France-based company will test corn byproducts on Hermetia illucens before deciding on a larger footprint
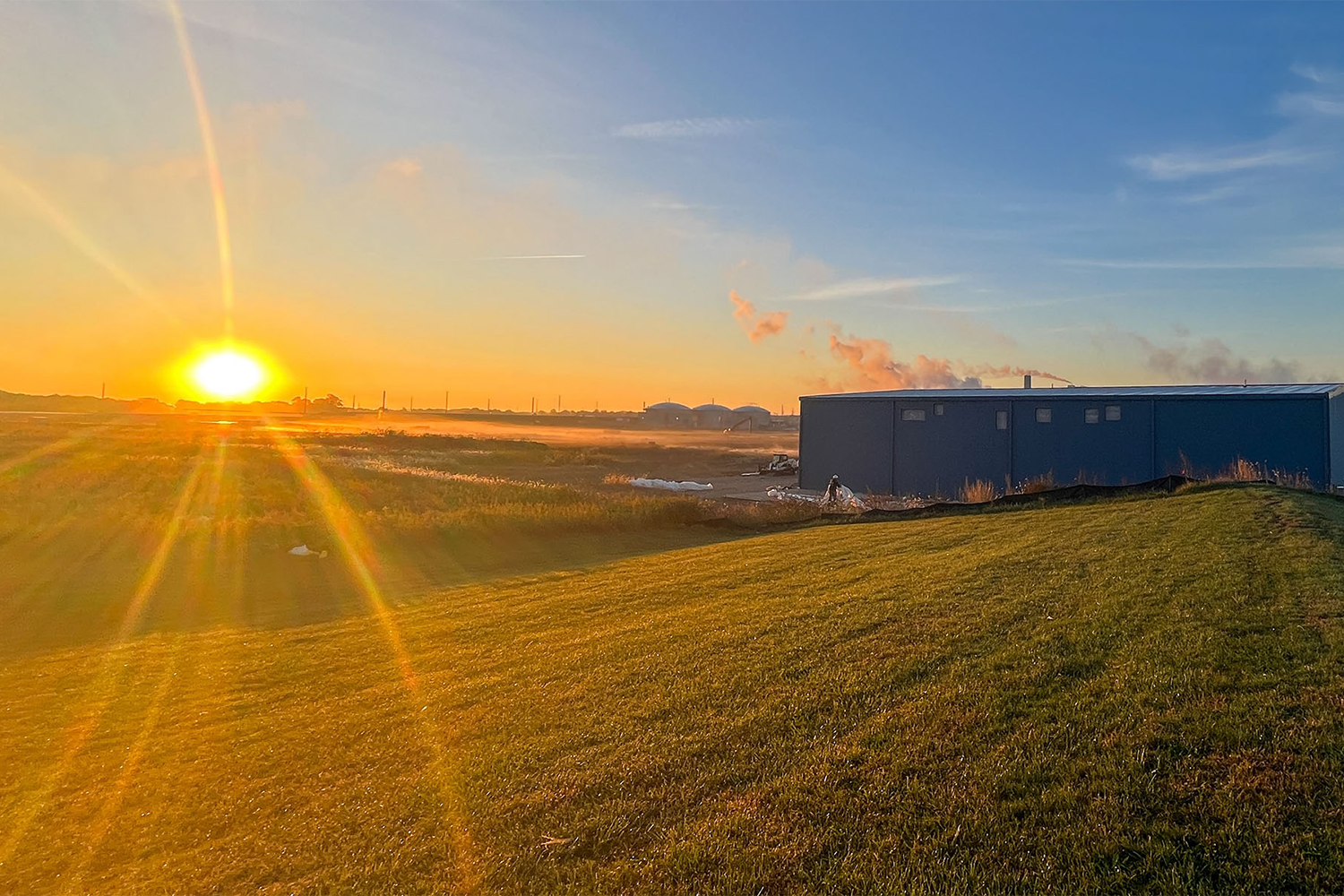
If you build it, they will buzz. A new black soldier fly facility – the first in the United States – is now online but any aquaculture business springing from it might take a while.
Innovafeed’s January launch of the Innovation and Research Center for insect-based ingredient production in Decatur, Ill., marked the company’s first step in industrial production in North America.
The $10 million pilot plant is located next to the Archer-Daniels-Midland company, a large corn processing facility whose byproducts Innovafeed will feed to its black soldier flies (Hermetia illucens, BSF) to produce BSF meal and oil. But for Innovafeed, the lure to America was not really about aquafeed sales – at least not yet.
“The availability of these corn byproducts is what brought us to North America, not the aquaculture market, which is much smaller in North America than it is in Europe,” said Maye Walraven, Innovafeed’s general manager for North America. “We turn the insects into two types of ingredients: a protein meal for aqua feed or pet food, and an insect oil, which is rich in lauric acid and has positive digestive benefits for swine and poultry.”
Innovafeed’s strategy of co-locating its plants next to large agricultural processors is not new. In France, the company uses wheat stillage, a byproduct, and wheat bran from a starch factory to produce 10,000 tons of insect protein annually. Since corn byproducts are more readily available than the wheat byproducts Innovafeed uses in Europe, the company could potentially produce four times more in the United States each year.
Black soldier fly larval production in a stacked production system
If its pilot phase in Decatur is successful, the company will build a large-scale processing plant that would supply insect protein to land and sea-based aquaculture companies in Canada and Alaska, Chile and possibly shrimp farmers in Ecuador. Its main markets in North America are pet food and livestock feed for poultry and swine.
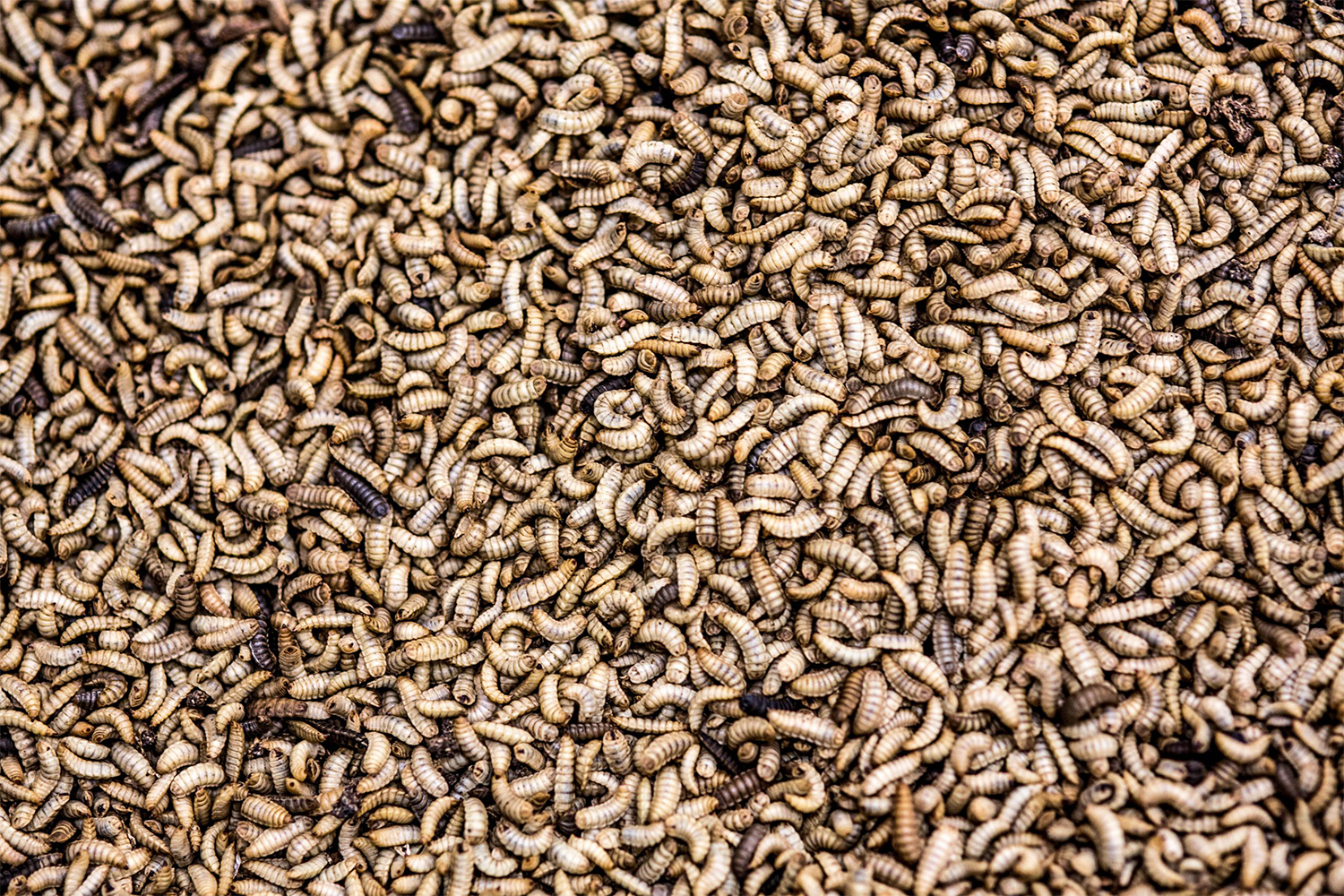
Its black soldier fly colonies will feed on corn gluten and steep water, raw material with low nutrient concentration. By processing the larvae, Innovafeed will create high-quality ingredients for animal and aquaculture feed.
“The innovation center is a research facility where we can test how the insects react to the corn byproducts, and tweak and optimize technology before we invest capital into a larger site,” Walraven said. While the test period duration will depend on the challenges the company experiences during testing, in France its innovation center conducted 18 months of testing before a full-scale site was launched.
A full-scale processing plant would take up to 24 months to build. Walraven said that in terms of insect production capacity, the United States is three to four years behind Europe, where legislation to permit insect meal in aquaculture was passed in 2017.
Insect producers are working collaboratively through North American Coalition for Insect Agriculture to effect legislative changes that will lead the way for these new ingredients to be adopted. Currently, black soldier fly larvae ingredients like BSFL meal and oil have been granted approval by the Association of American Feed Control Officials for adult dogs, swine and salmonids. Black soldier fly oil for poultry is under review, according to Walraven, while approvals for cat food and other finfish feeds is expected sometime this summer.
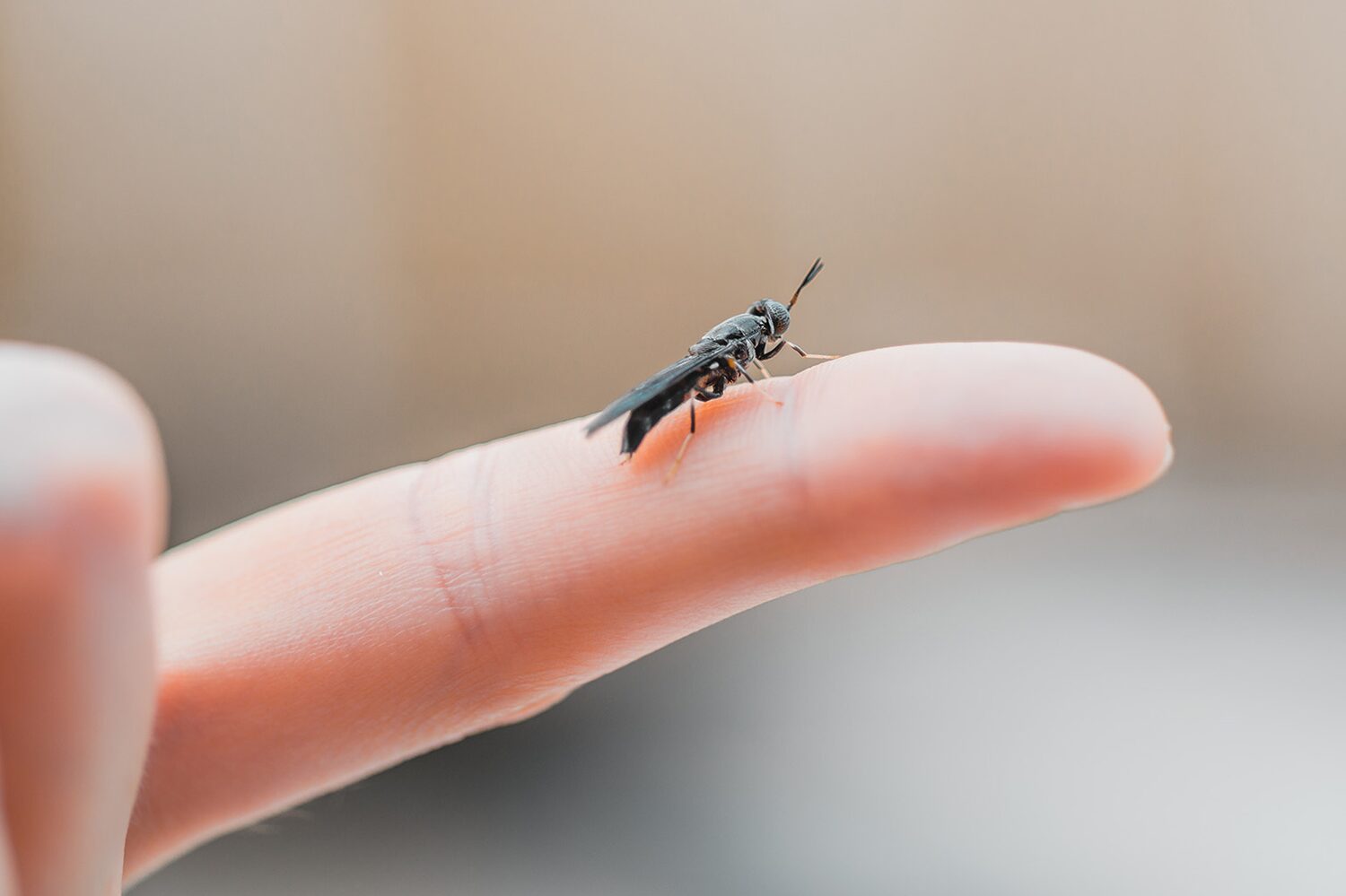
“Feed formulators are increasingly facing challenges with getting conventional protein sources like chicken meal or fishmeal,” she said. “There’s a concern that we’ll have a shortage of 20 million [metric tons] by 2050 . That’s fueling our development because we can definitely make a difference. Our insect meal will increase the diversity of ingredients that formulators can use to address this shortage, as well as bring the benefits of insect meal.”
“Our goal is to improve the sustainability of food supply chains,” she added. “We think of insect ingredients as delivering impact in four ways: We can produce protein at a lower carbon footprint, we can reduce the impact on biodiversity, we can build our plants in areas with lower economic dynamics, and we can use our industry to build resilient food systems and create more food security for the future.”
Now that you've reached the end of the article ...
… please consider supporting GSA’s mission to advance responsible seafood practices through education, advocacy and third-party assurances. The Advocate aims to document the evolution of responsible seafood practices and share the expansive knowledge of our vast network of contributors.
By becoming a Global Seafood Alliance member, you’re ensuring that all of the pre-competitive work we do through member benefits, resources and events can continue. Individual membership costs just $50 a year.
Not a GSA member? Join us.
Author
-
Lauren Kramer
Vancouver-based correspondent Lauren Kramer has written about the seafood industry for the past 15 years.
Tagged With
Related Posts
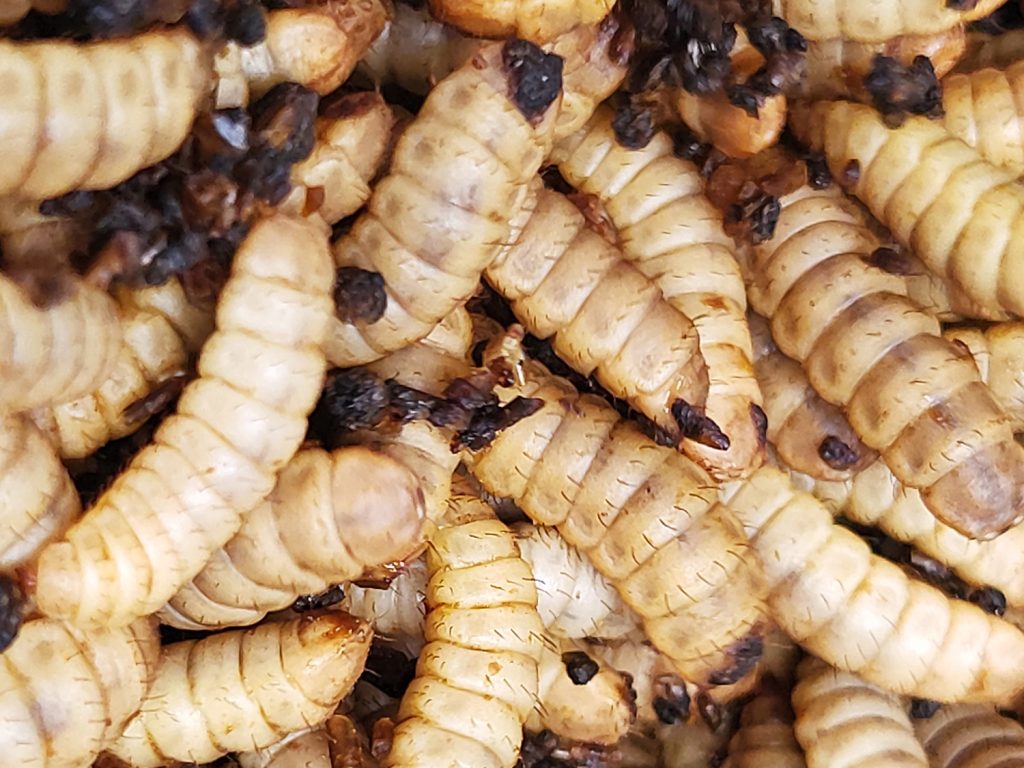
Aquafeeds
Bioactivity of black soldier fly larvae meal
Black soldier fly larvae meal has anti-inflammatory molecules that may alleviate inflammation but is outperformed by quercetin in this capacity.
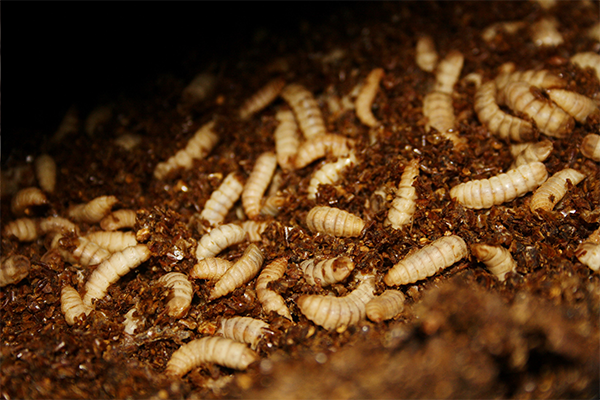
Aquafeeds
Black soldier fly larvae meal producers get innovative, collaborative
After years of R&D, black soldier fly larvae meal is now seen as a feed ingredient that is en route to widespread industry adoption.
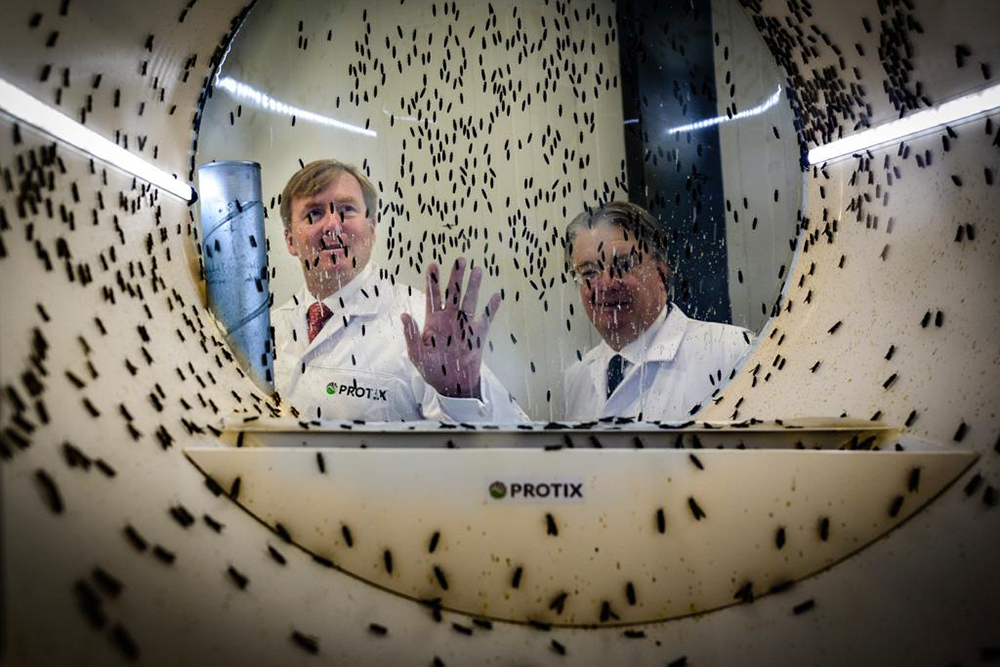
Aquafeeds
World’s largest fly factory attracting investors eyeing aquafeed expansion
A high-capacity black soldier fly factory puts Protix in position to ramp up production. Investors explain why they’re betting on the sector’s success.
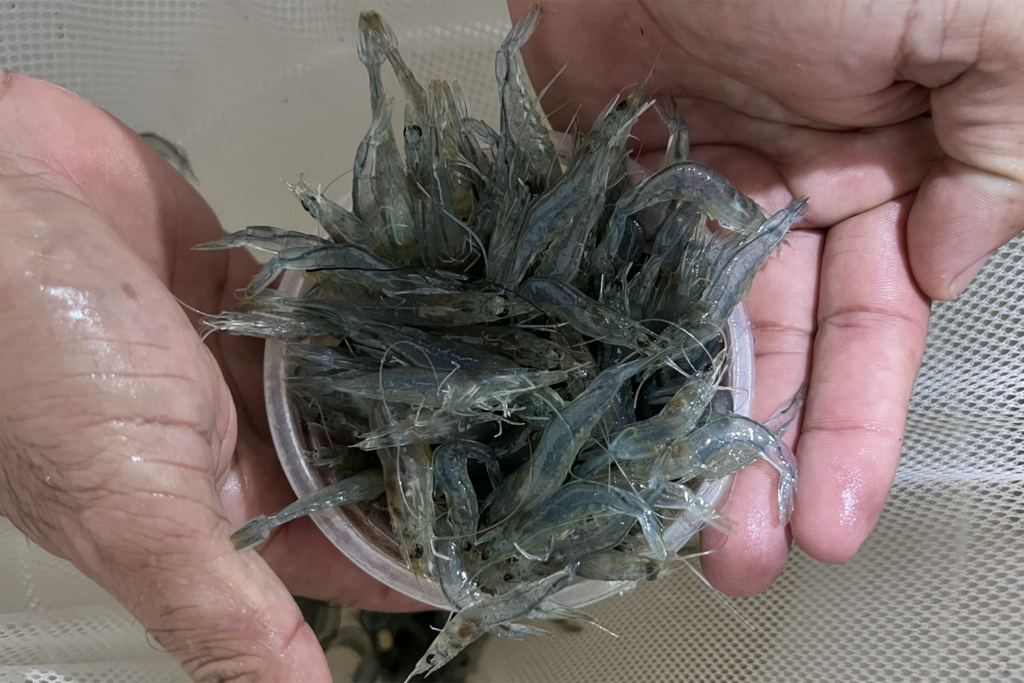
Aquafeeds
Black soldier fly larvae meal cost-effectively replaces fishmeal in Pacific white shrimp postlarvae nursery diets
Black soldier fly larvae meal can effectively replace fishmeal in shrimp diets if nutrient balance and price sensitivity are properly considered.