article was an early production method that enhanced natural production of algae, and was supplemented with Artemia and very small amounts of artificial diets to produce shrimp PLs at low densities. Current production methods are based on nauplii produced from domesticated, and in some cases, genetically improved broodstock. Larviculture stocking densities are approximately 10 times higher than the typical system of 25 years ago, and also have increased survival rates. The improvements that we have experienced in shrimp culture have been gained through the efforts of many individuals and companies, researching the many variables involved in our industry.
What will we see in the next 25 years? Will we have production systems with no discharge into the environment? Will we use only diseasefree stocks, genetically selected or genetically engineered for improved growth rate in all environments and immune to all known shrimp diseases? Will we still rely on natural foods for maturation, larviculture and grow-out? Will all larviculture feeds be derived only from low cost and/or genetically engineered vegetable proteins? I hope that the above questions – and many more – will be answered positively within the next 25 years.
(Editor’s Note: This article was originally published in the February 2000 print edition of the Global Aquaculture Advocate.)
Now that you've reached the end of the article ...
… please consider supporting GSA’s mission to advance responsible seafood practices through education, advocacy and third-party assurances. The Advocate aims to document the evolution of responsible seafood practices and share the expansive knowledge of our vast network of contributors.
By becoming a Global Seafood Alliance member, you’re ensuring that all of the pre-competitive work we do through member benefits, resources and events can continue. Individual membership costs just $50 a year.
Not a GSA member? Join us.
Author
Tagged With
Related Posts
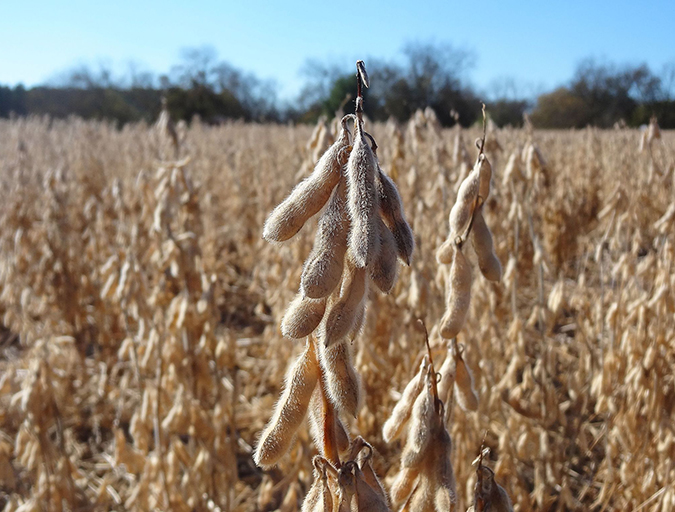
Aquafeeds
A look at phospholipids in aquafeeds
Phospholipids are the major constituents of cell membranes and are vital to the normal function of every cell and organ. The inclusion of phospholipids in aquafeeds ensures increased growth, better survival and stress resistance, and prevention of skeletal deformities of larval and juvenile stages of fish and shellfish species.
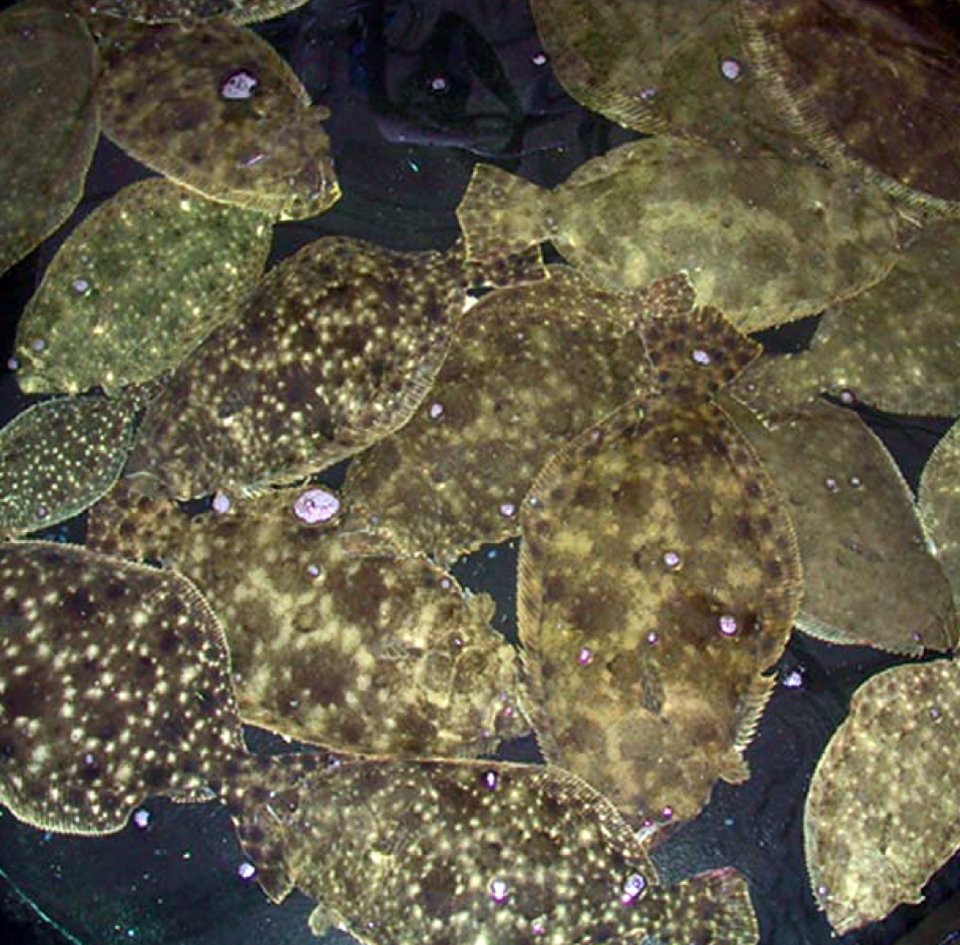
Health & Welfare
Florida study achieves tank spawning of southern flounder
Southern flounder offer potential in aquaculture to answer declining fishery landings and increased demand, but insufficient fingerlings are available.
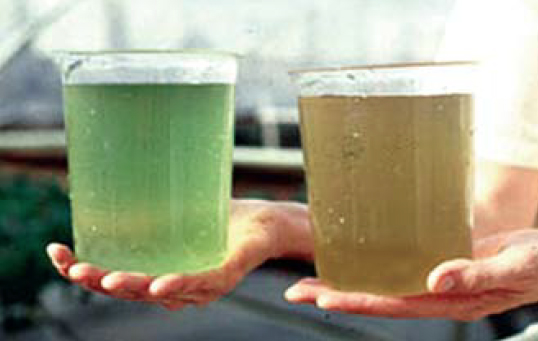
Health & Welfare
Microbial flocs for aquaculture
Microbial flocs consist of a variety of bacteria, fungi, microalgae and other organisms suspended with detritus in culture water.

Aquafeeds
Aquaculture Exchange: Rick Barrows
After 14 years with the USDA’s Agricultural Research Service, Rick Barrows talks about the importance of finding ‘complete’ and commercially viable alternative sources of omega-3 fatty acids and continuing innovation in the aquafeed sector.