Harbor Branch Oceanographic Institution develops low-cost systems

In recent years, researchers in the U.S. have been working to develop indoor recirculating aquaculture systems for production of marine shrimp. These systems are attractive to U.S. shrimp producers, because they allow shrimp to be cultured year round in relatively small areas. Indoor recirculation technology reduces water requirements and discharge from the culture system, minimizing environmental impacts, and offering a high degree of biosecurity. The probability of introducing viral pathogens into indoor recirculation systems supplied with well water and stocked with specific pathogen free postlarvae is minimal. Indoor systems also reduce the risks of predation and accidental introduction of nonnative shrimp into U.S. waters. Despite these advantages, there are still no profitable commercial shrimp production facilities utilizing indoor recirculating technology. The capital cost per kilogram of shrimp produced per year is much higher for these systems than for traditional pond culture systems. Operating costs per kilogram of production are also higher due to the higher energy and labor requirements. The smaller production area and higher capital costs require very high production rates per unit area if these systems are to be profitable.
Research at Harbor Branch Oceanographic Institution

In 1996, work began at Harbor Branch Oceanographic Institution (HBOI) to develop low-cost, economical recirculating systems for producing Penaeus vannamei in freshwater. Initial trials established the technological feasibility of culturing shrimp in hard freshwater (Chloride 300 ppm, Total Hardness 150 ppm). These trials were carried out in single-phase production systems in which shrimp were reared from postlarvae to harvest size in a single culture tank (Fig. 1). Culture tanks were stocked at around 220 shrimp per square meter and harvested after 150 to 180 days, at densities of 135 to 150 per square meter, and with average weights of 15 to 18 grams. Initial economic analyses based on these production levels suggested that commercial facilities utilizing similar single-phase systems are unlikely to be profitable. Singlephase systems utilize space very inefficiently during the first two-thirds of the production cycle, when loading rates are well below the system carrying capacity.
HBOI then set out to develop a more efficient production system to improve the profit potential of tankbased shrimp production. One alternative is to maintain the shrimp at densities much closer to the carrying capacity of the system throughout the production cycle, by utilizing a multiphase production system. Each phase would be allotted an area proportional to the maximum biomass that would be attained in that phase. We applied this concept in the design of a threephase production system (Fig. 1) in which the production cycle was divided into three 60-day phases. In the HBOI system, all three phases of the production cycle take place within a single culture tank, partitioned into nursery, intermediate, and final grow-out areas. The nursery section occupies 10 percent of the total area, the intermediate section occupies 30 percent of the total area, and the final grow-out section occupies 60 percent of the total area. The area harvested is only 60 percentm2 of the area harvested in a single-phase system, but the three-phase system would be harvested three times for every harvest of the single-phase system. Assuming equal growth and survival rates, annual productivity of a threephase system would be 1.8 times higher than that of a single-phase system (0.6 x 3).
System design

In 1998, the Florida Department of Agriculture and Consumer Services (FDACS) funded a study at HBOI to evaluate the economic feasibility of producing L. vannamei commercially in freshwater recirculating aquaculture systems. As part of this study, HBOI set up a comparison of single and three-phase production systems.
The shrimp production systems utilized in the FDACS-sponsored project represent two generations of system design. First generation systems at HBOI (System A) use sand filters for solids removal and biofiltration. Although simple, these systems perform surprisingly well and support loading rates as high as 2.4 kg shrimp per square meter.
However, sand filters are expensive to operate because they require inefficient, high-head pumps to move water through compacted sand filter media and require substantial labor to maintain. The second-generation system at HBOI (System B) have an inground raceway and a low-head water treatment system consisting of a solids filter tank and a moving bed biofilter, both filled with plastic Kaldnes biofilter media. Water enters the tank near the bottom and flows up through a static bed of Kaldnes media, where particulate wastes are trapped. Water flows by gravity out of the solids filter and into the biofilter tank, in which the biofilter media is tumbled by gentle aeration to maintain a thin biofilm on the media surface. A low-head pump returns the water to the raceway.
A 1/4-hp axial flow pump (160 gpm) returns the water to the culture tank in the single-phase systems, while a 3/4- hp low head centrifugal pump (130 gpm) circulates the water in the threephase system. Regenerative blowers were used for aerating the culture tanks. Approximately 0.1 SCFM of air was provided for each kilogram of anticipated biomass.
Space is more efficiently utilized in System B than in System A. The System A greenhouse contains 4 culture tanks separated by an aisle that runs the length of the greenhouse, and a 10-foot filter area in the middle. The culture area occupies only 78 percent of the greenhouse area. The System B greenhouses each contain two culture tanks that span the width of the greenhouse and most of the length of the greenhouse, and share a common interior wall. A catwalk is mounted on top of the interior wall. The culture tanks in System B occupy 90 percent of the greenhouse area.
The culture tanks consist of a wooden frame supporting a black 30- mil high-density polyethylene liner. The tanks are rectangular in shape and are set up in a “racetrack” configuration (Fig. 1). Each culture tank has two drain outlets at opposite ends of the tank and centered between the sidewalls and the end wall. A central baffle extends between the drain outlets dividing the tank down the middle. The water in the culture tank flows in an elongated oval pattern, circling around the drain outlets at the ends of the tank. Corner baffles prevent solids from collecting in the corners of the tank. The semi-circular flow pattern around the drain outlets concentrates the solid wastes around the drain where they exit the tank. The racetrack configuration provides the efficient space utilization of a rectangular tank and the good mixing and solids removal characteristics of a circular tank.
The three-phase culture tanks were partitioned into three separate tanks divided by a shared wall, with an elevation difference of 4 inches between adjacent sections, which allowed the shrimp to be transferred between sections by gravity draining the water through a 4-inch bulkhead fitting.
Single-phase vs. three-phase production trials
A series of paired production trials were carried out, in which the single-phase and three-phase systems were stocked simultaneously with same age, high health PLs, at an average density of 206 PLs per square meter of final grow-out area. This resulted in an average nursery density of 1,236 PLs per square meter in the three-phase tanks. In each trial, the shrimp were harvested after 180 days. The results of the trials are summarized in Table 1. The final project report (Van Wyk et al. 2000) contains a more detailed presentation of the production trial results.
Van Wyk, Comparison of productivity, Table 1
Parameter | Single-Phase | Three-Phase |
---|
Parameter | Single-Phase | Three-Phase |
---|---|---|
Percentage of culture area harvested | 100% | 60% |
Survival (%) | 61% | 77% |
Feed conversion ratio | 1.59 | 1.74 |
Harvest density (shrimp/m2 of area harvested) | 153 | 128 |
Average shrimp weight (g) | 14.1 | 15.9 |
Kg harvested/m2 of area harvested/crop | 2.07 | 2.00 |
Kg harvested/m2 of total area/crop | 2.07 | 1.20 |
Crops/year | 2 | 6 |
Kilograms harvested/m2 of total area/yr | 4.14 | 7.20 |
The average harvest densities of the single-phase and three-phase trials were virtually identical (2.07 kilogram per square meter of harvest area per crop and 2.00 kilogram per square meter harvest area per crop, respectively). The lower survival of the shrimp in the three-phase systems was largely compensated for by the increased weight of shrimp harvested from these systems. All of the culture area was harvested in the single-phase systems, while 60 percent of the total culture area was harvested in the three-phase systems. The harvest density of the three-phase system expressed in terms of kg harvested per unit of culture area was 1.2 kilogram per square meter total area per crop.
Economics

An economic analysis was performed to analyze the profitability of a hypothetical enterprise based on the System B 3-phase design. A 10-year cash-flow model was developed for an enterprise consisting of twelve production greenhouses, an acclimation/quarantine greenhouse, a feed shed, workshop, and three retention ponds.
The production parameters, construction costs, and operating costs for the model were based on the results obtained in the production trials described above. The baseline scenario assumed shrimp could be grown to an average weight of 18 grams in 180 days, with stocking of density of 220 shrimp per square meter of final grow-out area and an average survival of 61 percent. The model further assumed the shrimp would be sold through direct marketing channel as a whole, fresh product for $5.24 per pound of whole shrimp. The initial capital cost for the project totaled $521,000. For the baseline scenario, the breakeven price was $4.59 per pound and the internal rate of return (IRR) for the hypothetical enterprise was 13 percent. Most investors would require an IRR of at least twice this value before they would be willing to consider entering into such a risky venture.
However, sensitivity analyses revealed that if the survival could be increased to 70 percent, or the shrimp could be grown to 18 g in 150 days, the IRR would be doubled. If shrimp could be grown to market size in 150 days with an overall survival of 70 percent, the IRR would increase to a very attractive 48 percent, with a breakeven price of $3.72 per pound. Under this scenario, the shrimp would have to be sold for at least $4.50 per pound of whole shrimp in order to return an IRR of 26 percent, the minimum return necessary to cover the opportunity cost and risk associated with the investment.
Conclusion
Can the technology be improved to allow for the growth rates and survival rates necessary for such an enterprise to be profitable? Recent work at HBOI indicates that growth rates can be improved by removing the shadecloths on the greenhouses to permit algal growth in the culture tanks and that survival in the nursery and intermediate section can be improved by increasing water depth and deploying artificial substrates. Further research will demonstrate if the necessary growth and survival can be achieved with sufficient consistency to support commercialization of the technology. But it is clear from the work already completed that the three-phase production strategy greatly improves our chances of growing shrimp profitably indoors.
Reference
Van Wyk, P., M. Davis-Hodgkins., R. Laramore, K.L. Main, J. Mountain, and J. Scarpa. 2000. Production of Marine Shrimp in Freshwater Recirculating Aquaculture Systems, Florida Department of Agriculture and Consumer Services. Bob Crawford. Tallahasse, Florida.
This is Harbor Branch Oceanographic Institution Contribution No. 1352.
(Editor’s Note: This article was originally published in the June 2000 print edition of the Global Aquaculture Advocate.)
Now that you've reached the end of the article ...
… please consider supporting GSA’s mission to advance responsible seafood practices through education, advocacy and third-party assurances. The Advocate aims to document the evolution of responsible seafood practices and share the expansive knowledge of our vast network of contributors.
By becoming a Global Seafood Alliance member, you’re ensuring that all of the pre-competitive work we do through member benefits, resources and events can continue. Individual membership costs just $50 a year.
Not a GSA member? Join us.
Author
Tagged With
Related Posts
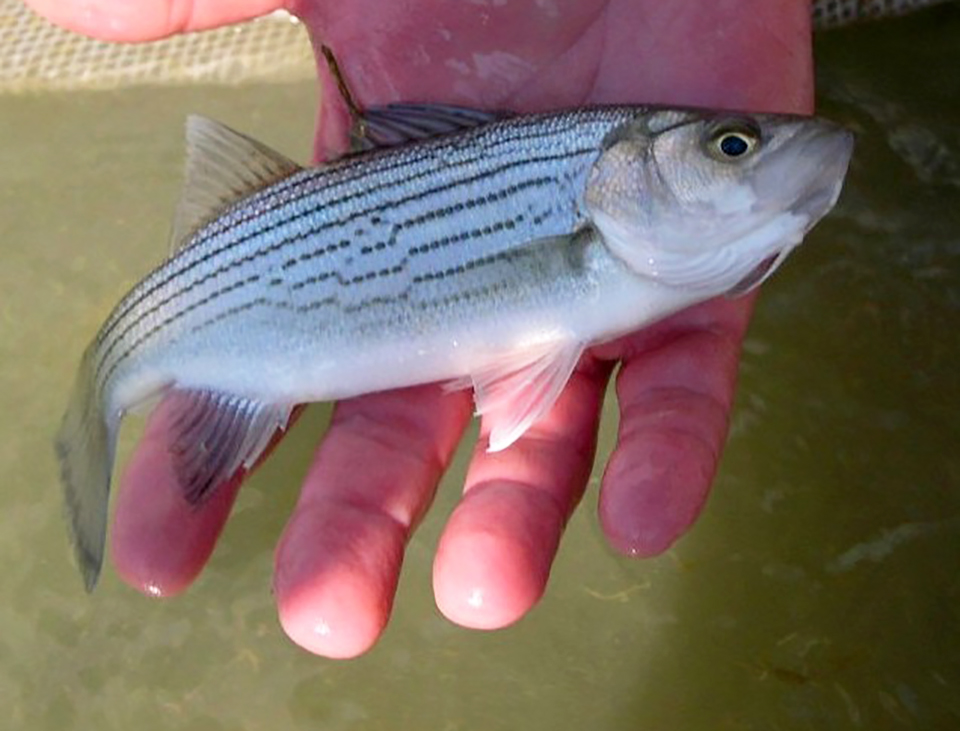
Responsibility
Stocking rate effects on growing juvenile sunshine bass
A dose-response study was conducted in an outdoor biofloc system to begin quantifying the stocking rate production function for sunshine bass advanced fingerlings.
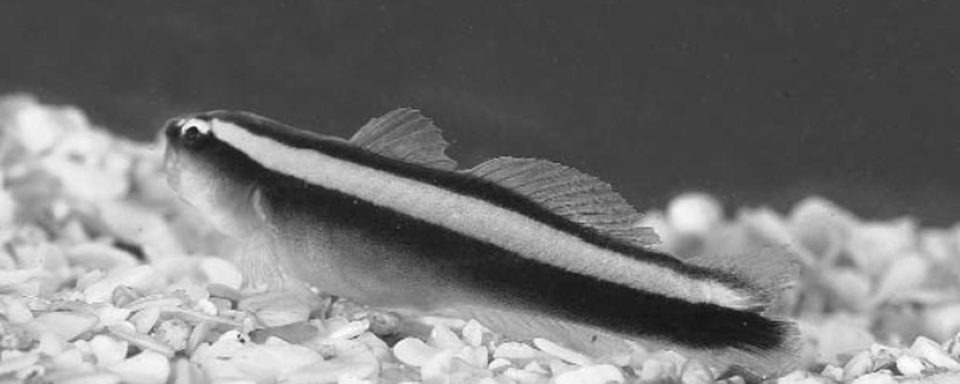
Health & Welfare
Cleaner fish: Neon gobies
Using neon gobies in broodstock maturation tanks as a form of parasite control is an effective alternative to the use of chemical treatments.
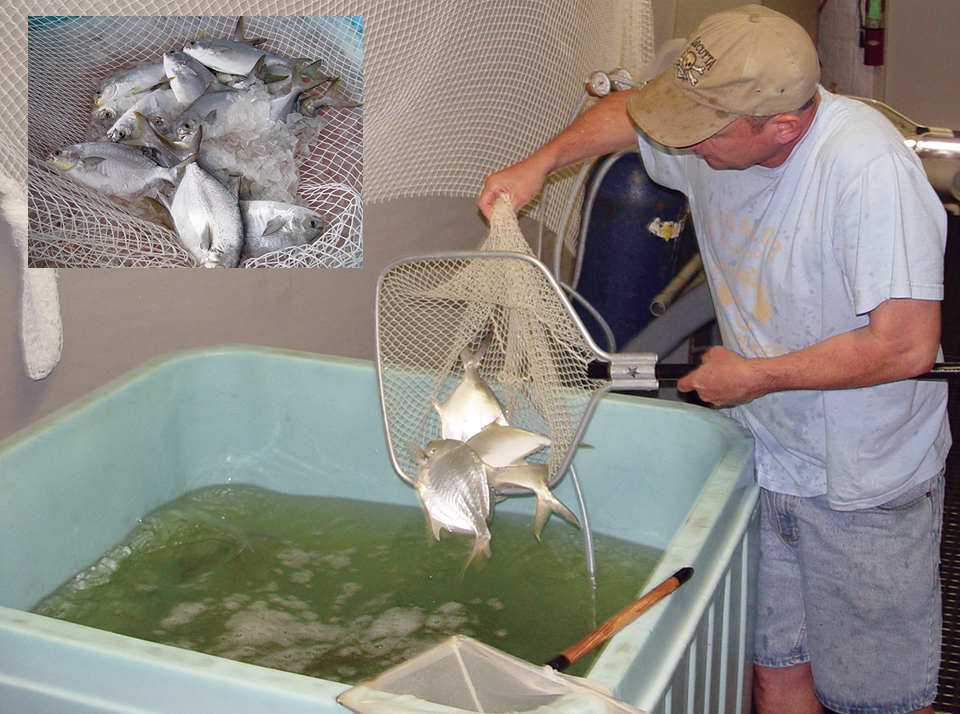
Health & Welfare
Pompano reared to market size in RAS
In a trial, rearing density affected the mean weight and weight gain of pompano, although differences between treatments became apparent toward the end of the study.
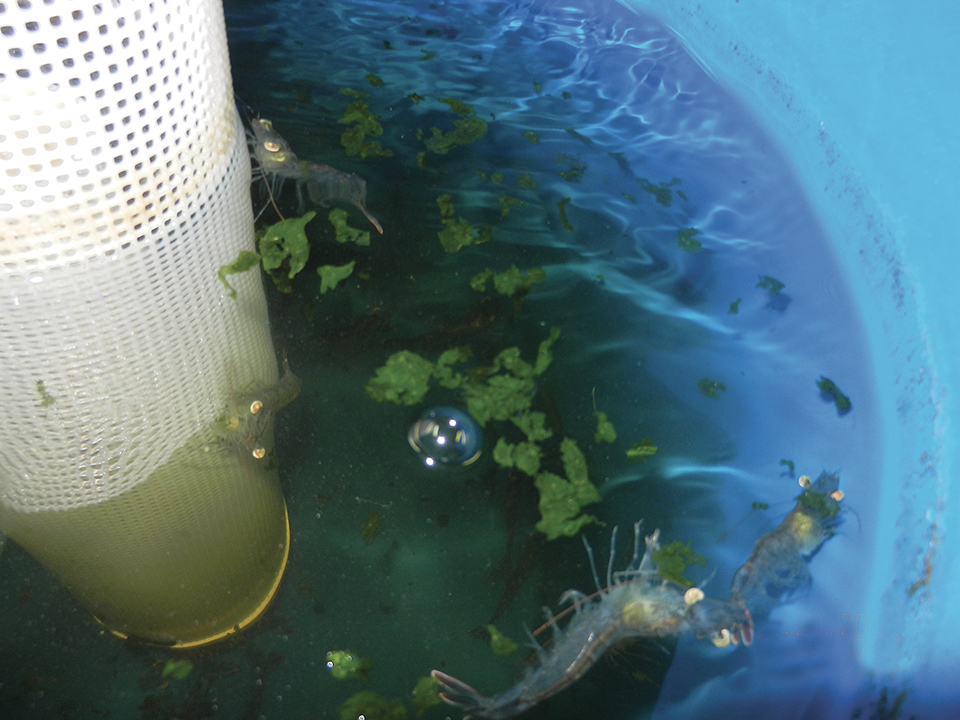
Aquafeeds
Utilization of Ulva lactuca studied in white shrimp diets
Can fresh U. lactuca harvested weekly from a land-based integrated multi-trophic aquaculture system be utilized as a nutritional supplement or partial replacement for pelleted feeds in the production of Litopenaeus vannamei?