Archer Daniels Midland project utilizes waste heat and carbon dioxide

Archer Daniels Midland is a major agribusiness company whose core business is processing farm outputs for manufacturers of animal feeds and human foods. This includes processing cereal grains and oil seeds; producing feed and food additives such as citric acid, amino acids, and vitamins; and merchandizing products around the globe.
With over 23,000 employees and 368 processing plants, ADM’s operations output enough to feed 130 million people every day, which explains the company’s slogan: “Supermarket to the World.” Clearly, feeding the world’s people will be one of the biggest challenges of the 21st century.
ADM is committed to exploring new technologies to increase food production in a more efficient and environmentally friendly manner. Its hydroponics/ aquaculture operation is an example of one of the many technologies that ADM has developed.
Byproduct utilization

Nearly 20 years ago, ADM corporate leadership recognized the opportunity to utilize waste heat from corn processing to raise hydroponic vegetables on a year-round basis. A small facility was built in Decatur, Illinois, USA, to begin exploring production methods. Since ADM is also a major producer of environmentally friendly ethanol for fuel power, waste carbon dioxide (CO2) from the ethanol plant was also introduced in the hydroponics greenhouses to enhance the available CO2 levels and increase yields of the vegetable crops.
An aquaculture component was added in the early 1990s. The focus was to utilize the production advantages already in place within the existing infrastructure, and explore the feasibility of raising foodfish on a corn- and soybean-based ration.
The first few years were dedicated to research and development, and many species were experimentally cultured, including catfish, hybrid striped bass, tilapia, freshwater shrimp, prawns, American and African bullfrogs, and others. Tilapia was the species eventually selected for commercial production due to its ease of breeding, durability, market demand, and most importantly, efficiency at converting feed into animal protein.
The hydroponics/aquaculture operation has grown to 10.5 acres (4.25 hectares) under roof. It currently produces an average of 100,000 heads of lettuce and 20,000 cucumbers, as well as several thousand pounds of tilapia fish, every month of the year.
Hydroponics

The greenhouse facility produces “Boston Bibb” lettuce grown in a nutrient film technology application. In this system, water is constantly circulated through the growing trays to provide optimum nutrient availability for the plants at all times. The water solution is simply a balanced blend of the same elements that would normally be present in the soil.
When plants grow in soil, they utilize a great deal of energy growing an extensive root system to search for their food. Hydroponic culture produces rapid growth, because all the needed nutrients are constantly available at the base of each plant.
ADM can produce a mature head of lettuce in as little as 35 days. Because the vegetables grow so quickly they are classified as “young, tender” plants and are nearly 100 percent usable.
All vegetables in the farm are harvested fresh and vacuum-cooled to lock in freshness, then shipped fresh to markets daily. ADM utilizes a unique packaging system in which the Boston lettuce and some herbs are shipped with the root system on. This means that each head of lettuce is still living when purchased by the consumer. It simply does not get any fresher than that!
Tilapia production

ADM began with a small but innovative system where fish were cultured in an integrated loop with hydroponic plants. The current fish production is a separate entity from the hydroponics section.
One of the most unique aspects of ADM Aquaculture is that it is totally self-contained. Even though hundreds of tons of fish have been shipped from the building, no new tilapia have been introduced in several years. The company maintains its own breeding lines and has total control over the fish “from egg to market.” This results in exceptionally high-quality fish with a feed conversion ratio of less than 2:1.
Currently there are about 175 indoor fiberglass raceways of 10,000 gallons (45 cubic meters) each that serve as grow-out tanks. These are stocked with more than 2 million tilapia fry, which are also produced indoors. Water quality is maintained using a recirculating system with bead filters as bioclarifiers. Maximum water replacement is 5 percent per month.
No fish are processed on site. They are shipped live to large metropolitan markets throughout the U.S. and Canada.
Conclusion
As our population grows and our natural resources tighten, it will become increasingly important to utilize resources efficiently. ADM is committed to developing improved technologies to feed the world’s people. The hydoponic/aquaculture project utilizes waste heat and carbon dioxide to produce high-quality vegetables and tilapia on a year-round basis using minimal water input and vegetable protein-based feeds.
(Editor’s Note: This article was originally published in the August 2000 print edition of the Global Aquaculture Advocate.)
Now that you've reached the end of the article ...
… please consider supporting GSA’s mission to advance responsible seafood practices through education, advocacy and third-party assurances. The Advocate aims to document the evolution of responsible seafood practices and share the expansive knowledge of our vast network of contributors.
By becoming a Global Seafood Alliance member, you’re ensuring that all of the pre-competitive work we do through member benefits, resources and events can continue. Individual membership costs just $50 a year.
Not a GSA member? Join us.
Author
-
Daniel L. Helfrich
Archer Daniels Midland Co.
P.O. Box 1470
Decatur, Illinois 62625 USA
Tagged With
Related Posts
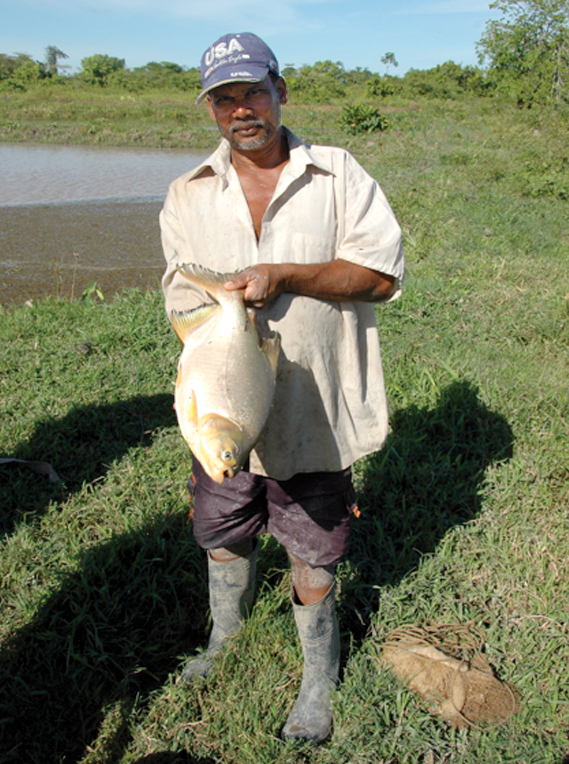
Health & Welfare
A look at aquaculture in Guyana
With its large quantities of water and little industry to pollute it, Guyana has the potential to become a greater player in global aquaculture.

Intelligence
An engineer’s design for a classroom aquaculture-aquaponics system
An aquaponics teaching system was designed, built and operated by students at the University of Arizona, integrating its operation and management into the educational curriculum. This engineering design will require minimum maintenance and will last years.
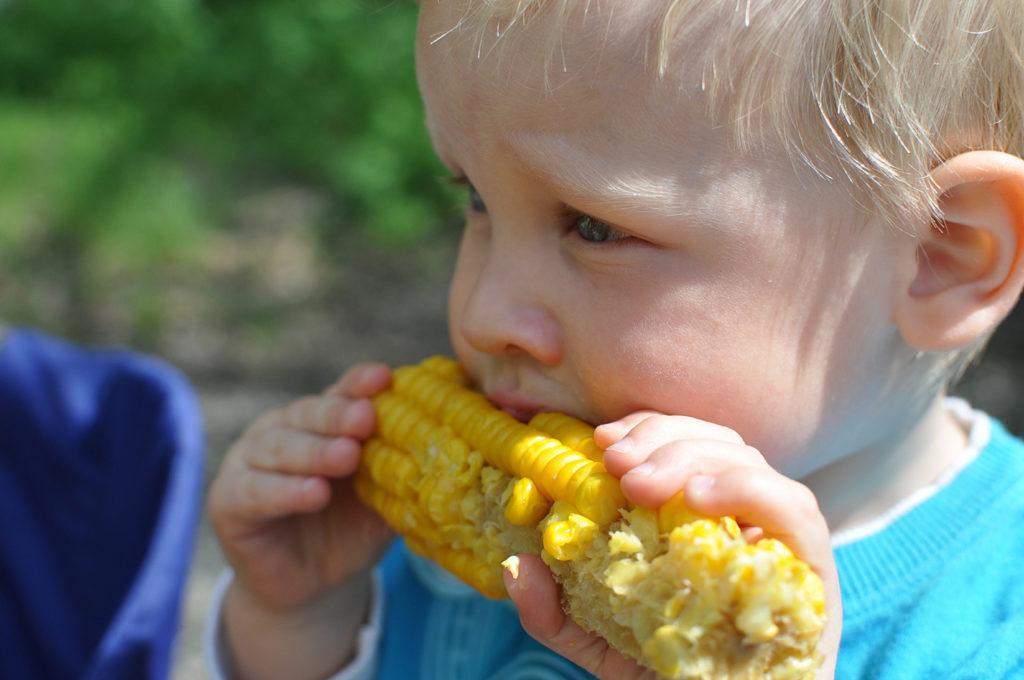
Responsibility
Are global nutritional needs being met?
This study shows that the global agricultural system currently overproduces grains, fats and sugars while production of fruits and vegetables and protein [including seafood] is insufficient to meet the current population’s nutritional needs.
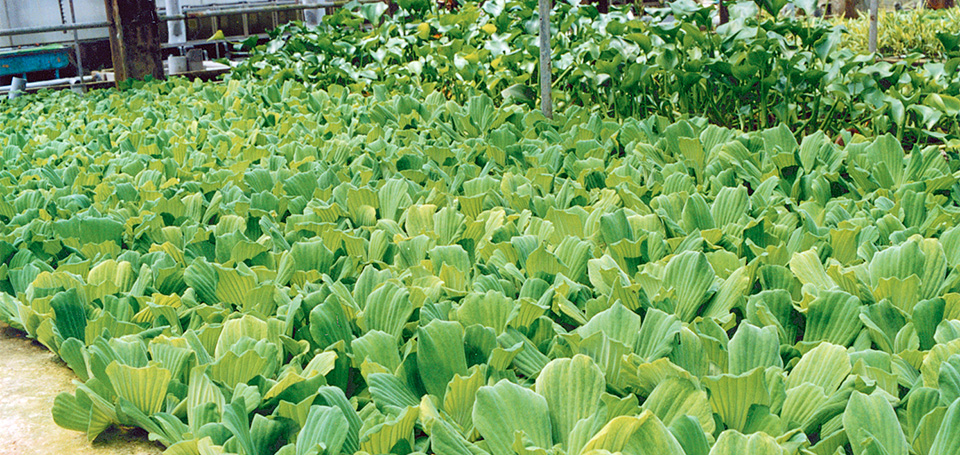
Responsibility
Denitrification in recirculating aquaculture systems: Comparison of aquatic plants
Denitrification by anaerobic bacteria can remove nitrates from RAS, but the operation requires anaerobic conditions and the addition of carbon sources.