Study in Australia keys on aeration, pumping demands

Shrimp aquaculture in Australia began around three decades ago, when farmers followed the model pioneered in Taiwan and then Thailand by largely stocking Penaeus monodon semi-intensively in earthen ponds on coastal land in or near estuaries. After starting down that path, rising production costs and import competition have required the farmers to use more, not less, total energy to further improve their production efficiency.
Today, many farms produce 10 metric tons (MT) per hectare (ha) per crop of shrimp, when 2 or 3 MT/ha may once have been the norm. Since having more shrimp raises the need for more aeration and water exchange, added energy is not wasted, it simply scales to the larger size of modern crops. Under these circumstances, rising energy costs are addressed by closer scrutiny of energy use during production, as well as attention to the origin of the electricity.
The authors studied six intensive shrimp farms in Australia to better understand their energy needs and examined how they might improve consumption and energy efficiency as well as approach alternative energy generation on the farms. This work was supported by the Australian Prawn Farmers Association and the Australian government’s Farm Ready program. While the findings are of most relevance to Australia, placing these results in a global context reveals how intensification and farming innovation have already triggered large shifts in shrimp farm energy efficiency.
Sources of energy demand
Energy consumption on Australian farms was dominated by electricity, although obviously some liquid petroleum gas or diesel fuel was used for heating in hatcheries or processing. The average farm electricity footprint was scaled to production at 6.5 MWh/MT shrimp.
Aeration dominated the direct energy budget for a shrimp farm in Australia (Table 1), but the lack of pandemic shrimp pathogens in Australia, coupled with careful regulation of farm discharges, means that pumping for seawater exchange to a level specific to each location continues. As farms in Australia also tend to be large – up to 70 ha in pond area – they also typically process product on site.
Paterson, Estimated contribution of production functions. Table 1
Demand | Energy Footprint (MWh/MT) | Comments |
---|
Demand | Energy Footprint (MWh/MT) | Comments |
---|---|---|
Aeration | ~ 4-5 | Peaking at ~ 15 kW/ha |
Aeration | ~ 4-5 | 1.5 kW – Paddlewheels |
Aeration | ~ 4-5 | 1.5 kW – Aspirators |
Pumping | ~ 1 | Scaled to farm size ≥ 5 kW/ha |
Processing | ~ 1 | Freezing, chilling, ice making and air-conditioning |
Green energy
A 50-hectare intensive shrimp farm in Australia demands a supply of about 1 MW of electricity from the distribution grid. Farms typically use emergency diesel generators to supply this demand during weather-related blackouts, but perhaps they can divert money from future rising power bills into “green” energy on farm.
Even with today’s technology, a nearby 1-MW biomass-fueled power station could probably compete successfully with grid electricity. But can enough fuel – sugar cane trash, for example – be diverted from nearby agriculture? Otherwise, an intensive farm’s need for constant aeration is not a natural fit with solar photovoltaic or wind power.
Ironically, large users like shrimp farms with a relatively steady demand may be among the last to cut the umbilical connection to the grid. Green energy comes into contention far sooner for small users, like households that already pay higher tariffs because their demand often fluctuates a great deal through the day.
Aeration, pumping
Aeration remains an important area where efficiencies may be gained. Given that aerators operate continuously for long periods, it is possible to calculate electricity use simply using the total length of the crop and the average number of kilowatts used per hectare. The value for the total harvest can be converted to an electricity footprint (Table 2).
Paterson, Examples of pond aeration footprints, Table 2
Production Year | Duration (days) | Average Crop Aeration (kW/ha ) | Electricity Demand (kWh) | Crop Harvested (mt/ha) | Electricity Footprint (kWh/mt) |
---|
Production Year | Duration (days) | Average Crop Aeration (kW/ha ) | Electricity Demand (kWh) | Crop Harvested (mt/ha) | Electricity Footprint (kWh/mt) |
---|---|---|---|---|---|
2000 | 130 | 4.6 | 14,263 | 3.8 | 3,753 |
2010 | 130 | 10.0 | 31,200 | 8.0 | 3,900 |
As seen in the table, the average aeration footprint for farms in Australia over the last decade has been sitting just below 4 MWh/MT. To reduce this would take a significant improvement in aerator efficiency.
A pressing problem in Australia is that pumping spikes that coincide with high tide incur steep cost penalties from electricity providers. So while pumping is generally a small fraction of the electricity use, under some circumstances, it can represent up to half of the annual electricity bill. Overseas experience has shown that stopping pumping to maintain biosecurity certainly improves the energy efficiency of intensive Litopeneaus vannamei production, but can the practice become routine for farming Penaeus monodon?
Energy use at P. monodon farms
Growing a 10-MT crop of black tiger shrimp, P. monodon, in Australia requires about 40 MWh of aeration. This value is close to average in terms of published data on energy use for shrimp production in other countries (Fig. 1). This graph shows, as one would expect, that a highly intensive crop in a 1-ha pond needs more energy than a less-intensive crop. However, the overall fitted slope is not the most interesting feature.

1 = L. vannamei, Colombia (1994)
2a = P. monodon, Thailand (2010)
2b = L. vannamei, Thailand (2010
3 = L. vannamei, Mexico (2001)
4 = L. vannamei, China (2011)
5 = P. monodon, Taiwan (1989)
6 = L. vannamei, Belize (2002)
The variation shows that the energy footprint for growing a given tonnage of shrimp in a 1-ha area has fallen 10 to 20 MWh in the last three decades. This even occurs in the semi-intensive part of the curve, where historically the size of the crop had little bearing on the energy use.
Even though global shrimp production has been rising, the industry is using energy more frugally. The near-mandatory switch to zero-exchange production of L. vannamei for biosecurity contributed to the overall improvement in efficiency. While the shrimp biomass:aeration ratio is quite favorable for L. vannamei, the reduced pumping energy accompanies shorter crop times and (ideally) reliable survival from high-health postlarvae.
Reading the figure, if yield falls unexpectedly – due to disease, for example – in a pond at a fixed level of aeration, then the MWh/MT value will deteriorate (shift left). Importantly, the reverse holds true to a point if yield can be increased under a fixed amount of aeration, say through higher stocking levels or survival.
Of course, unless better aerators with superior standard aeration efficiency are adopted, this last point was only possible because the broader demands of circulation and mixing in lightly stocked ponds meant that aeration sometimes exceeded the needs of the intended shrimp biomass. There was “room” to squeeze more shrimp into the pond.
The future
There may be limits to how far energy use at P. monodon farms can be pushed down into “vannamei” territory. The fortunate lack of pandemic shrimp diseases in Australia has reduced the biosecurity imperative for zero-exchange farming. Yet the price signal from electricity companies is telling farmers to find alternatives to high-volume pumping, or at least find a cheaper way to continue using exchange pumps.
While black tiger shrimp culture may not benefit as much from biofloc production in terms of aeration and energy use as L. vannamei farming does, partial implementation of floc principles is already showing promise for P. monodon. In the meantime, energy use will at least keep moving in the right direction if new feeds and genetic selection can keep yield high and crop duration as short as possible.
(Editor’s Note: This article was originally published in the November/December 2014 print edition of the Global Aquaculture Advocate.)
Now that you've reached the end of the article ...
… please consider supporting GSA’s mission to advance responsible seafood practices through education, advocacy and third-party assurances. The Advocate aims to document the evolution of responsible seafood practices and share the expansive knowledge of our vast network of contributors.
By becoming a Global Seafood Alliance member, you’re ensuring that all of the pre-competitive work we do through member benefits, resources and events can continue. Individual membership costs just $50 a year.
Not a GSA member? Join us.
Authors
-
Brian Paterson
Bribie Island Research Centre
Queensland Department of Agriculture, Fisheries and Forestry
P. O. Box 2066
Woorim, Queensland 4507 Australia -
Sarah Miller
CSIRO Energy Flagship
Clayton South, Victoria, Australia
Tagged With
Related Posts
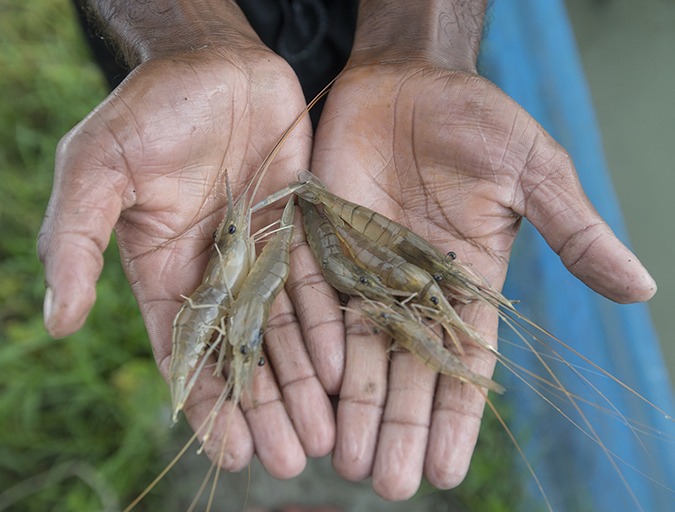
Innovation & Investment
Australia incentivizing innovation in aquaculture
A government-funded $3 million (AUS) project by innovationXchange, WWF and others seeks transformative solutions from entrepreneurs for small-scale producers in the Indo-Pacific region. The competition’s three challenges include fresh thinking on feed, “new ocean products” and sustainable design.
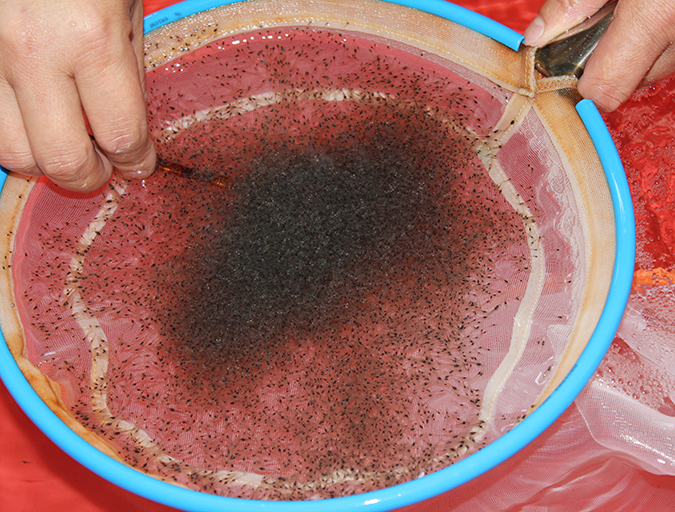
Health & Welfare
Acclimating shrimp postlarvae before pond stocking
Shrimp postlarvae acclimation before stocking into the various growout systems (ponds, raceways, tanks) is a critical – and often overlooked, sometimes taken for granted – step in the shrimp culture process. Various water quality parameters should be changed slowly so that the young shrimp have the time to gradually adapt to the new conditions.
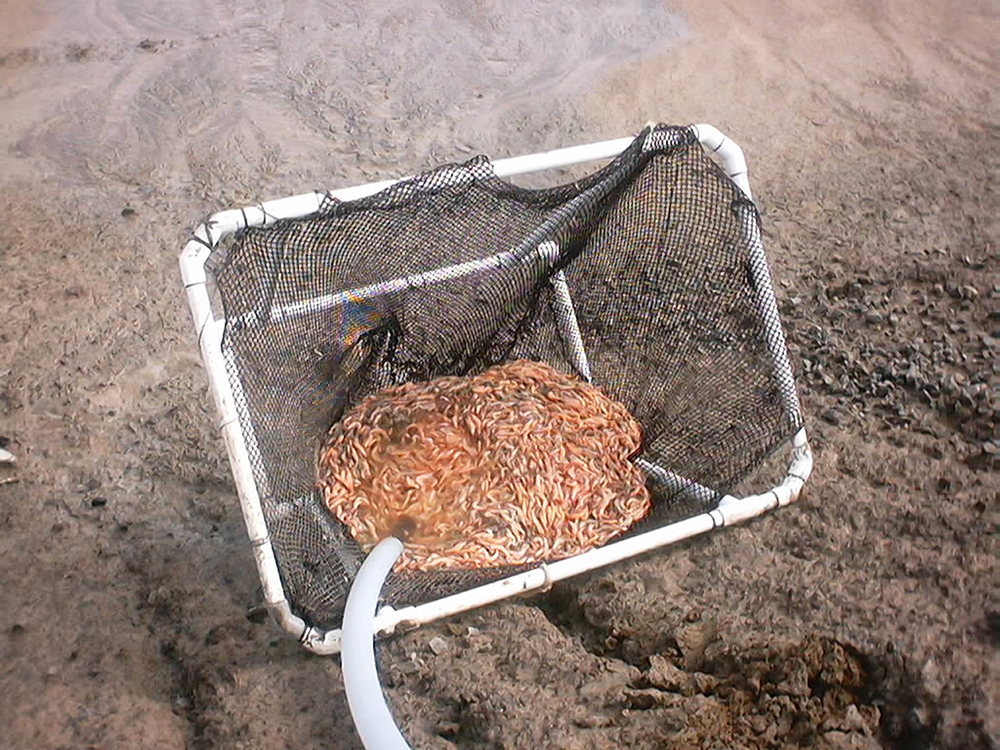
Aquafeeds
Biosecurity protocols needed for shrimp feeds, feeding practices
Shrimp aquafeeds – live, fresh or formulated – should not be an entry point of potential pathogens to the shrimp and/or to their culture systems.
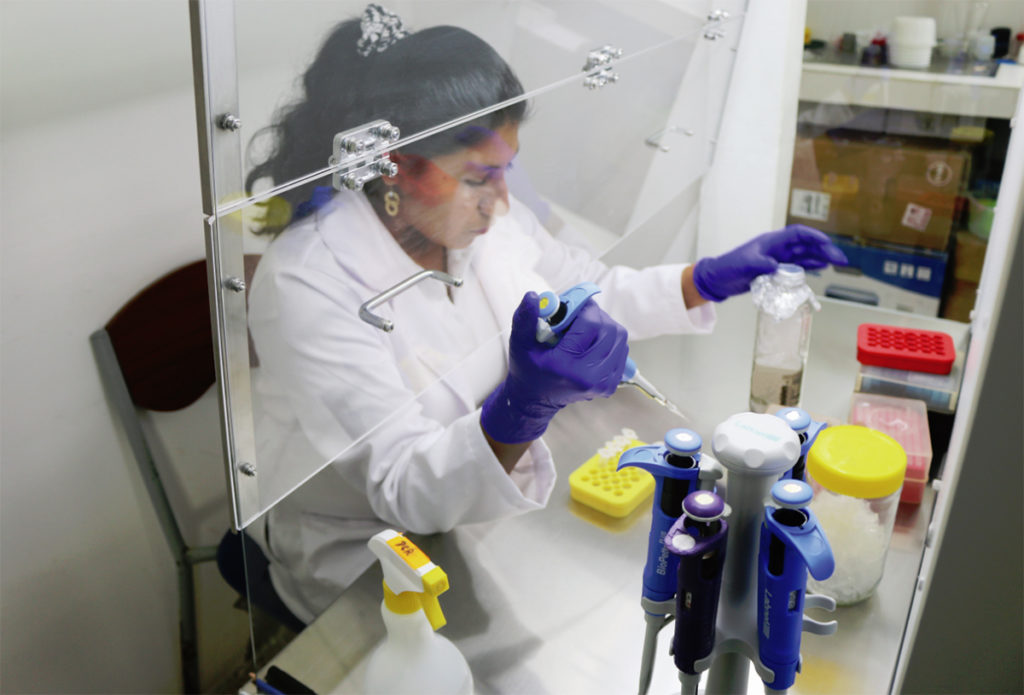
Health & Welfare
Asepsis key to prevent contamination in shrimp hatcheries
Maintaining biosecurity and asepsis in larval shrimp production is a key component of the production chain in Ecuador, which requires the production of 5.5 billion larvae monthly from 300-plus hatcheries.