Global Fisheries Innovation Award finalist: Cruz Foam
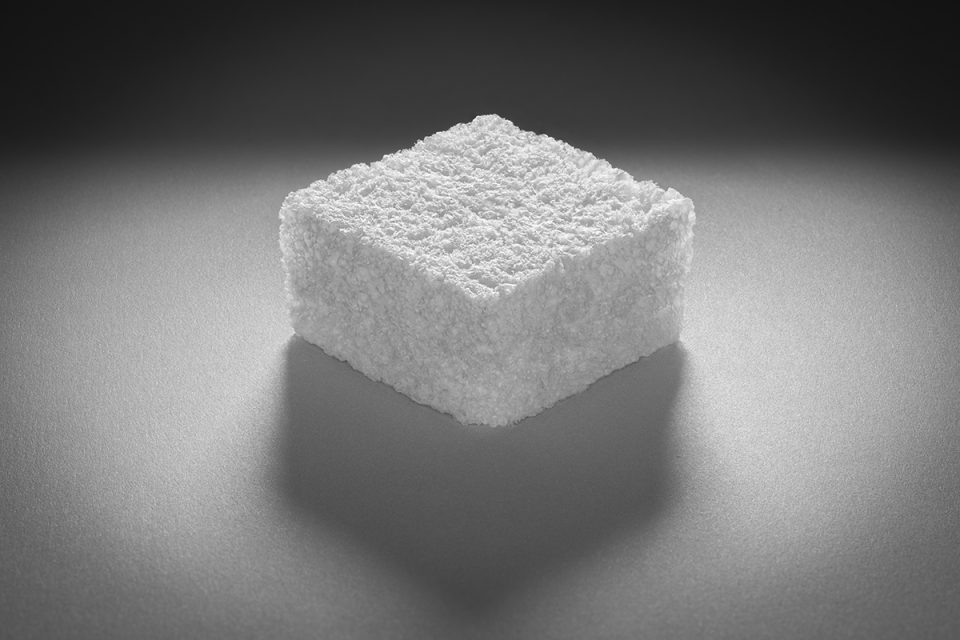
In a classic example of turning trash to treasure, Cruz Foam is turning chitin – a substance extracted from the exoskeletons of shellfish, including crab, lobster and shrimp – into a durable, biodegradable packaging foam that can be used by the seafood industry. And the Santa Monica, Calif.-based company could offer one possible remedy to the pressing problem of ocean pollution.
Concern is mounting among scientists and citizens about the pervasiveness of microplastics (small pieces of plastic less than 5 millimeters in size) and the harm caused by plastic pollution in the ocean. Most recently, the UN Ocean Conference opened with an urgent call to action to address the “ocean emergency,” which included dealing with plastic pollution “choking” the seas.
A major source of plastic waste in the ocean is expanded polystyrene – a type of plastic that when puffed with air is lightweight, buoyant, water-resistant and an excellent insulator. For these reasons, expanded polystyrene — also called foamed polystyrene, EPS or “Styrofoam” — is used widely by the seafood industry, popular among fisheries and aquaculture operations for buoys, food packaging (e.g., fish boxes or cool boxes), the interior of pontoons and marina platforms and more. Disintegrating into thousands of puffed fragments, research suggests that foamed polystyrene pollution in the ocean threatens marine life and human health, leading select U.S. states and countries to restrict or ban its use.
Despite these concerns, EPS remains popular for transporting seafood, used for both packaging and insulation purposes. It’s partly because finding practical, sustainable plastic packaging alternatives that meet acceptable quality and food safety standards hasn’t been easy.
But that’s changing. Thinking outside the polystyrene box, Cruz Foam has produced a protective biodegradable packaging foam as a sustainable alternative to petroleum-based products. For this innovation, the company is one of three finalists for the Global Seafood Alliance’s inaugural Global Fisheries Innovation Award.
‘Our pipeline of customers is overflowing’
Incorporated in 2017, Cruz Foam’s product is made from chitosan, a refined version of chitin, which is the world’s second-most abundant biopolymer next to cellulose, which is typically sourced from plant fibers and wood. The company sources it primarily from shrimp shells, naturally occurring waste streams in the seafood industry.,
“We divert [the shells] from landfills and use them to create a product that replaces conventional packaging foam,” said John Felts, who co-founded the company with Marco Rolandi.
Felts said Cruz Foam breaks down in 120 days or less, with a 97.9 percent average biodegradation in soil. It produces high-quality organic waste that can be used as nutrient-rich compost and biogas used for electricity.
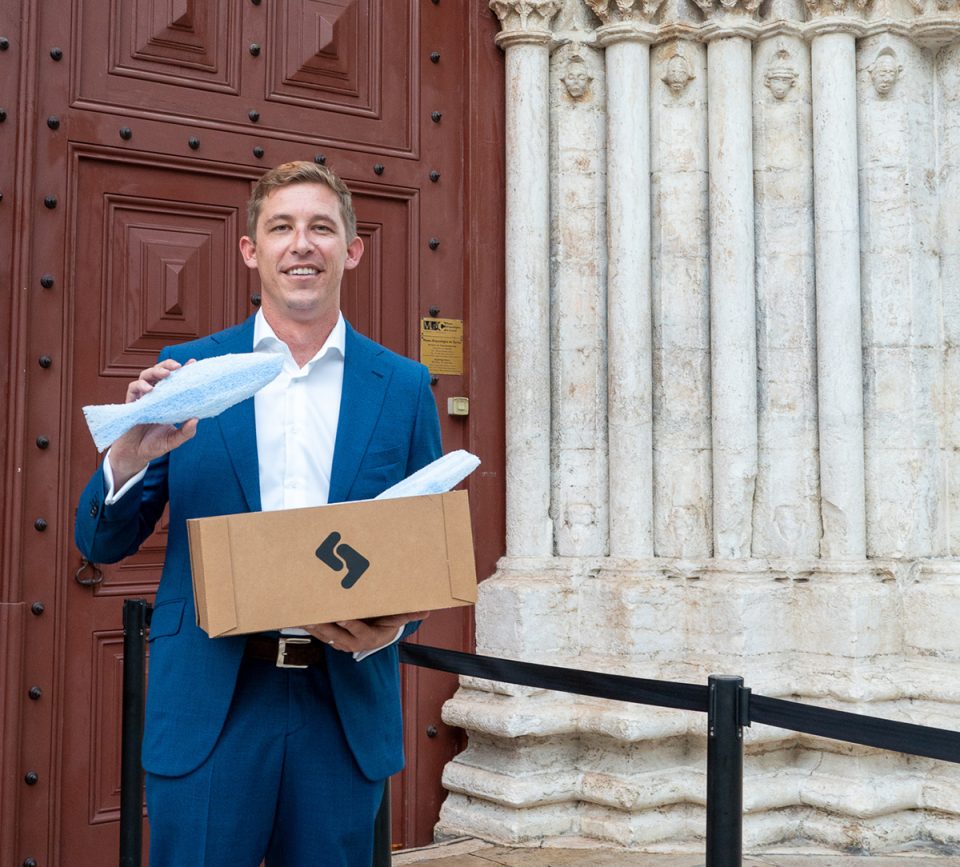
While the company’s market entry was focused on appliance protection, the foam’s composting properties make it a promising solution for the food service industry and for cold chain shipping of high-value seafood products.
“We know we have a good formula for cold chain shipping,” Felts said. “We’re just doing another six months of product development to ensure we can provide the best fit for the seafood industry’s needs.”
Felts said chitin is “literally everywhere. Its most abundant source is crustacean shell waste but it’s abundant from insects and fungi.” Chitin is comprised of minerals, proteins, an amide derivative of glucose, whereas chitosan is a modified version that is easier to manufacture at scale, explained Felts. “When chitin is combined with certain minerals it forms a strong composite material,” he said.
Cruz Foam extracts the proteins and mixes what remains with non-food-grade starches and plant-based plasticizers to convert it into packaging.
At the company’s 10,000-square-foot R&D facility, Felts and his 23-person team are fine-tuning different formulas of the combination, creating firm foams comparable to Styrofoam or flexible, soft foams used for shipping small electronics. The goal is to innovate new materials and validate the process to a point where Cruz Foam can partner with large manufacturers. And there’s lots of demand from those manufacturers.
“Our pipeline of customers is overflowing,” Felts said. “Regulation is pushing toward greenifying materials around single-use materials, especially packaging, and the packaging industry is looking aggressively for solutions to meet this shift. Our solution answers this need.”
The fishing industry’s use of tons of petroleum-based Styrofoam packaging yearly is in direct conflict with its desire to protect the health of the world’s oceans.
From spinning to scaling
The company has two formulas ready to go and is in the first stage of commercial production with packaging partners. The challenge lies in accelerating the first stages of identifying a steady supply of chitin.
“We have to make sure we have volume supply secured as we grow,” he explained. “Though there’s more than enough chitosan, it’s not a well-developed supply chain right now because no one is using it at high volume yet. We also have to help our packaging converters understand the different capabilities of our foam to allow widespread adoption to happen faster.”
Cruz Foam plans to license its technology to achieve scale and Felts believes his biodegradable, sustainable foam product will be a great fit for the seafood industry.
“The fishing industry’s use of tons of petroleum-based Styrofoam packaging yearly is in direct conflict with its desire to protect the health of the world’s oceans,” he noted. “Over 380 million tons of plastic are produced every year and 50 percent of that is for single-use purposes such as product packaging. The EPA estimates that the U.S. alone produces more than 3 million tons of Styrofoam each year, making this an existential issue for both earth and sea.”
If successful, Felts says Cruz Foam could become the circular industry standard for cold chain protective packaging material, an alternative that industries have long sought. “No other company has yet been able to match the technical properties of Expanded Polystyrene and Expanded Polyethylene with an earth-digestible, regenerative formula,” Felts said. “This can prevent many tons of petroleum-based materials from going into landfills, or worse, into our oceans.”
Follow the Advocate on Twitter @GSA_Advocate
Now that you've reached the end of the article ...
… please consider supporting GSA’s mission to advance responsible seafood practices through education, advocacy and third-party assurances. The Advocate aims to document the evolution of responsible seafood practices and share the expansive knowledge of our vast network of contributors.
By becoming a Global Seafood Alliance member, you’re ensuring that all of the pre-competitive work we do through member benefits, resources and events can continue. Individual membership costs just $50 a year.
Not a GSA member? Join us.
Author
-
Lauren Kramer
Vancouver-based correspondent Lauren Kramer has written about the seafood industry for the past 15 years.
Tagged With
Related Posts
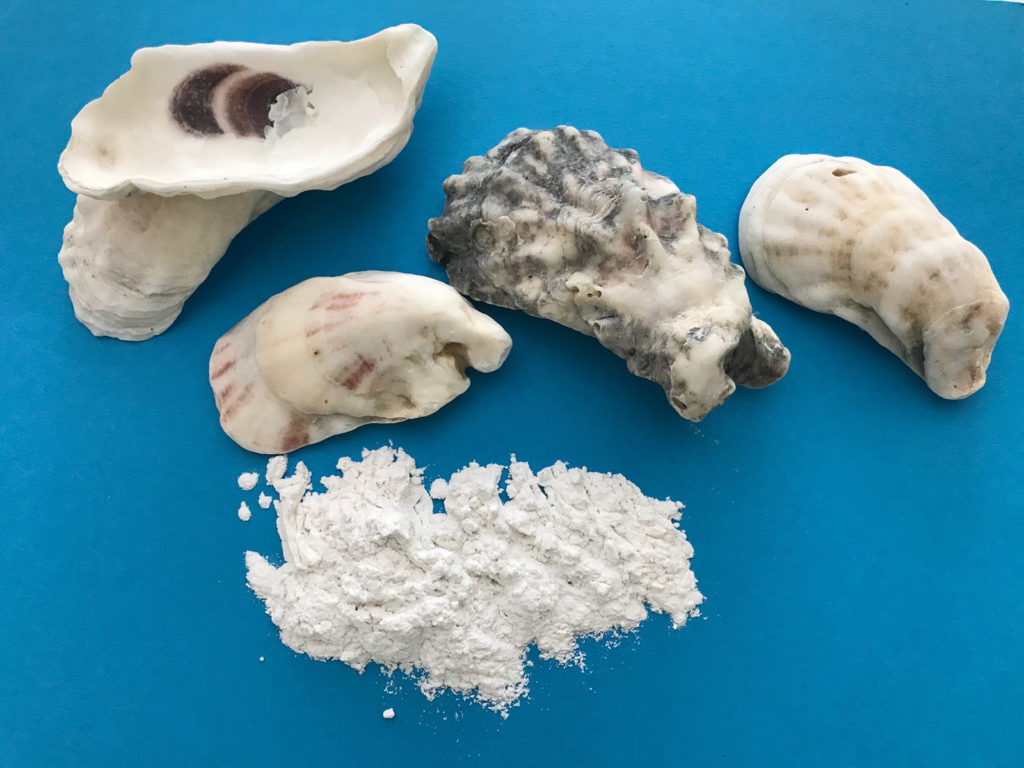
Innovation & Investment
Can an oyster-shell paint help rethink artificial reefs?
North Carolina company Shellbond seeks to commercialize a creative product made from shells, believing it could transform oyster farming.
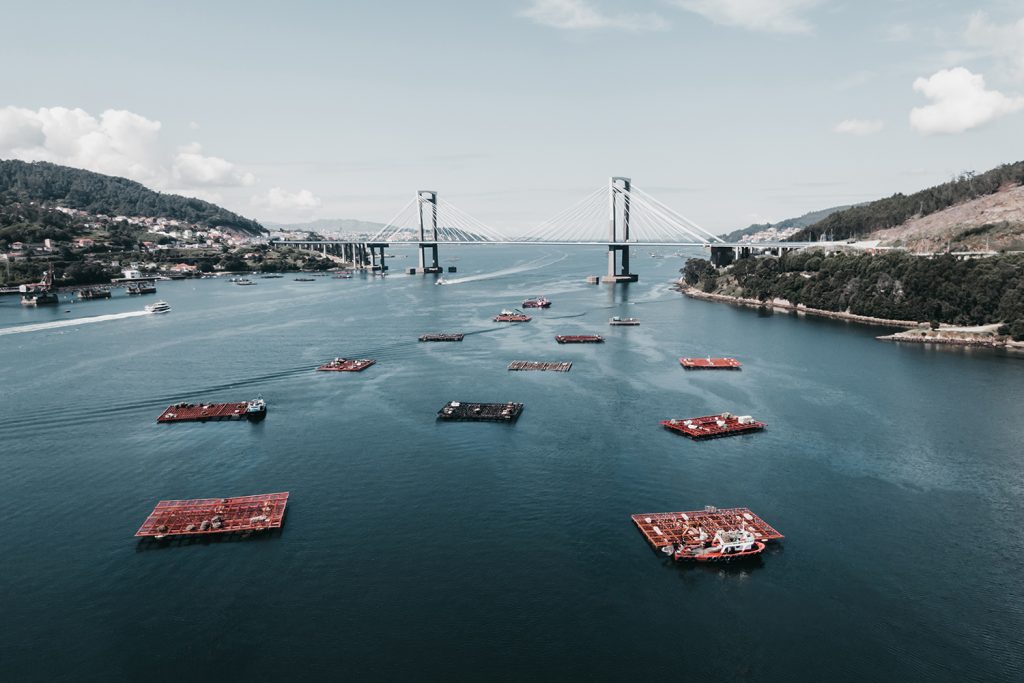
Innovation & Investment
Can plastic-eating bacteria help with fisheries’ and aquaculture’s plastics problem?
Plastic-eating bacteria have the potential to “digest” petroleum-based plastics, used in both fisheries and aquaculture. Is it feasible for recycling?
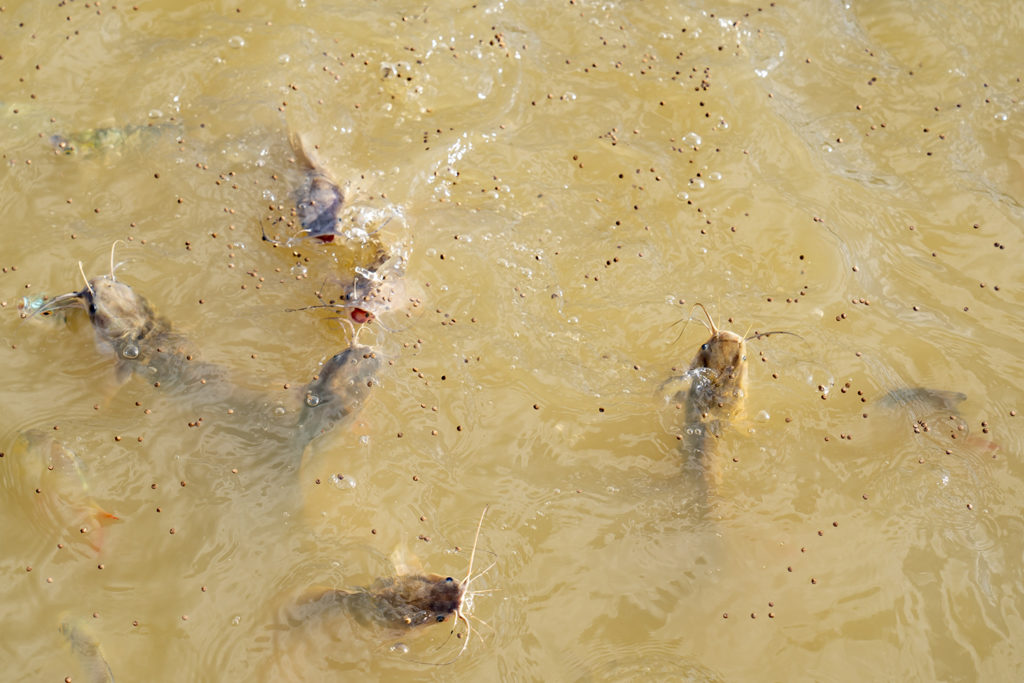
Aquafeeds
‘We will very likely find it’: Microplastics warning sounded for aquafeeds
The warning about microplastics pollution is finding its way to aquaculture, as a new study finds contaminated samples of fishmeal, a prominent aquafeeds ingredient.
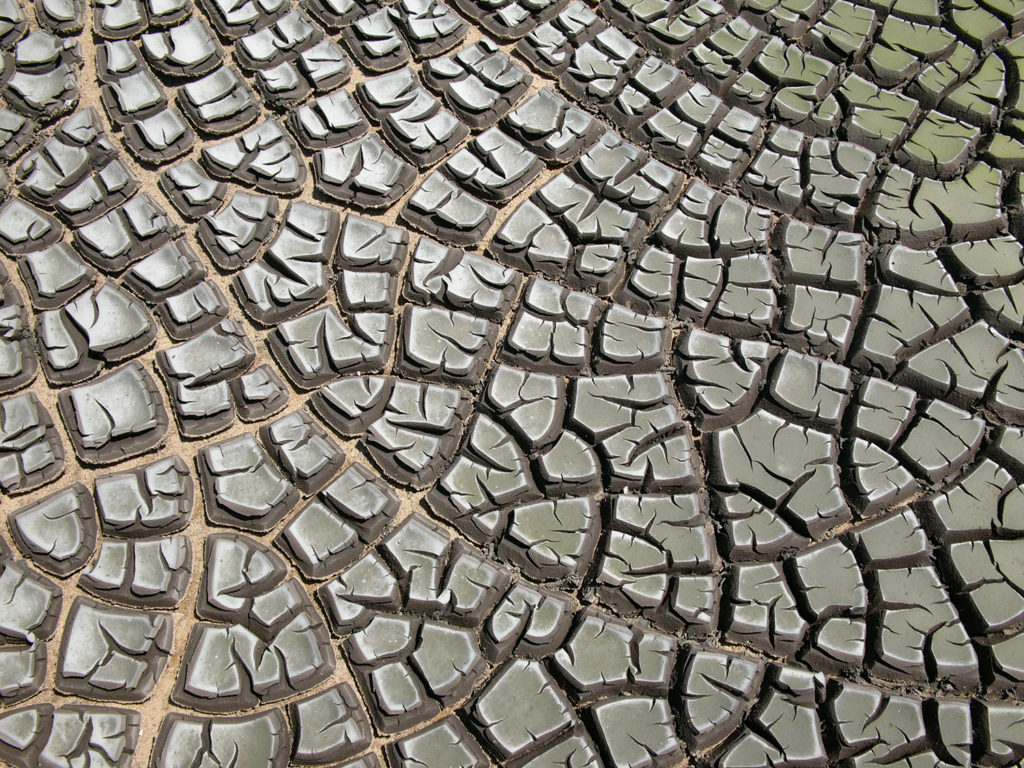
Responsibility
Composting of seafood processing sludge
Study evaluates if controlling maturation stage during seafood sludge composting through turning improves the process in comparison to static composting.