Several farms produce in floating cages and earthen ponds, with processing and exporting to the United States

When extensive tilapia culture in Panama started in the 1970s, it was integrated with and dependent on other agriculture and livestock production activities. In the early 1990s, some farmers began developing commercial semi-intensive and intensive operations to produce tilapia in floating cages and earthen ponds, using both pelleted and extruded feeds. Two species are currently produced: tilapia nilotica (Oreochromis niloticus) for filleting and export to the United States, and red tilapia (Oreochromis sp.) mostly for the local, whole fish market.
Floating cage culture
Two projects, both located in Lake Gatún, utilize floating cage technology. One project currently has 14, 40- m3 cages and an annual production capacity of around 200,000 lbs (91 metric tons (MT)), with plans to double or triple its production in the near future.
The other project is a pilot operation sponsored by the local Chinese Technical Mission and the Ministry of Agriculture and Livestock Development (Ministerio de Desarrollo Agropecuario). It has 24 cages and annual production capacity of 300,000 lbs (136 MT). Other trials are under way with floating cages of less than 6 m3, to try to expand cage culture to smaller dams and reservoirs.
Two phases
The production cycle has two phases; one is a nursery and the other a final grow-out to market size. Depending on desired fish size, the cycle lasts seven to 14 months. Population sampling is usually done on a monthly basis. Water quality is monitored throughout the cycle, along with a cage cleaning and maintenance program.
Feeding and production
Commercial meal is used to feed animals up to 30 grams, with 3/16-in floating feeds applied to 300 grams, and 5/16- in feed to harvest. Market size varies 450 to 900 grams, depending on whether animals are to be sold whole or filleted and exported fresh to the U.S.
Pond culture

In 1999, the new Costa Sol Comercial S.A. farm began operations. The farm has 30 ha of ponds (1,000 and 2,000 m2), and a four-phase production system that involves reproduction, nursery, grow-out I and grow-out II.
The nursery phase stocks at 15 fingerlings per square meter (mean weight 1 gram). Fish are culled and moved to grow-out I at 100 grams and a density of 8 fish per square meter. At 250 grams, they are moved to the grow-out II phase and grown at a density of 6 animals per square meter to a market size of 900 to 1,000 grams. This farm uses several commercial feeds, including meals, granules, and floating pellets.
Currently, one of the shrimp farms (Acuícola Las Huabas) that had been converted to tilapia production in 1999 due to White Spot Syndome Virus problems is going back to shrimp production. While in tilapia production, this farm had 100 ha of ponds under semi-intensive, two-phase production of tilapia nilotica. Its nursery system used 1.5-ha ponds, stocked monthly with 250,000 1-gram fingerlings. Upon reaching a mean weight of 150 grams, fish were transferred to 8 to 10 ha grow-out ponds, stocked at 1 fish per square meter and grown to 900 to 1,000 grams in about one year.
Marketing
Various farms producing in ponds process their fish as fresh fillets for export to the U.S. Currently, 35,000 lbs (15.9 mt) are being processed and exported, with deep-skinning fillet yields of 30-31 percent, and size classifications of 3-5, 5-7, and 7-9 oz (85-140 g, 140-200 g, and 200-255 g). Other smaller farms that produce tilapia in earthen ponds sell their fish at an average harvest weight of 450 g on the local market.
Exports
In 2000, Panama exported 159,282 kg of fresh tilapia fillets and 1,814 kg of whole frozen tilapia, worth over U.S. $1 million. During January and February of 2001, exports included 72,224 kg of fresh fillets and 2,379 kg whole frozen tilapia, worth U.S. $464,187, the American Tilapia Association reported. Production from the Costa Sol Comercial farm and the two floating cage projects is processed and exported to the U.S. by Basilio Export and Import.
Conclusion
Commercial tilapia farming is a relatively new industry in Panama, but there are now several farms that produce in floating cages and earthen ponds, with processing and exporting to the United States. The excellent environmental conditions and abundant water resources of the country indicate the industry could significantly expand in the future.
(Editor’s Note: This article was originally published in the December 2001 print edition of the Global Aquaculture Advocate.)
Now that you've reached the end of the article ...
… please consider supporting GSA’s mission to advance responsible seafood practices through education, advocacy and third-party assurances. The Advocate aims to document the evolution of responsible seafood practices and share the expansive knowledge of our vast network of contributors.
By becoming a Global Seafood Alliance member, you’re ensuring that all of the pre-competitive work we do through member benefits, resources and events can continue. Individual membership costs just $50 a year.
Not a GSA member? Join us.
Author
Tagged With
Related Posts
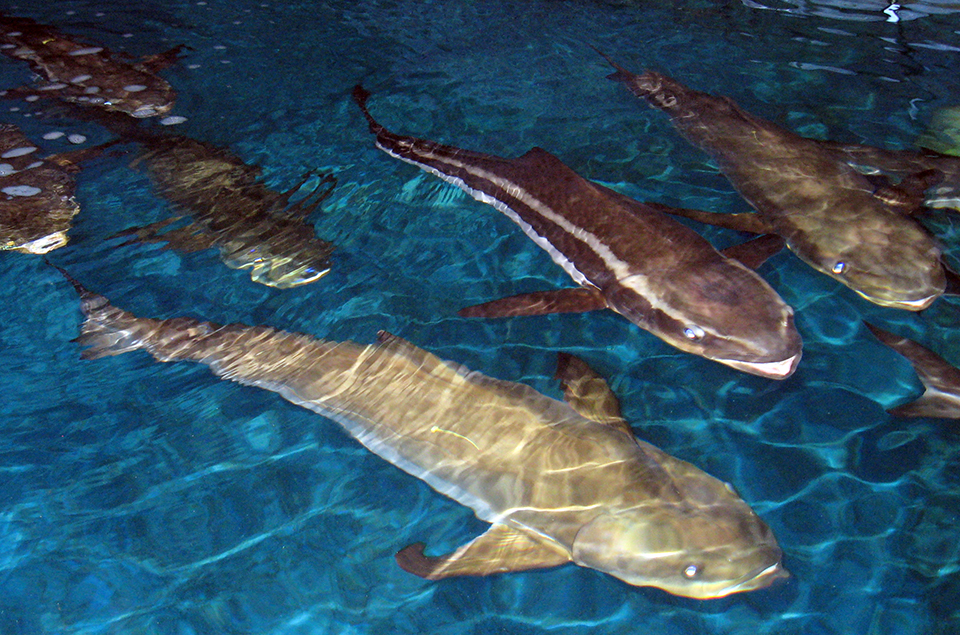
Health & Welfare
Cobia hatchery-to-market technology at UMEH
Cobia is a top emerging candidate for tropical and subtropical marine fish aquaculture. The University of Miami Experimental Hatchery has led ongoing research to advance the viability of raising hatchery-reared cobia.
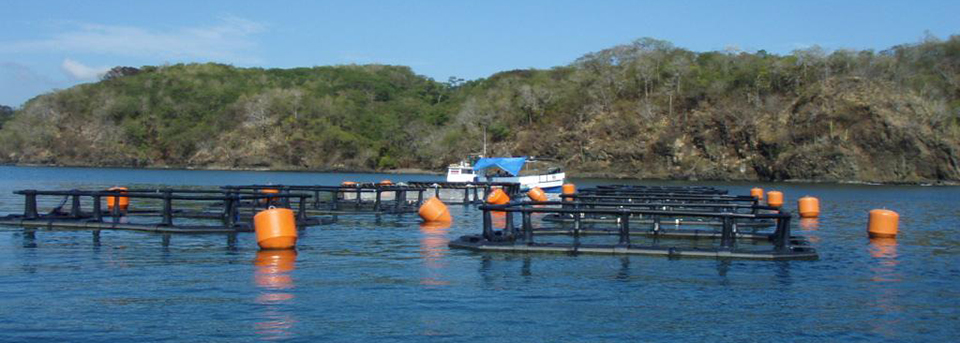
Health & Welfare
Integrated spotted red snapper aquaculture in Central America
The technology for closing the life cycle of spotted red snappers has progressed due to efforts of government and private-sector researchers.

Intelligence
Paradigm shifts in shrimp farming
In the evolution of shrimp farming, white shrimp emerged as the primary species. While some farms in the Americas successfully converted to intensive practices, wide adoption has been limited.
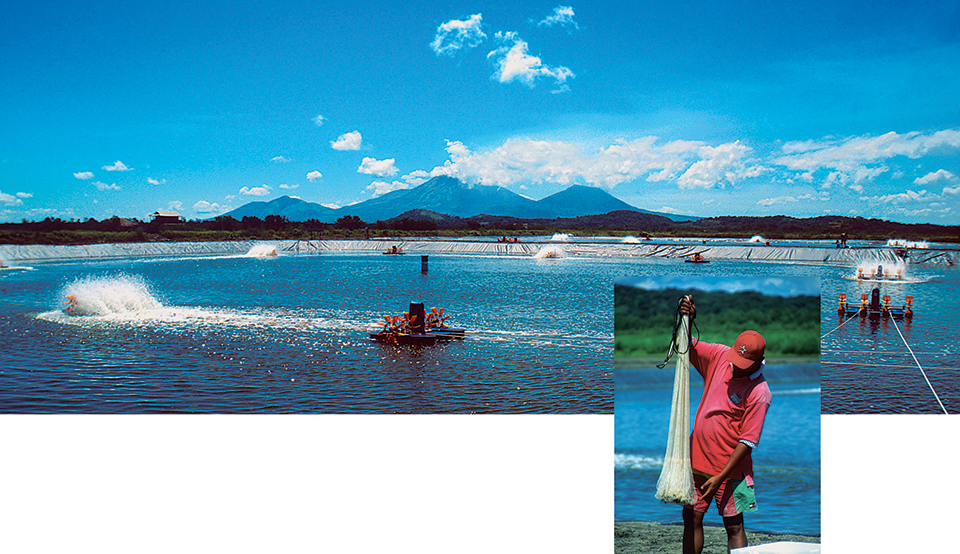
Health & Welfare
Zero-exchange demonstration posts good results in Nicaragua
The Nicaragua Small Shrimp Producer Assistance Program built a closed, zero water-exchange shrimp production system to demonstrate the concepts and practices.