Technologies for large-scale, biosecure nursery culture have matured

Several factors have limited the growth and expansion of the pond-based shrimp-farming industry in the United States. Extensive and semi-intensive pond production systems are typically managed with high rates of water exchange, and this production method raises environmental concerns regarding effluent discharge into receiving water. Pond based culture systems are also typically restricted to coastal regions, where land costs are inherently high.
Another major concern is the limited growing season often found in temperate and subtropical regions. For example, in coastal South Carolina, USA, water temperatures conducive to shrimp production only exist 6 to 7 months per year. This factor restricts overall production and usually allows only one annual crop. Finally, several viral disease outbreaks have damaged pond-reared shrimp in the U.S. and globally.
In response, recent research efforts in the U.S. have focused on the use of greenhouse-enclosed raceways for intensive to superintensive shrimp production.
Greenhouse-enclosed raceways

Greenhouse-enclosed raceways offer several advantages over typical pond-based systems. The raceways can be managed with zero to minimal water exchange, thus greatly reducing environmental impacts due to effluent discharge. Biosecurity protocols can be implemented to manage disease vectors. Greenhouse-enclosed systems also provide opportunities for inland culture operations, and year-round production can be achieved.
Ongoing experiments at the Waddell Mariculture Center in Bluffton, South Carolina, USA, during the last few years have studied the application of super-intensive greenhouse-enclosed raceways for the nursery and grow-out culture of Pacific white shrimp (Litopenaeus vannamei).
System and operational procedures
To date, several juvenile and grow-out production trials have been conducted using pilot- and commercial scale greenhouse-enclosed raceway systems. The pilot-scale system consists of two 55-square-meter HDPE-lined, sediment- free raceways, while the commercial- scale system consists of a single 282-square-meter unit. Each can be equipped with artificial substrates for vertical surface enhancement at a density of about 1 square meter mat per cubic meter of raceway volume.
Aeration and water movement has been supplied by blown air, and 0.75-kw paddlewheel and propeller-aspirator units. Propane-based water heating is achieved using heat-exchange units in situ in the pilot-scale system and externally with a recirculating water pump that also aids in water movement in the commercial-scale system. Temperature is moderated during warmer months via shade cloth covering and thermostat-controlled fans.
Through 2002, no external biological or mechanical filtration has been employed during the production trials. However, during the last grow-out trial in the 282-square-meter commercial-scale system, a 25-cubic-meter bead filter was operated during the latter half of the cycle. Also, in place of the paddlewheel and aspirator units used in previous trials, oxygen supplementation was provided via injection oxygen generator.
Two weeks prior to stocking of PL10-20, raceway units are filled with ultraviolet-sterilized water and fertilized to establish planktonic communities. For juvenile production trials, PL are stocked and reared using standard feeding and husbandry protocols for 25 to 100 days. For the most recent grow-out production trials, 1-gram juvenile animals were stocked at 300 per square meter and reared for 75 to 90 days.
Nursery results
Test results confirm the technical feasibility of these technologies for the nursery production of juvenile L. vannamei (Table 1). Survival of animals in each trial has been over 90 percent, with mean harvest weights exceeding 0.25 grams 30 days after stocking.
McAbee, At-harvest results of greenhouse-based trials, Table 1
Time of Stocking | Stocking Density | Total Days In Raceways | Survival (%) | Mean Individual Weight (g) |
---|
Time of Stocking | Stocking Density | Total Days In Raceways | Survival (%) | Mean Individual Weight (g) |
---|---|---|---|---|
April 2001 | 1,950 PL/m2 | 97 | 98 | 1.01 |
April 2002 | 1,950 PL/m2 | 28 | 97 | 0.55 |
June 2002 | 1,240 PL/m2 | 38 | 97 | 0.31 |
April 2002† | 1,945 PL/m2 | 74 | >90* | 1.00 |
October/2002† | 1,364 PL/m2 | 80 | 98 | 0.90 |
† = Pilot-scale system * = Estimated
As densities increase, the risks associated with mechanical failure increase. This necessitates investment in personnel, and emergency backup and alarm systems to manage the additional risk of catastrophic crop loss. Clearly, however, the technologies for large-scale, biosecure, superintensive nursery culture of L. vannamei have matured to the point where commercial implementation can be quickly implemented with a minimum of risk.
The transfer of juveniles to grow-out systems can be quickly and efficiently carried out. Transfer mortality is minimal, particularly if oxygen is applied during the transfer process.
Advantages vary

The degree of intensification of the nursery can be balanced with factors such as target growth rate and harvest size, capital investments, and application of water treatment and oxygen injection technologies. The advantages of biosecure superintensive nursery systems vary according to the site and type of grow-out operation.
In more temperate zones and areas where shrimp growth improves seasonally, these systems allow growers to gain three to four weeks of growing time by stocking 1-gram juveniles in ponds at the start of the optimal growing season. Typically, postlarvae availability is limited during optimal stocking windows, and the use of the nursery system to “head start” and/or stockpile postlarvae can improve the outlook for stock availability. For operations in which culture can be carried out year-round, the head start system greatly increases farm productivity, allowing more efficient use of space and more annual production cycles, which improves overall returns per unit area.
Health benefits
Holding of stock in raceways for up to 30 days provides a powerful quarantine option to assure animal health before stocking into the farm. This requires proper site selection for the nursery system, and planning and design with an effective health-monitoring protocol, but it can be one of the most important components in an overall disease risk management and farm biosecurity program.
The survival of nursed animals in grow-out is typically much higher and more predictable than that of direct-stocked PL. This allows more efficient feed management and can be an important factor in overall farm profitability. In areas where viral pathogens are endemic, use of nursed juveniles can improve survival rates by allowing the animals to grow larger and improving the condition of the shrimp before exposure to pathogens.
Grow-out results
Five grow-out production trials completed through 2002 in the Waddell Mariculture Center superintensive production systems were reported by Weirich et al. in 2002. The trials demonstrated the biological feasibility of the systems while documenting several bottlenecks that must be overcome for successful commercialization. Although market-size shrimp were produced using minimal exchange systems without external filtration, survival and yield have been inconsistent.
The most important factor in maintaining crop health and growth is adequate supplemental aeration in the system. In some trials, technical difficulties with liner designs or power failures in the absence of proper alarm and backup systems caused catastrophic failures. Clearly, one of the most important guiding principles for the design and implementation of commercial-scale systems must be risk management hrough appropriate engineering technologies and management systems.
Table 2 shows production results for trials 2 and 5. Both trials were stocked at 200 PL8-10 per square meter for a 20-week grow-out cycle. Trends towards increasing production levels and reduced feed-conversion ratios reflected improvements through experience gained in the completion of initial trials. The results suggested the system can operate without outside filtration or water exchange up to a carrying capacity of 3 kilograms per milligram.
McAbee, Harvest results of greenhouse-based trials, Table 2
Parameter | Trial 2: July-November 2000 | Trial 2: July-November 2000 | Trial 5: December 2001-April 2002 | Trial 5: December 2001-April 2002 | Trial 5: December 2001-April 2002 |
---|
Parameter | Trial 2: July-November 2000 | Trial 2: July-November 2000 | Trial 5: December 2001-April 2002 | Trial 5: December 2001-April 2002 | Trial 5: December 2001-April 2002 |
---|---|---|---|---|---|
RW 1 | RW 2 | RW 1 | RW 2 | RW 3 | |
Weight (g) | 19.3 | 18.9 | 14.6 | 15.4 | 17.1 |
Survival (%) | 60.1 | 63.9 | 70.5 | 71.5 | 55.2 |
FCR | 2.8 | 2.8 | 1.8 | 2.0 | 1.9 |
Yield (kg/m2) | 2.3 | 2.4 | 3.1 | 3.3 | 2.8 |
Water quality parameters from trial 5 are shown in Table 3. Water temperatures were maintained at stable optimal levels by the heat-exchange system despite outside temperatures that neared freezing on several occasions. Data on temperature inside and outside the greenhouse and in the raceway, coupled with information on propane usage, will form the basis for system engineering to optimize passive heat gain and provide information for financial feasibility analyses for varying geographical locations.
McAbee, Water quality parameters recorded during L. vannamei, Table 3
Parameter | RW 1 New Water | RW 2 Old Water | RW 3 Pond Water |
---|
Parameter | RW 1 New Water | RW 2 Old Water | RW 3 Pond Water |
---|---|---|---|
Temperature (º C) A.M. | 28.5 (25.7-30.3) | 28.8 (25.7-30.5) | 28.5 (24.2-30.6) |
Temperature (º C) P.M. | 29.5 (26.2-31.1) | 29.8 (25.9-31.1) | 29.7 (25.0-32.7) |
Dissolved oxygen (mg/l) | 6.3 (5.0-7.9) | 6.1 (4.9-7.7) | 5.8 (4.3-7.2) |
Salinity (g/l) | 15.0 (14.3-15.6) | 14.9 (14.1-16.1) | 15.1 (14.6-15.7) |
pH | 7.7 (7.1-8.3) | 7.7 (7.1-8.2) | 7.6 (7.1-8.3) |
Alkalinity (mg/l as CaCO3) | 180 (140-240) | 229 (160-340) | 144 (120-220) |
Total ammonia-nitrogen (mg/l) | 0.01 (0-0.10) | 0.01 (0-0.10) | 0.15 (0-1.80) |
Nitrite-nitrogen (mg/l) | 0.13 (0.03-1.40) | 0.18 (0.03-0.50) | 0.94 (0-7.60) |
Nitrate-nitrogen (mg/l) | 22 (1-38) | 29 (10-40) | 19 (1-40) |
In trial 2 and in raceway 2 in trial 5, water from the previous run was stored at harvest and reused for the subsequent cycle. The reuse of water coupled with a relatively fast turnaround and reflooding around the substrate material resulted in consistently low ammonia and nitrite levels.
In contrast, freshly filled and bloomed tanks or use of new substrates resulted in midseason ammonia increases followed by nitrite spikes. Thus, system designs that reuse water between crops may stabilize microbial communities and associated water quality parameters while enhancing opportunities for the application of these technologies away from the coastal zone.
Results from the most recent grow-out trial continued to demonstrate trends towards improvement in production parameters (Table 4). Production results at harvest reported survival at 91 percent, mean weight at 16.6 grams, feed-conversion ratio of 1.54, average growth per week of 1.44 grams, and yield of 4.50 kilogram per square meter. For this trial, the raceway was stocked with 1-gram juveniles from a nursery system. Together with improved growth rates, grow-out time was reduced to 11 weeks. The use of juveniles may also have contributed to the improvement in survival rates.
McAbee, At-harvest results of greenhouse-based trials, Table 4
Parameter | Value |
---|
Parameter | Value |
---|---|
Weight at stocking (g) | 1.0 |
Final weight (g) | 16.6 |
Total days growout | 76 |
Avg. growth/day (g) | 0.21 |
Avg. growth/week (g) | 1.44 |
Total biomass harvested (kg) | 1,270 |
Kg/m2 | 4.50 |
Survival (%) | 91 |
Total amount fed (kg) | 1,955 |
Feed-conversion ratio | 1.54 |
As described above, important modifications were made to system operations during this trial, including the use of a bead filter and removal of solids during the backwash cycle and injection of oxygen. Fig. 1 shows the growth of the shrimp and system dissolved oxygen levels before and after the addition of oxygen and filtration.

The apparent increase in growth during the latter half of the cycle is in stark contrast to the typical plateau effect observed in previous trials as solid levels continued to increase late in the growing season. The use of oxygen can have positive benefits in terms of improved growth and condition of the target crop, and increased system carrying capacity. However, the negative effects of CO2 buildup and associated pH drops must be addressed.
Preliminary economic feasibility analysis
The economic feasibility of commercial shrimp culture in South Carolina using state-of-the-art indoor recirculating systems has also been initiated. The purpose of the analysis is two-fold: to develop a bio-economic model specific to South Carolina that will assist researchers in investigating the sensitivities of projected profits and risks to various culture techniques and related variables such as market prices, and provide commercial feasibility analysis information germane to private-sector needs.
As an initial starting point of the analysis, a “base case” production system, along with production and economic assumptions, was selected based upon experimental work at the Waddell Mariculture Center (Table 4) and other information sources. The hypothetical base case production unit in the initial analysis was made up of five modules, each of which was comprised of six, 750-square-meter raceways covered by interlinked biosecure greenhouses. It was assumed that seawater would be pumped in from a nearby source, treated, and heated via a heat exchanger system during the colder months.
Major preliminary base case production assumptions included direct stocking of 1-gram shrimp at 300 animals per square meter, overall survival to harvest size of 85 percent, mean harvest size of 17 grams, growth rate of 1.3 grams per week – allowing 4 crops per raceway over 12 months – and 1.50 feed conversion ratio. Major economic assumptions included juvenile stocking costs of U.S. $11.50 per 1,000 and feed costs of $0.50 per kilogram.
The total estimated cost of production was U.S. $4.36 per kilogram, with variable costs making up $3.27 per kilogram. This preliminary analysis indicated one of the most important parameters relative to reducing production costs is growth rate.
For example, maintaining growth at 1.44 grams per week rather than 1.3 grams per week as in the base case scenario would reduce projected total production costs by U.S. $0.21 per kilogram. Consequently, it appears cost-effective techniques that can improve growth rates – such as the selection of fast-growing shrimp strains – could significantly improve the financial performance of biosecure indoor recirculating systems.

Commercial feasibility
The Waddell Mariculture Center prototype systems provide an insight into alternative culture technologies that have the potential to allow development and expansion of the U.S. shrimp-farming industry. By embracing these technologies, the environmental impact of discharged effluents would be reduced or eliminated, biosecurity protocols and procedures could be implemented to prevent the spread of disease agents to and from the culture facility, and year-round culture could be achieved irrespective of location. In addition, systems could potentially be located inland near market centers, opening up new opportunities for value-added fresh or live product sales.
However, in order for greenhouse based minimal-exchange shrimp production systems to be adopted commercially, they must be proven under a research setting to be biologically and economically sound on a consistent basis. To do this, a commercial scale prototype system with a minimum of six raceways to allow controlled studies must be constructed, so that commercial feasibility can be demonstrated while continuing research and development to improve system performance.
Further research
Additional research will be needed to explore the effects of aeration type, water flow patterns, substrates, diets, feeding regimes and other factors. The appropriate use of oxygen supplementation, filtration, and solids removal will require additional replicated studies to develop optimal protocols to assure maximum growth and production with the highest efficiency of protein use. Future studies will also have to address disposal or treatment options for solids removed from these super-intensive systems.
Data obtained from previous, ongoing and future trials is being subjected to appropriate economic feasibility analyses to develop baseline cost and return information. This data will be reported and used to project the profitability of various multiunit culture system layouts and drive the establishment of ongoing research.
Conclusion
The commercial development of greenhouse-enclosed super-intensive shrimp culture is favorable in the United States, but will remain dependent upon the research and development of cost-effective production techniques coupled with marketing approaches that buffer U.S. shrimp farm products from the vicissitudes of major U.S. shrimp market segments, especially those subject to import-induced price reductions.
Note: Cited references are available from the second author.
(Editor’s Note: This article was originally published in the June 2003 print edition of the Global Aquaculture Advocate.)
Now that you've reached the end of the article ...
… please consider supporting GSA’s mission to advance responsible seafood practices through education, advocacy and third-party assurances. The Advocate aims to document the evolution of responsible seafood practices and share the expansive knowledge of our vast network of contributors.
By becoming a Global Seafood Alliance member, you’re ensuring that all of the pre-competitive work we do through member benefits, resources and events can continue. Individual membership costs just $50 a year.
Not a GSA member? Join us.
Authors
-
Brad J. McAbee
Waddell Mariculture Center
South Carolina Department of Natural Resources
P.O. Box 809
Bluffton, South Carolina 29910 USA -
Craig L. Browdy, Ph.D.
Waddell Mariculture Center
South Carolina Department of Natural Resources
P.O. Box 809
Bluffton, South Carolina 29910 USA -
Raymond J. Rhodes
Waddell Mariculture Center
South Carolina Department of Natural Resources
P.O. Box 809
Bluffton, South Carolina 29910 USA -
Alvin D. Stokes, Ph.D.
Waddell Mariculture Center
South Carolina Department of Natural Resources
P.O. Box 809
Bluffton, South Carolina 29910 USA
Related Posts
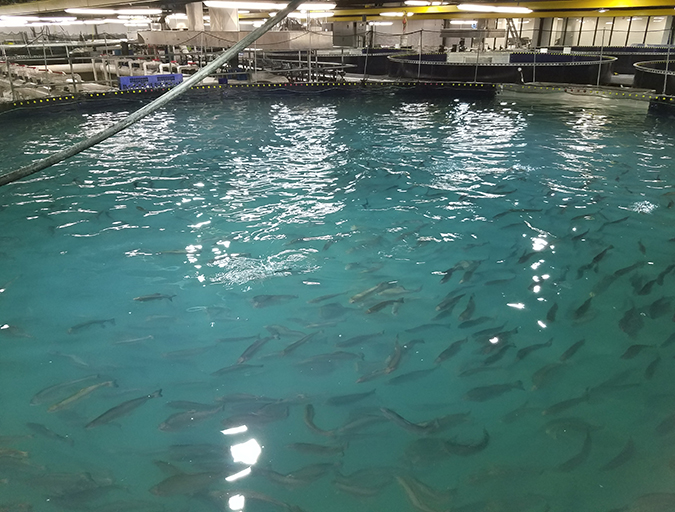
Intelligence
A land grab for salmon (and shrimp) in upstate New York
The operators of Hudson Valley Fish Farm see their inland locale as a pilot to prove that land-based fish farming, located in close proximity to major metropolitan markets, can be successful.
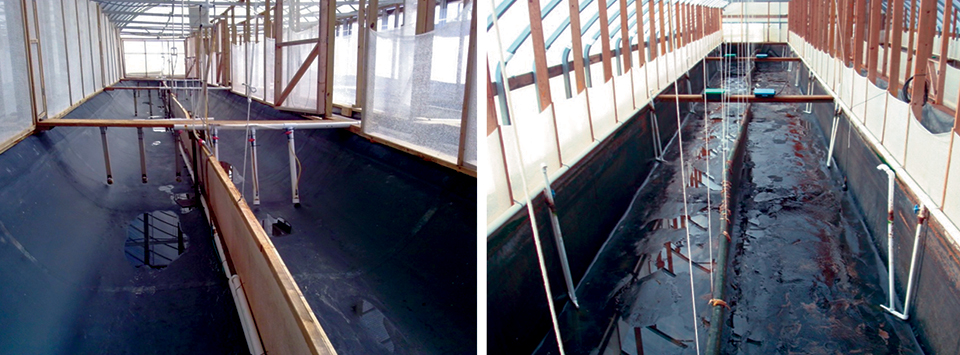
Responsibility
Advances in super-intensive, zero-exchange shrimp raceways
Research at the Texas AgriLife Research Mariculture Laboratory is investigating ways to improve the economic viability of super-intensive raceways for shrimp production.
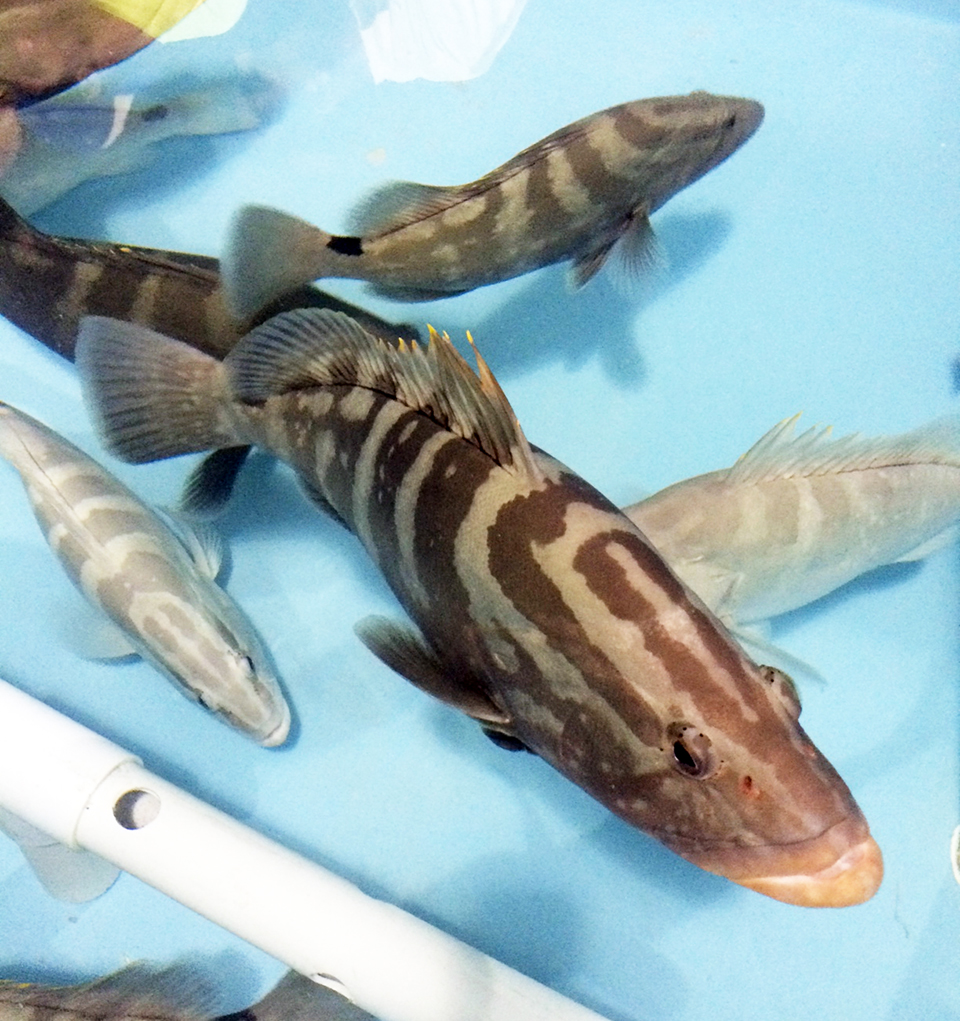
Intelligence
Bahamas venture focuses on grouper, other high-value marine fish
A new venture under development in the Bahamas will capitalize on Tropic Seafood’s established logistics and infrastructure to diversify its operations from processing and selling wild fisheries products to include the culture of grouper and other marine fish.
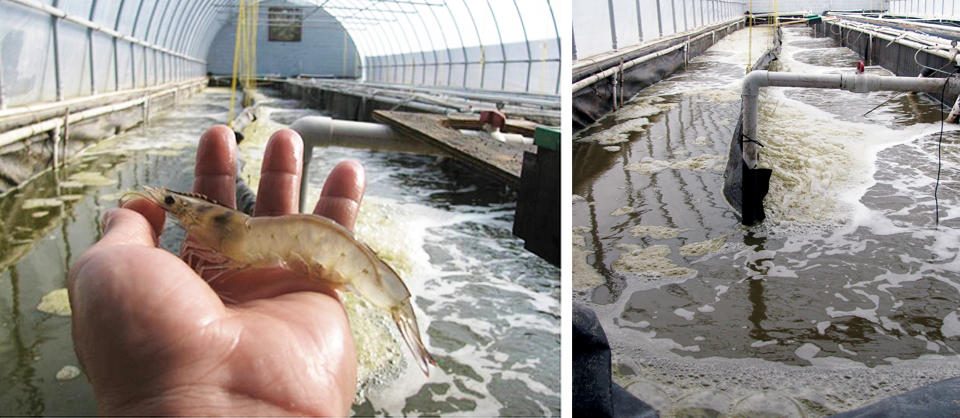
Health & Welfare
Biofloc trial results in fast shrimp growth, low FCR, high survival
A trial in a lined, greenhouse-enclosed raceway evaluated the use of a heterotrophic biofloc system equipped with aeration, supplemental oxygen injection and centralized heating to achieve good shrimp production.