Shrimp farming in the five major exporting countries could use less energy by focusing on water exchange and aerator use
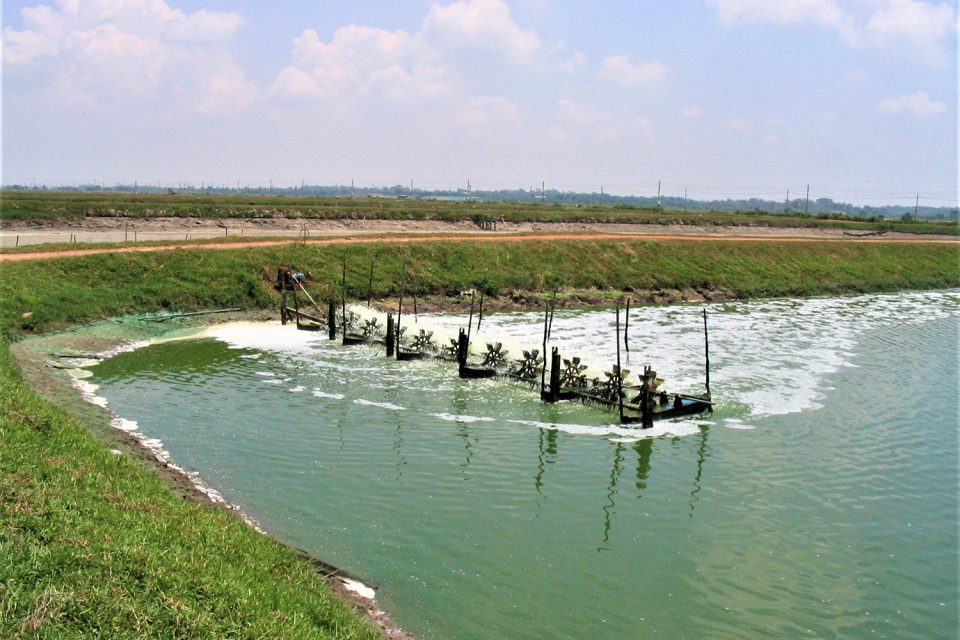
Energy use is a resource use issue because there is a looming shortage of fossil fuels that are the source of most of the world’s primary energy. In addition, the combustion of fossil fuels results in carbon dioxide emissions into the atmosphere that increase the greenhouse effect of the atmosphere. Shrimp farming, like almost all other human activities, requires energy and produces greenhouse gas emissions.
Energy use data are reported here for whiteleg shrimp production are based on a survey of farms in the five major exporting countries for farmed shrimp. The number of farms included for each country were as follows: 101 in Ecuador; 89 in India; 131 in Indonesia; 34 in Thailand; and 30 in Vietnam. The findings were given in greater detail in a review article (see Aquaculture, Fish, and Fisheries 2021, 1-13).
Main direct uses
The most important direct energy uses at shrimp farms are construction and maintenance of farms, pumping water and operating mechanical aerators. There also are embodied energy uses associated with management inputs and especially with feed and fuel.
The farms all used feed, and all Asian farms applied mechanical aeration. In Ecuador, 47 percent of farms used aeration. Water exchange was also commonly practiced at farms: 21 percent in India; 37 percent in Vietnam; 50 percent in Thailand; 86 percent in Ecuador; 94 percent in Indonesia. Farms in all five countries used a variety of amendments in ponds to include fertilizers, liming materials, disinfectants, oxidants, molasses and sugar, zeolite, various minerals, and probiotics. The amendments, like feed and fuels, contained embodied energy (Table 1). The total energy use was calculated to include direct energy use on farms for fuels plus the embodied energy associated with feeds, fuels and pond amendments.
Boyd, Energy Use, Table 1
Input | Direct | Embodied |
---|
Input | Direct | Embodied |
---|---|---|
Diesel fuel | 0.0387 GJ/L | 0.007 GJ/L (»0.0007 GJ/kW·hr |
Gasoline | 0.0349 GJ/L | 0.0084 GJ/L (»0.008 GJ/kW·hr) |
Electricity | 0.0036 GJ/kW·hr | 0.00539 GJ/kW·hr |
Shrimp feed | --- | 9.59 GJ/t |
Agricultural limestone | --- | 1.29 GJ/t |
Lime | --- | 5.30 GJ/t |
Molasses | --- | 0.48 GJ/t |
Sugar | --- | 1.90 GJ/t |
Urea | --- | 29.2 GJ/t |
Triple superphosphate | --- | 4.3 GJ/t |
Mixed fertilizers | --- | 14.2 GJ/t |
Mineral mixes | --- | 4.8 GJ/t |
Zeolite | --- | 8.4 GJ/t |
Calcium hypochlorite | --- | 0.30 GJ/kg |
Other disinfectants | --- | 0.18 GJ/kg |
Fuel was used by pumps, aerators, tractors, vehicles and other mechanized farm machinery. In Asia, electricity was the main fuel used, but in Ecuador, use of diesel fuel greatly exceeded the use of electricity. Gasoline was a minor fuel in all countries.
Total energy use (Table 2) ranged from 56.0 GJ/t shrimp in Ecuador to 98.8 GJ/t shrimp in Thailand. The weighted energy use average for all countries was 76.8 GJ/t.
Boyd, Energy Use, Table 2
Country | Energy use (GJ/t shrimp) |
---|
Country | Energy use (GJ/t shrimp) |
---|---|
Ecuador | 56 |
India | 90 |
Indonesia | 75.4 |
Thailand | 98.8 |
Vietnam | 89.5 |
Embodied energy comprised bout 60 percent of total energy in Asia where electricity was the main energy source. In Ecuador – where diesel fuel was the main energy source – embodied energy comprised about 38 percent of total energy. The largest embodied energy components were fuels and feed.
Farm construction, maintenance
Farm construction and maintenance requires a lot of energy. However, when amortized over 30 years, annual construction and maintenance resulted in use of 11.51 GJ/ha/year of direct energy and 2.54 GJ/ha/year of embodied energy for farms in Ecuador with large ponds (5–10 ha). In Asia, 27.9 GJ/ha/year direct energy and 5.0 GJ/ha/year of embodied energy were incurred for construction of farms with small ponds (0.25–0.75). When the amortized construction and maintenance estimates are divided by annual farm shrimp production (t/ha/year), it becomes a rather small proportion of energy use per metric ton of shrimp production.
There was a small portion of farms with ponds of hyper-intensive production that were completely lined with plastic. These farms also tended to have somewhat smaller ponds. Direct energy for construction and maintenance was calculated to be 46.3 GJ/ha/year and embodied energy as 11.7 GJ/ha/year (including embodied energy for plastic liners). Shrimp production was greater in these ponds than in normal intensive farms, and energy use for construction, and maintenance per metric ton of shrimp was similar to that of normal intensive operations.
Quantifying greenhouse gas emissions from global aquaculture
Production
Energy use for the production of farmed shrimp per kilogram of edible protein was rather high (0.52-0.92 GJ/kg). By contrast, values for the major terrestrial-source meats were 0.11–0.17 GJ/kg for broiler chicken protein, 0.10–0.37 GJ/kg for pig meat protein and 0.27–0.53 GJ/kg for beef cattle protein. Obviously, efforts should be made to lessen the amount of energy used in shrimp aquaculture.
The main reasons for high energy use for farmed shrimp is the use of mechanical aeration, water exchange that incurs pumping energy and feeds of high embodied energy content. Feeds for broiler chickens, pigs and beef cattle contain an average of 4.2, 3.8 and 3.2 GJ/t of embodied energy, respectively. This is much lower than 9.59 GJ/t of embodied energy for shrimp feed. This difference relates to the use of fishmeal, animal byproducts meals, and fish oil in shrimp feed.
Reducing energy use
Efforts to reduce the energy use for farmed shrimp should focus on reduction in water exchange rates, adoption of more efficient aerators and better aerator operation schedules. There is no scientific evidence that water exchange is needed other than for avoiding excessive salinity in some arid areas.
Farm-made, “long-arm” paddlewheel aerators popular in Asian countries are highly inefficient. It would be more cost- and energy-use effective to use factory-made paddlewheel aerators. Farmers tend to use more aerator horsepower per hectare than necessary even when using factory-made aerators. Many farmers do not adjust the number of aerators in use in accordance with the standing stock of shrimp in ponds. Moreover, in daytime a portion of the aerators could be shut down until the evening.
The embodied energy content of shrimp feed can be reduced by the choice of ingredients. However, shrimp feed must have a rather high crude protein concentration compared to land animal feeds. As a result, it is likely not possible to produce shrimp feeds that have embodied energy contents as low as found in other animal feeds.
Perspectives
Although shrimp, like beef cattle, are a high energy use commodity, energy use for shrimp could be reduced greatly and at least to the level for beef cattle. This would conserve energy and lessen carbon dioxide emissions for farmed shrimp. Moreover, it would lessen production costs. These benefits would seem to make the effort well worthwhile.
Now that you've reached the end of the article ...
… please consider supporting GSA’s mission to advance responsible seafood practices through education, advocacy and third-party assurances. The Advocate aims to document the evolution of responsible seafood practices and share the expansive knowledge of our vast network of contributors.
By becoming a Global Seafood Alliance member, you’re ensuring that all of the pre-competitive work we do through member benefits, resources and events can continue. Individual membership costs just $50 a year.
Not a GSA member? Join us.
Authors
-
Claude E. Boyd, Ph.D.
Corresponding author and Professor Emeritus
School of Fisheries, Aquaculture and Aquatic Sciences
Auburn University, Auburn, AL 36849 USA -
Robert P. Davis, Ph.D.
School of Fisheries, Aquaculture and Aquatic Sciences
Auburn University, Auburn, AL 36849 USA -
Aaron McNevin, Ph.D.
World Wildlife Fund
Washington, DC 200037 USA
Tagged With
Related Posts
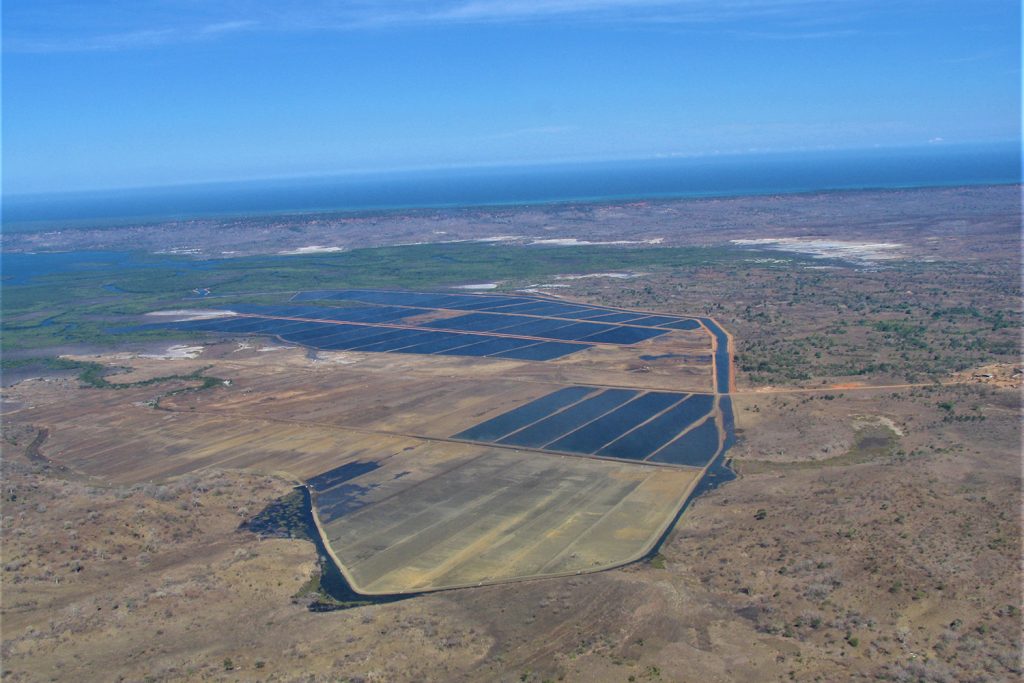
Responsibility
A comparison of resource use in shrimp farming, part 1: Land
Prof. Boyd discusses land use in shrimp farming in the five major exporting countries of farmed shrimp: Ecuador, India, Indonesia, Thailand and Vietnam.
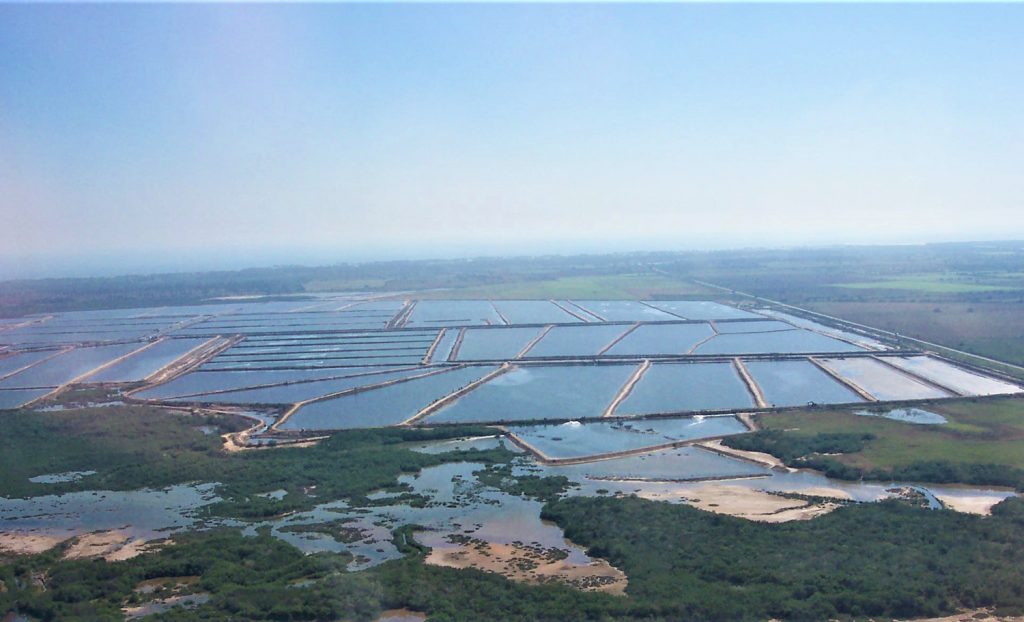
Responsibility
A comparison of resource use in shrimp farming, part 2: Water
In part two of this series, the authors suggest steps to reduce the pollution potential of shrimp farming by paying special attention to uneaten feed.

Responsibility
An introduction to circular economy principles in aquaculture
In the latest article from the GAIN project, implementing circular economy principles can help increase the sustainability of aquaculture production.
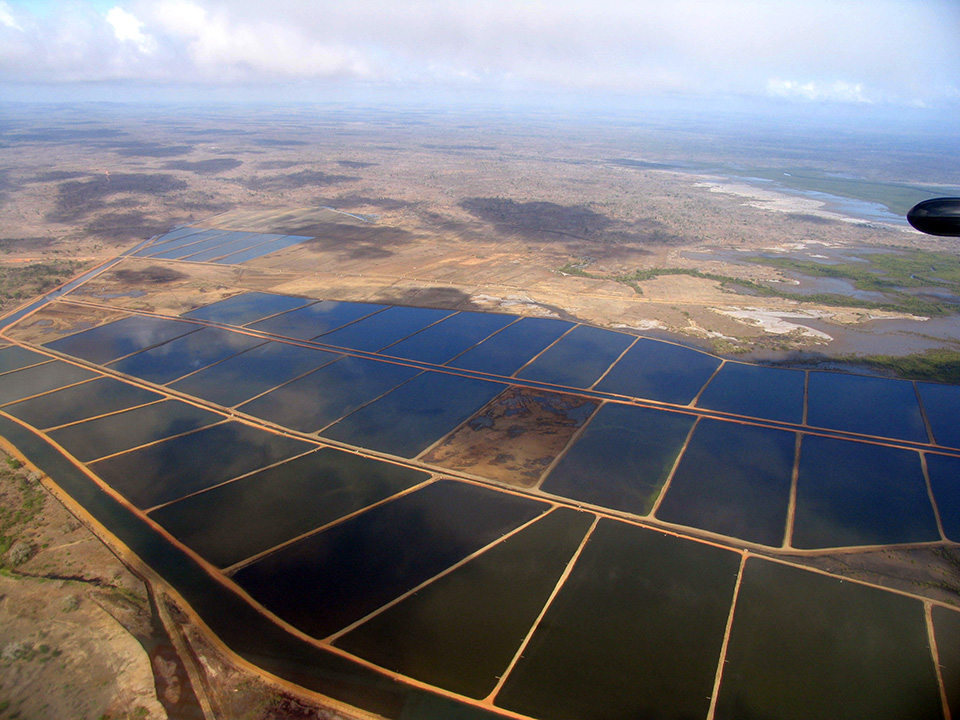
Responsibility
Aquaculture ponds hold carbon
Although 16.6 million metric tons of carbon are annually buried in aquaculture ponds, estimated carbon emissions for culture species have approached several metric tons of carbon per metric ton of aquaculture product.